1. INTRODUCTION
In road design on low-bearing capacity fine soils, stabilization techniques are frequently employed to improve their geotechnical properties and increase strength. Among the traditional stabilization methods, various chemical additives are used. Rivera et al. [1] reviewed traditional methods, mentioning disadvantages such as negative environmental impact and high costs. The current trend in construction is to develop sustainable solutions that contribute to environmental conservation and are cost-effective, leveraging waste from industrial, artisanal, or agricultural activities, that generates in the locations where the works are located.
In Peru, technical specifications for road design [2] consider subgrade strength determined by the California Bearing Ratio (CBR) ASTM 1883 test [3], with a minimum CBR value of 6% for 95% of the maximum dry density of the Modified Proctor test. It is common for fine soils such as high plasticity clays and silts in saturated conditions not to reach fail the minimum required strength. In Cajamarca, Perú, there are areas undergoing economic and social development that require road construction [4]. In these locations, low-bearing capacity fine soils predominate, and artisanal brick kilns utilizing mineral coal from regional deposits are located [5]; the combustion of mineral coal in the kilns produces bottom ash (BA) as a residue. In the present study, BA generated by artisanal kilns was used as the main additive for the treatment of fine soil subgrades, with Type I Portland cement employed as a secondary additive.
The soil treatment began with the identification of its physical and chemical properties, along with those of the BA. Several mix combinations were prepared, evaluating the resulting physical and mechanical changes. To enhance strength, cement was added, achieving proportional increases based on the percentage used (see sections 3.2 and 3.3). Curing was essential to promote pozzolanic activity, and saturation was used to evaluate strength under adverse conditions. The CBR test was adequate for measuring the expected strength levels in the treated soil, without aiming for high strength or stiffness requiring additional tests.
The purpose of adding cement in this research was to improve the soil's strength with a small amount of cement, sufficient to activate the pozzolanic reaction with the BA and increase the soil's CBR, making it suitable as a subgrade. An economical and sustainable alternative is proposed, utilizing a higher proportion of locally available BA.
2. BACKGROUND
The use of ashes in road construction has primarily been applied in various pavement layers. Lyn et al. [6] conducted a study with comprehensive information on the use of BA derived from municipal waste incineration in several European countries. They reported that it has been used for decades with favorable outcomes in base layers, subbase layers, road surfaces, and embankments, being adding naturally and as part of hydraulic and asphaltic mixtures.
The nature of BA influences its physical and chemical properties. According to Abdullah et al. [7], these properties primarily depend on the type of coal used in combustion, which influences its affinity when mixed with soil and other considered additives, mentioning furthermore the importance of harmonizing these properties with the projected use.
The use of secondary additives to enhance the effect of ash has been addressed in several studies. Osinubi K. [8] utilized cement (2%-8%) and pulverized coal bottom ash (5%-30%) in stabilizing black tropical clays from Nigeria, resulting in a significant increase in CBR value from 9% to 130%. Lime is another secondary additive used alongside ash, where the results are influenced by the proportion of lime and curing time. Bhurtel A. and Eisazadeh A. [9] incorporated an equal amount of lime into two different proportions of BA from a power plant to increase the strength and durability of Bangkok clay in Thailand. They found that the curing time depends on the proportion of BA used.
The use of rice husk ash (RHA) combined with cement has also shown favorable results. Sana F. and Haq F. [10] presented the treatment of soil from Pakistan classified as A-4, with RHA ranging from 5% to 20% combined with 3% and 6% of cement, and they reported the highest strength increments with 15% RHA and 6% cement. Basha et al. [11] reported strength enhancement and reduction of plasticity in stabilizing residual soil from Malaysia, recommending the use of 6% to 8% cement and RHA in 10% to 15% proportions.
The combination of two types of ashes was reported by Krishnan et al. [12], employing BA from a thermal power plant and sugarcane bagasse ash. Adding 3% cement, they found favorable results in stabilizing expansive soil.
Research results using cement as a secondary additive show a proportional increase in strength relative to the cement content; low contents, such as 2% used by Osinubi [8] and 3% used by Sana and Haq [10], were sufficient to increase the strength of stabilized soil, while Basha et al. [11] reported better results with 6% cement.
