Servicios Personalizados
Revista
Articulo
Indicadores
-
Citado por SciELO
Links relacionados
-
Similares en SciELO
Compartir
Industrial Data
versión impresa ISSN 1560-9146versión On-line ISSN 1810-9993
Ind. data vol.26 no.2 Lima jul./dic. 2023 Epub 20-Dic-2023
http://dx.doi.org/10.15381/idata.v26i2.24717
Production and Management
Motivation Program to Reduce Occupational Accidents in a Manufacturing Company
1Industrial engineer from Universidad Continental (Huancayo-Peru). Currently working as occupational health and safety specialist at CNCH (Medellín-Colombia). E-mail: greysisantillan@gmail.com
the purpose of this research study was to determine whether implementing a motivation program could lead to a reduction in the rate of occupational accidents in the bakery plant of a manufacturing company based in Lima. The study followed a quasi-experimental approach and used a pretest/posttest design with a single group and a sample of 117 workers. The data collection methods included statistical data on work-related accidents, direct observations in the workplace, recording and monitoring of interactions, and a motivation questionnaire. The research results revealed that implementing the IPLEFOR motivation program-which spanned 21 months-led to a 100% reduction in the accident rate. Consequently, it led to a significant improvement in the occupational health and safety system.
Keywords: motivation; safety; intervention; occupational accidents
INTRODUCTION
Occupational safety and health (OSH) is a major concern worldwide, as evidenced by the statistics presented by the International Labour Organization in its Statistics on safety and health at work. Non-fatal occupational injuries total around 50,876 accidents per 100,000 workers (ILOSTAT, n.d.). Sadly, Peru is no exception, as it has a high rate of occupational accidents. The Sistema Informático de Notificación de Accidentes de Trabajo, Incidentes Peligrosos y Enfermedades Ocupacionales - SAT [Computerized System of Notification of Occupational Accidents, Hazardous Incidents, and Occupational Diseases] reported 3,323 notifications up to the end of February 2020, representing a 14.7% increase over the previous year’s rate. Furthermore, January 2020 saw an 8.7% rise compared to the previous year. Of the total notifications, 97.5% were for non-fatal work accidents, followed by 0.57% for fatal accidents. In total, (non-fatal and fatal) accidents make up about 98% of all reports, while incidents and occupational diseases constitute only 1.75% and 0.21%, respectively. Additionally, when considering the type of economic activity, manufacturing industries have the highest accident rate at 22.81%, followed by real estate activities at 17.33%, transportation at 12.43%, and construction at 11.80% (Ministerio de Trabajo y Promoción del Empleo [MTPE], 2020).
According to the SAT, Metropolitan Lima has reported the highest number of notifications for non-fatal and fatal occupational accidents, accounting for 72.5% of the total notifications nationwide. Callao comes in second with 372 notifications, representing 11.3% of the total. Piura has 160 notifications, representing 4.8%, and Arequipa has 152 notifications, representing 4.5%. These three regions account for 11.6% of the total number of workers on the electronic payroll (MTPE, 2020). It should be noted that these figures are solely from formal companies. The actual figures would be higher if the existing informality in Peru was considered since many accidents go unreported. Therefore, the issue of occupational accidents is critical and needs immediate attention.
It is evident from statistics that occupational health and safety are critical factors in ensuring safe work environments. The physical surroundings and mental demands of the workplace have a significant impact on the well-being of workers. Occupational accidents, unfortunately, come at a high social, human, and economic cost. When an accident occurs at work, it affects the injured person, their family, and everyone involved in the organization. Employers are responsible for ensuring the safety of their workers because the effects of occupational accidents are not limited to financial losses but also have emotional consequences for workers. These emotional consequences can adversely affect the productivity of the organization (Salinas, 2018; González et al., 2016).
Occupational accidents pose an imminent risk for all organizations. Therefore, to establish an effective safety culture, the focus should be on accident prevention. Previous studies have attempted to address this issue by improving physical and/or mechanical conditions through the implementation of technical improvements or redesign controls (Denton, 1986). However, since no significant changes were achieved through the improvement of working conditions, research shifted towards analyzing the behavior of workers concerning safety (Islas & Meliá, 1991).
The manufacturing company under study has an accumulated accident report spanning from 2014 to 2017. The report indicates that the number of accidents has been steadily increasing over the last three years, as shown in Figure 1.
All plants have reported accidents, but the bakery plant has the highest number. As shown in Figure 2, the number of accidents in the bakery plant has also been increasing in the last three years.
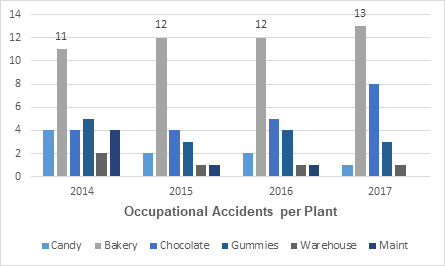
Source: Prepared by the author.
Figure 2 Number of Occupational Accidents per Plant Between 2014-2017.
Upon analyzing the accumulated accidents in the bakery plant (Figure 3), it can be observed that 77% of the accidents that occurred between 2014 and 2017 were caused by unsafe acts. This result is consistent with the findings of several studies on occupational accidents, which suggest that technical control alone is not sufficient to prevent accidents. It has been established that 90% of occupational accidents are caused by unsafe behaviors (Heinrich et al., 1980). This baseline research reinforces the above-mentioned studies.
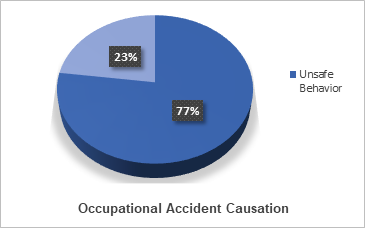
Source: Prepared by the author.
Figure 3 Accident Causation in the Bakery Plant Accumulated Between 2014-2017.
Meliá’s workplace safety tri-conditional model was used to establish the main accident causes related to personal factors. According to this model, for workers to work safely, they must be able to work safely, know how to work safely, and want to work safely. As a result, they will prevent accidents and will feel motivated to use safe practices. As shown in Figure 4, 81% of accidents that occurred between 2014 and 2017 were due to a lack of motivation. This indicates that people are not motivated enough to follow safety standards.
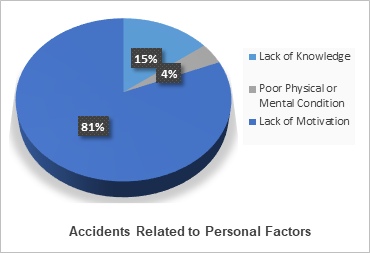
Source: Prepared by the author.
Figure 4 Accidents Resulting from Personal Factors at CNCH Between 2014-2017.
After collecting data related to the causes of accidents in the case study, a new intervention proposal was developed. The proposal includes a motivation program tailored to the specific needs and requirements of the plant under study. This research provides innovative information that will enrich the concepts of motivation and safety. In the absence of such research, the Identification of Critical Processes, Participatory Leadership, Empowerment of Facilitators, Achievement Orientation and Recognition (IPLEFOR, by its Spanish acronym) motivation program offers a new strategy to reduce accidents by addressing human behavior.
The research investigates the preparation and implementation of each strategy for every deliverable using objective and reliable methods. These strategies can be scientifically studied and applied in other organizations, as the programs have indicators applicable at the organizational level and their methods are practical and useful in different stages of implementation.
The research contributes not only to the production of research that enriches the concepts of the new occupational safety and health proposal in Latin America but also has a significant impact on manufacturing companies that wish to reduce occupational accidents related to the human factor. The benefits of this research include reduced operating and administrative costs, improved work climate, increased motivation, and a positive impact on worker productivity and self-esteem. Hence, it is possible to create a culture of interdependence where workers take care of themselves and others out of conviction rather than obligation, which has been a significant challenge for occupational health and safety over the years.
Certain limitations were encountered when conducting the study research, like the lack of studies on occupational safety and health in Latin America. Additionally, the available literature on occupational safety and health-related program interventions was limited. The IPLEFOR program is suitable only for companies where the human factor is the primary cause of accidents. Furthermore, there were no studies available on motivation and occupational health and safety. Finally, obtaining information in Spanish on proposals for implementing human factors in occupational safety and health proved to be a challenge.
The main objective of the research was to determine whether implementing a motivation program could lead to a reduction in the rate of occupational accidents in the bakery plant of the manufacturing company under study.
On the other hand, the general hypothesis was that the implementation of a motivation program would have a significant impact on reducing occupational accidents.
Motivation
Motivation is a multi-faceted concept. One of the most common definitions is that it is the result of the interaction between people and their environment. For an organization to achieve success, all of its members need to be committed and put in a certain level of effort. Managers and administrators have different theories on what motivates people, and these theories affect how they lead their teams. In essence, motivation is what drives people to act according to their needs. It is the will to take action and optimize life activities, giving a sense of purpose to human existence. Maslow (1987) believed that motivation is the key to fulfilling the needs of an organism; therefore, it is an instrument that guides satisfying needs by prompting action. Atkinson (1958) defined it as the predisposition to act and produce one or more effects. Young (1961) saw motivation as a systematic process that leads to sustained action or behavior.