The PCA manuals [13], [14] define cement-modified soil (CMS) as soil to which a small amount of cement (usually 2% to 4%) is added, resulting in permanent benefits such as increased CBR. However, when a higher cement content is added, a rigid material with greater strength is obtained, known as cement-stabilized soil (CSS). For this case, there are standards and design protocols, such as ASTM methods [15], [16], [17], which include procedures for evaluating the properties of stabilized soil, such as strength, durability, and others.
3. METHODOLOGY
3.1 MATERIALS
FINE SOIL: The soil used originates from the Cajamarca region in Perú, whose location is shown in Fig. 1. It is a typical material found in various locations where pavements are projected to replace current unpaved roads, similar as shown in Fig. 2a). The Table I shows the soil characterization, classified according to the Unified Soil Classification System (USCS) as elastic silt (MH) with high plasticity. In the AASHTO classification system, it belongs to subgroup A-7-5 (27) wich represents a low-quality material as a subgrade, with 2% CBR value. Its chemical composition, expressed in oxides, is predominantly composed of silicon oxide and aluminum oxide. Fig. 3 shows the fine soil used in the research
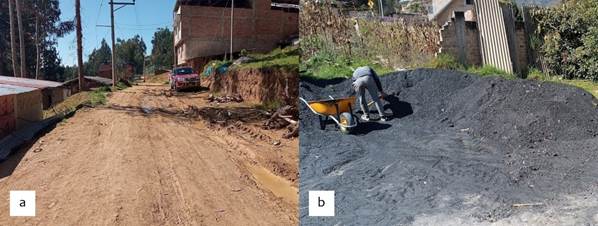
Fig. 2 a) Unpaved road located in Cajamarca, with fine soils at the subgrade level.; b) Mineral coal used in the combustion of artisanal kilns, which generates bottom ash.
TABLE I Fine soil characterization
Property | value |
Particles size distribution | |
Gravel content, % | 0 |
Sand content, % | 13.2 |
Finer < 75mm, % | 86.8 |
Liquid limit, % | 64 |
Plastic limit, % | 40 |
Plasticity index, % | 24 |
Specific gravity of soil solids | 2.693 |
USCS classification | MH (limo elastic) |
AASHTO classification | A-7-5(27) |
Maximum dry density (MDD), g/cm3 | 1.610 |
Optimum water content (OWC), % | 21.3 |
CBR at 100% MDD, % | 2.10 |
CBR at 95% MDD, % | 2.00 |
pH | 7.06 |
Organic matters on ignition, % | 1.37 |
Main chemicals compounds in oxides | |
SiO2, % | 50.636 |
Al2O3, % | 33.335 |
Fe2O3, % | 9.618 |
BOTTOM ASH (BA): BA comes from artisanal brick-making kilns that use mineral coal in combustion. Fig. 4.a) and Fig 2b) show the mineral coal, locally known as "stone coal", used by brickyards in Cajamarca, which is classified between the bituminous and anthracitic ranges. Fig. 4.b) displays a sample of BA extracted from the kilns, the overall sample presented isolated pieces of mineral coal measuring 1 to 2 inches in size. Fig. 4.c) depicts the material sieved through the No. 4 mesh, which was utilized in the tests.
TABLE IIpresents the characterization of the BA, classified according to the SUCS system as SM silty sand and in the AASHTO system as A-2-4(0). It is a non-plastic and lightweight material, with a specific gravity of soil solids at 2.448.
Chemical composition analysis showed that the oxides SiO2, Al2O3, and Fe2O3, which influence its pozzolanic property, represent more than 90% of the total.
TABLE II Bottom ash characterization
Property | value | |
Particles size distribution | ||
Gravel content, % | 0 | |
Sand content, % | 69.9 | |
Finer < 75mm, % | 30.1 | |
Liquid limit, % | NP | |
Plastic limit, % | NP | |
Plasticity index, % | NP | |
Specific gravity of soil solids | 2.448 | |
USCS classification | SM (silty sand) | |
AASHTO classification | A-2-4(0) | |
pH | 6.94 | |
Organic matters on ignition, % | 0.98 | |
Main chemicals compounds in oxides | ||
SiO2, % | 61.619 | |
Al2O3, % | 29.089 | |
Fe2O3, % | 2.908 |
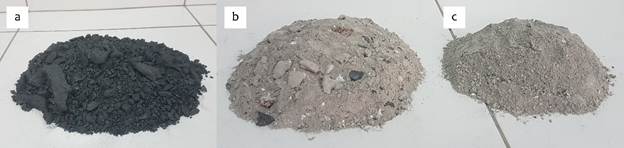
Fig. 4 a) Mineral coal used in combustion; b) Overall sample of bottom ash extracted from the kilns; c) Bottom ash sample sieved through No. 4 mesh for use in the tests.