Job satisfaction is certainly related to salary satisfaction but also to employee motivation, which has a complex dynamic. The work environment, working conditions, treatment from superiors, recognition, quality of life at work, and respect for the work of each person are some of the relevant factors that contribute to job satisfaction and motivate an individual to give their best during the execution of an activity (Robbins, 2004).
In conclusion, motivation is the energy, process, and momentum that drives people to perform activities to achieve a purpose. In the case of occupational health and safety, this purpose will be oriented toward reducing accidents.
Herzberg’s Two-Factor Theory
One of the most suitable motivation theories for the research was Herzberg’s two-factor theory. According to psychologist Frederick Herzberg, people’s relationship with their work is essential, and their success or failure may depend on their attitude towards it. Herzberg sustains that there is a difference between people who say they feel good versus those who say they feel bad, thus some traits are usually associated with job satisfaction, while others are linked to dissatisfaction. People tend to relate job satisfaction to intrinsic factors like recognition, achievement, progress, and growth. On the other hand, job dissatisfaction is often related to extrinsic factors like organizational management, policies, supervision, working conditions, and interpersonal relationships.
It is important to note that the opposite of satisfaction is not dissatisfaction, as is commonly thought. The absence of negative aspects in a situation or place makes it satisfactory. Frederick Herzberg found that there are two separate concepts: the opposite of satisfaction is “no satisfaction”, and the opposite of dissatisfaction is “no dissatisfaction”.
According to Herzberg, the factors that lead to satisfaction are different from those that lead to dissatisfaction. Therefore, organizations that focus on eliminating the elements that cause dissatisfaction can create a peaceful work environment, but not necessarily a motivated one.
Herzberg referred to characteristics such as management, supervision, administration, working conditions, interpersonal relations, and pay as hygiene factors.
If the hygiene factors are adequate for the staff members, they will not be dissatisfied. However, this does not necessarily mean that they will be satisfied. To motivate people at work, Herzberg suggests focusing on achievement, recognition, responsibility, growth, and the nature of the work itself. These factors provide people with intrinsic satisfaction.
Herzberg also notes that the motivators for good job performance are different from those for poor performance. For the former, the job itself is the determining factor, while for the latter, the context of the job plays a greater role. Therefore, job dissatisfaction is typically associated with the job itself, while job satisfaction is influenced by the individual and the work environment.
The two-factor theory, also known as the motivation-hygiene theory, has had a significant impact on management thinking. According to this theory, every job has two critical sets of factors: dissatisfiers and satisfiers.
According to Herzberg, dissatisfiers are the factors that are related to hygiene, maintenance, or work conditions. Although they don’t motivate employees, they must be present to prevent dissatisfaction. These factors include working conditions, job security, company policy and administration, hierarchical status or position, technical survival, interpersonal relations with the direct supervisor or leader, interpersonal relations with the work team, interpersonal relations with subordination, personal life, and pay.
On the other hand, satisfiers, also known as motivators, directly influence job satisfaction or dissatisfaction. They are related to job analysis, progress, and development. Each of the six motivational factors identified by Herzberg can be fitted into Maslow’s hierarchy of needs. These factors include work itself, responsibility, success, recognition, promotion, and the possibility of growth. The presence of these factors can lead to employee engagement and job satisfaction or no satisfaction.
According to Herzberg, satisfaction and dissatisfaction are not two opposite poles of the same dimension, but rather two individual dimensions (López & Romero, 2015).
Definition of Occupational Accident According to Peruvian Law No. 9783
The regulation established by Law No. 29783 issued by the MTPE states that an occupation accident is
[any sudden event that causes an organic injury, functional disturbance, disability, or death. It also includes any incident that occurs during the execution of the employer’s orders or the execution of work under their authority, even outside the place and hours of work]. (Ley N.º 29783, 2011, p. 28)Todo suceso repentino que sobrevenga por causa o con ocasión del trabajo y que produzca en el trabajador una lesión orgánica, una perturbación funcional, una invalidez o la muerte. Es también accidente de trabajo aquel que se produce durante la ejecución de órdenes del empleador, o durante la ejecución de una labor bajo su autoridad, y aun fuera del lugar y horas de trabajo
Frequency Rate
According to the Instituto Nacional de Seguridad e Higiene en el Trabajo - INSHT [National Institute of Occupational Safety and Hygiene], the frequency rate is a measure of the number of lost time accidents that occur per million working hours of employees exposed to risk. This rate indicates the number of days lost per million working hours. Moreover, it takes into account temporary medical breaks and other time lost due to the incapacity caused by the occupational accident. Severity Rate
As for the severity rate, it represents the number of days lost per million working hours (INSHT, 1982).