CEMENT: Portland cement with the commercial name "Cemento Sol Tipo I" was used, which meets ASTM C-150 [18] and NTP 34.009 [19] technical specifications. A typical chemical composition of the product meeting manufacturer specifications is shown in TABLE III.
3.2 SAMPLE PREPARATION
The soil was air-dried and sieved through a No. 10 mesh, while the BA was sieved through a No. 4 mesh, and isolated pieces of coal were removed. The materials were stored separately in airtight bags. Before mixing the soil and BA, their moisture contents were determined for weight corrections.
For the preparation of the soil and BA mixture, the necessary amount of each material was weighed for dosages of 10%, 15%, 20%, 25%, and 30% of BA relative to the total dry weight. The materials were carefully mixed until a uniform material was obtained, and the quantity prepared was in accordance with the type of test.
For the mixtures of soil, BA, and cement, the soil and BA were initially mixed according to the previous step, and the moisture content of the soil-BA mixture was determined. Then, the necessary amount of the soil-BA mixture and cement for the desired dosage was weighed considering dry weights. Subsequently, it was carefully mixed, placed in airtight bags, and left to rest to allow moisture to equilibrate among all materials before conducting the tests.
3.3 TEST PROCEDURES
Physical characterization: The index properties of the soil, BA, and soil-BA mixtures in proportions of 10%, 15%, 20%, 25%, and 30% BA were determined through particles size analysis, Atterberg limits, and specific gravity of soil solids tests. Additionally, the USCS and AASHTO classifications of each soil-BA combination were determined.
Compaction tests: The Modified Proctor method ASTM D1557 [20] was employed for the fine soil and the soil-BA combinations. The maximum dry density (MDD) and the optimum moisture content (OMC) were determined. Compaction was conducted in 5 layers using a modified hammer with a mass of 10 lb and a drop height of 18 inches.
California Bearing Ratio test (CBR): The ASTM D1883 method [3] was employed with three specimens compacted in 5 layers with 56, 25, and 10 blows per layer, respectively, with the compaction moisture content close to the previously determined OMC using the Modified Proctor test.
In a first group, soil samples with BA additions in proportions of 10%, 15%, 20%, 25%, and 30% were tested. The compacted specimens were saturated by immersion in water for seven days before the penetration test.
In a second group, soil samples with BA and cement additions were tested. To determine the appropriate range of cement, pilot tests were conducted with tentative cement dosages, revealing that the desired increase in CBR was achieved with dosages between 1% and 4% of cement. Definitive tests were conducted with 1.0%, 1.5%, 2%, and 4% cement combined with variable percentages of BA.
After compacting the CBR specimens in molds, they were left to cure in a humid environment for seven days. Subsequently, they were immersed in water for an additional seven days, and penetration tests on the molds were carried out according to ASTM D1883 method.
X-ray diffraction (XRD) and X-ray fluorescence (XRF): X-ray diffraction (XRD) analysis was conducted to identify the chemical compounds and crystalline phases of the soil, BA, and soil-BA-cement mixture. Additionally, X-ray fluorescence (XRF) spectrometry was used to identify the oxide composition and chemical elements. The initial chemical composition of the individual materials allowed for the assessment of mineralogical changes in the stabilized soil due to the pozzolanic activity of the treatment.
4. RESULTS AND DISCUSSION
4.1 CHARACTERIZATION OF SOIL AND BOTTOM ASH(BA) MIXTURE
TABLE IVshows the modification of soil properties according to the percentage of BA added. In Fig. 5a). a moderate reduction in the content of fines that pass the No. 200 sieve is observed, Fig. 5. b) shows the reduction of the liquid limit and the plastic limit; for 30% BA this reduction represents 23% for the liquid limit and 46% for the plasticity index. These changes contribute to the improvement of the geotechnical properties of the fine soil.
4.2 COMPACTION OF SOIL AND BOTTOM ASH MIXTURES
In TABLE V, the results of compaction using the modified Proctor method are presented. For the natural soil, a maximum dry density (MDD) of 1.610 g/cm³ and an optimum water content (OWC) of 21.3% were obtained. In the soil and BA combinations, it was observed that both MDD and OWC decrease as the proportion of BA increases.
Fig. 6a) illustrates the Water content - Dry density curves, showing a decrease in OWC with increasing BA content. The decrease in MDD is attributed to the low specific gravity of soil solids of BA at 2.448. In Fig. 6b) the reduction in MDD and specific gravity of soil solids with increasing BA is observed.
According to TABLE V and Fig. 6a), the OWC of the various BA proportions varies between 21.3% for natural soil and 19% for 30% BA. This indicates a minor variation of 3% in OWC across all tested BA combinations. These OWC values were considered as reference points in the compaction of CBR specimens.
4.3 CBR IN SOIL AND BA MIXTURES
The CBR results (in soaked condition) have been considered for 0.1 inch penetration and values for 100% MDD and 95% MDD of the modified Proctor. In subgrade, the CBR 95% MDD is considered.
The swelling and initial dry density correspond to the mold with the highest compacting energy with 56 blows per layer.
TABLE VIpresents the CBR results in soil mixtures with 0%, 10%, 15%, 20%, 25%, and 30% BA. Regarding these results:
The CBR values (95%MDD) in all BA combinations are like those of the natural soil; for 30% BA, the CBR only increased from 2.0% to 2.4%. This increase is not significant and does not meet the minimum required CBR for subgrades.
The soil expansion decreased with the addition of BA. In the natural soil without additives, a swelling of 9.9% was obtained, and as BA was added, the swelling decreased moderately. At 30% BA, which was the highest BA content added, a swelling of 6.1% was obtained, representing a 38% reduction.
TABLE VI CBR results - soil and BA mixtures
BA % | Initial dry density g/cm3 | Initial water content, % | Swelling % | CBR (100%MDD) % | CBR (95%MDD) % |
0% | 1.606 | 20.9 | 9.9 | 2.1 | 2.0 |
10% | 1.600 | 20.5 | 9.7 | 2.2 | 2.0 |
15% | 1.606 | 20.5 | 8.7 | 2.2 | 2.0 |
20% | 1.610 | 19.9 | 7.4 | 2.6 | 2.4 |
25% | 1.602 | 19.5 | 6.5 | 2.6 | 2.5 |
30% | 1.582 | 18.7 | 6.1 | 2.6 | 2.4 |
4.4 CBR IN SOIL, BA AND CEMENT MIXTURES
In TABLE VII, the CBR results are presented for mixtures with cement additions at 1.0%, 1.5%, 2.0%, and 4.0%, with varying percentages of BA. Regarding these results:
-With 1% cement and 10% BA, a CBR of 6% was obtained, which is the minimum required value for subgrades. With 1% cement and 25% BA, a CBR of 9.9% was obtained, slightly surpassing the minimum requirement.
-In tests with 1.5% cement, the CBR values met the requirements across all BA percentages. For samples containing 1.5% cement and BA between 15% and 20%, CBR values exceeding 13% were obtained. In addition, improved stability as a subgrade was observed by reducing expansion.
-With 2% cement, significantly higher CBR values than those required were obtained, ranging from 17.2% to 84% for BA contents between 10% and 30%, respectively.
-With 4% cement and 25% BA, the resulting material exhibited high resistance, with CBR exceeding 100% and typical stiffness of soil-cement stabilization. These results surpassed the objective of improving the soil for subgrade use, with only a small amount of cement and higher BA content.
-Expansion decreased with cement and BA content. With 2% cement and 25% BA, swelling was zero. With 4% cement, total swelling control was achieved, even without BA.
In Fig. 7, CBR results from various combinations of soil, BA and cement are presented. Fig. 7a) displays the results at 95% of the maximum dry density, which are considered in the evaluation of subgrade strength. In 7b), the results at 100% of the maximum dry density, measured using the mold with 56 blows per layer, compacted with the energy of the modified Proctor, are shown.
The swelling recorded in the molds with 56 blows per layer and its CBR value (100% MDD) are displayed in Fig.8for each percentage of cement with varying BA; it is observed that increasing the amount of BA and cement increases the CBR value and reduces swelling.
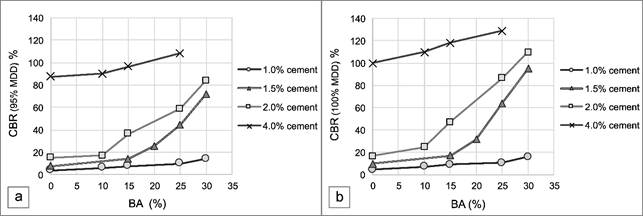
Fig. 7 Results of CBR tests of various combinations of soil, BA y cement. a) CBR at 95% MDD, considered as subgrade resistance; b) CBR at 100% MDD
4.5 CHEMICAL PROPERTIES
The changes in the soil's chemical composition depend on the proportions of BA and cement. TABLE VIIIshows the chemical composition in oxides obtained by XRF spectrometry for the soil, BA, and a mixture of soil + 20% BA + 1.5% cement. The combined SiO2, Al2O3, and Fe2O3 oxides from the BA amount to 93.616%, which is a significant value influencing the chemical reaction with cement and leading to the improvement of the soil's geotechnical properties.
TABLE IXpresents the elemental chemical composition determined by X-ray fluorescence (XRF) method, revealing that silicon (Si) is the main element in all materials: 56.806% in BA, 43.977% in the soil, and 47.720% in the soil mixture with 20% BA and 1.5% cement.
The chemical compounds of the soil and BA obtained by X-ray diffraction analysis (XRD) are shown in TABLE X. Silicon oxide (SiO₂) or quartz, is the main component in both materials: the soil contains 43.78% and the BA 49.29%.
In TABLE XI, the chemical compounds identified in the mixture of soil with 20% BA and 1.5% cement are presented. The mineral compounds of silicon oxide are quartz and cristobalite, representing 54.89%. Fig. 9 shows the respective XRD diffractogram.
TABLE VIII Chemical composition in oxides
Oxide | Soil % | BA % | Cem % | Soil+20%BA +1.5%Cement, % |
SiO2 | 50.636 | 61.619 | 19.79 | 53.262 |
Al2O3 | 33.335 | 29.089 | 6.15 | 28.996 |
Fe2O3 | 9.618 | 2.908 | 2.82 | 9.160 |
MgO | 2.035 | - | 3.16 | 1902 |
K2O | 1.199 | 0.718 | 0.96 | 1.173 |
TiO2 | 1.044 | 1.035 | - | 1.186 |
CaO | 0.85 | 1.576 | 63.2 | 2.358 |
SO3 | 0.662 | 1.518 | 2.58 | 1.040 |
P2O5 | 0.387 | 0.326 | - | 0.225 |
MnO | 0.154 | 0.036 | - | 0.199 |
V2O5 | 0.049 | - | - | - |
SrO | 0.031 | 0.068 | - | 0.048 |
ZnO | - | 0.787 | - | 0.397 |
Na2O | - | - | 0.28 | - |
PbO | - | 0.301 | - | - |
CuO | - | 0.018 | - | - |
ZrO2 | - | - | - | 0.055 |
Rb2O | - | - | - | 0.001 |
TABLE IX Elemental chemical composition
Elements | Soil % | BA % | Soil+20%BA +1.5%Cement % |
Silicon, Si | 43.977 | 56.806 | 47.720 |
Aluminum, Al | 30.473 | 26.817 | 29.415 |
Iron, Fe | 16.42 | 5.63 | 12.280 |
Magnesium, Mg | 2.761 | 0 | 2.199 |
Potassium, K | 2.221 | 1.527 | 1.867 |
Titanium, Ti | 1.399 | 1.624 | 1.363 |
Calcium, Ca | 1.383 | 2.952 | 3.230 |
Sulfur, S | 0.572 | 1.491 | 0.798 |
Phosphorus, P | 0.384 | 0.368 | 0.332 |
Manganese, Mn | 0.284 | 0.075 | 0.295 |
Strontium, Sr | 0.064 | 0.157 | 0.078 |
Vanadium, V | 0.061 | 0 | 0 |
Zinc, Zn | 0 | 1.814 | 0.246 |
Lead, Pb | 0 | 0.696 | 0 |
Copper, Cu | 0 | 0.043 | 0 |
Zirconium, Zr | 0 | 0 | 0.077 |
Rubidium, Rb | 0 | 0 | 0.001 |
TABLE X Chemical composition of soil and bottom ash
Chemical compounds of soil | % |
Silicon oxide (quartz), SiO2 | 43.78 |
Potassium oxalate, K2C2O4 | 17.24 |
Potassium aluminum silicate (sanidine) KAlSi3O8 | 12.67 |
Aluminum phosphate, AlPO4 | 11.49 |
Iron oxide (magnetite), Fe3O4 | 9.87 |
Sodium iron oxide chloride oxalate hydrate, Na2Fe2O(C2O4)2Cl2(H2O)4 | 3.81 |
Iron oxide (hematite), Fe2O3 | 1.13 |
Chemical compounds of bottom ash | % |
Silicon oxide (quartz), SiO2 | 49.29 |
Aluminum, calcium and sodium silicate (Albite) Na0.685 Ca0.347 Al1.46 Si2.54 O8 | 33.53 |
Silicon Aluminum Oxide (Mullite), Al4.54 Si1.46 O9.73 | 7.98 |
Aluminum phosphate, AlPO4 | 7.56 |
Iron oxide (hematite), Fe2O3 | 1.36 |
Magnesium iron silicone hydroxide, Fe6.5 Mg0.5 (Si8O22(OH)2) | 0.28 |
TABLE XI Chemical composition mixture: soil + 20%BA +1.5 cement
Chemical compound mixture | % |
Silicon oxide (quartz), SiO2 | 51.66 |
Iron oxide (hematite, Fe3O3 | 1.69 |
Silicon oxide (cristobalite), SiO2 | 3.23 |
Sodium, calcium, aluminum and silicon oxide (Anorthite), Ca2.133Na1.867) (Si10.003Al5.987) O32 | 7.45 |
Potassium, aluminum, iron and silicon oxide hydroxide (Muscovite), KFe0.12Al2.88Si3O10(OH)2 | 29.32 |
Silicon Aluminum Oxide Hydroxide (Kaolinite), Al2(Si2O5(OH)4) | 6.64 |
4.6 PROPORTION OF ADDITIVES FOR SOIL TREATMENT
The requirement for treated soil is a minimum CBR of 6% (95% MDD). An economically and environmentally sustainable technical alternative is achieved by adding 1% cement and 25% BA, resulting in a CBR of 9.9%. With 1.5% cement and BA percentages ranging from 15% to 20%, better benefits are obtained in the treated soil, such as reduced expansion and higher CBR values, which will contribute to the economic aspect of pavement design. TABLE VIIpresents other possible combinations that may be suitable for other projects.
CONCLUSIONS
The treatment of a fine soil with high plasticity, classified as A-7-5(27), with low-bearing capacity and a CBR of 2% in soaked condition, was investigated. It does not meet specifications requiring a minimum CBR of 6% in subgrades. For soil improvement, bottom ash (BA) from mineral coal and a small amount of Type I Portland cement were used. The principal conclusions are as follows:
-Trials using BA as the sole additive didn't exhibit a significant strength increase; with 30% BA, the CBR value only increased from 2.0% to 2.4%. The addition of cement had a notable impact; even a small quantity facilitated the pozzolanic reaction with the BA, resulting in an increase in soil strength. The CBR value increased, surpassing the minimum requirement.
-The required strength in the treated soil was achieved with low cement dosages. With 1% cement and 25% BA, a CBR of 9.9% was obtained, increasing to 14.1% with 30% BA. With 1.5% cement and 15% BA, a CBR of 13.7% was achieved, and with 30% BA, the CBR increased to 72%.
-Additional benefits were obtained with 1.5% cement in the treated soil. The minimum CBR was achieved with all BA proportions, and for BA contents between 15% to 20%, there was a greater reduction in swelling. Furthermore, the higher CBR values obtained contribute to the economic aspect of pavement design.
-In tests with BA as the sole additive, although a significant increase in CBR was not achieved, there was an improvement in the soil's physical and geotechnical properties due to a reduction in plasticity and fines content. With 30% BA, the liquid limit (LL) decreased from 64% to 49%, the plasticity index (PI) decreased from 24% to 13%, and the fines content < 75μm decreased from 86.8% to 71.0%.
ACKNOWLEDGEMENTS
The authors express their gratitude to the Research Institute of the Faculty of Civil Engineering UNI for their support in this work; likewise, they extend their gratitude to the Soil Mechanics and Chemistry laboratories of FIC UNI for their assistance during the execution of the experiments.