To quantify the safety objective, the following rates are measured:
(500 workers)
Frequency rate = No. of accidents × 1,000,000 hours / hours worked
Severity rate = Days lost × 1,000,000 hours / hours worked
METHODOLOGY
Multi-Method Approach
The research study followed a multi-method approach. It involved collecting statistical data on occupational accidents, occupational safety, and health indicators, monitoring interactions, and conducting a motivation questionnaire to evaluate the status before and after the implementation of the program.
Descriptive Analysis
As part of the study of a company, descriptive and inferential analyses were conducted. The descriptive analysis involved organizing the data obtained from various techniques. The safety indicators were used to tabulate the data, and the level of motivation was evaluated using the Likert scale. This information was presented using tables and figures and analyzed using appropriate tools to better understand the variables under study. This allowed for an accurate diagnosis of the situation before and after the implementation of the program.
Inferential Analysis
The inferential analysis provided details on the current context, forecasts, evaluations, comparisons, and conclusions of the selected sample. This sample represents the population defined at a given time through the implementation of the IPLEFOR motivation program.
Questionnaire
To determine the level of motivation before and after the implementation of the IPLEFOR program, a questionnaire consisting of 20 questions was created based on Herzberg’s two-factor theory. The Likert scale was used to measure each question, and the questionnaire was applied to the personnel according to their availability with their consent. This provided the necessary information for the research conducted (Rivas, 2020).
Study Design and Participants
The study followed an action research approach, which views research as a collaborative process between the researcher and the object of study. It was an experimental study with a pretest/posttest design involving a single group. The study was conducted in the bakery plant of CNCH, a manufacturing company that produces panettones and cookies. The study population was comprised of 117 workers. A statistical collection was carried out as a baseline before the IPLEFOR motivational program was implemented.
Intervention Process
The IPLEFOR program stands for Identification of Critical Processes, Participative Leadership, Empowerment of Facilitators, Achievement Orientation, and Recognition. It aims to reduce workplace accidents at CNCH over 84 weeks (21 months), starting in March 2018 and ending in December 2019. It is based on Herzberg’s two-factor motivation-hygiene theory and consists of three stages:
Baseline stage: collecting data on accidents in the baking area in 2017
Direct intervention stage: implementing of motivators and hygiene factors.
Follow-up stage: monitoring without direct intervention.
The proposal consists of five strategies that aim to increase the motivation of workers about occupational health and safety in the organization under study, to reduce occupational accidents. It is based on Herzberg’s two-factor theory, which comprises hygiene factors and motivational factors.
Hygiene Factors
Strategy: Improving Critical Processes
Activity 01: Formation of the Unity Team
Unity is the work team in charge of process improvement. Members received prior training on program objectives. They were also informed about responsibilities to be met. This ensured participation of all members.
Activity 02: Identification of Critical Processes
The next step was to identify the critical steps in the bakery processes using the Hazard Identification, Risk Assessment and Risk Control (HIRARC) matrix. This helped identify the processes with the highest levels of risk of unsafe conditions. The members of the Unity also observed the tasks throughout the three shifts to ensure a comprehensive evaluation.
Activity 03: Improvement Assessment
The critical processes were examined for improvement options in Activity 03. Unity then selected the most feasible and sustainable engineering option, taking into account safety, quality, environmental, and process optimization factors.
Activity 04: Improvement Implementation
The chosen option was implemented within the established timeframes and deadlines in coordination with Unity leaders.
Table 1 provides a detailed list of activities, objectives, and deliverables for the improvement strategy of the critical processes.
Table 1 Improving Critical Processes.
Activity | Objective | Deliverable |
---|---|---|
Formation of the Unity Team | Determine leaders’ level of involvement | List of Unity members |
Identification of Critical Processes | Focus on the most critical risks | Critical processes identified |
Improvement Assessment | Choose an alternative with greater impact and efficiency | Minutes of Agreement Implementation plan of the chosen alternative |
Improvement Implementation | Improve working conditions Reduce occupational hazards (shocks, cuts) | Minutes of delivery of improvement HIRARC matrix of the activity with tolerable risk |
Source: Prepared by the author.
Strategy: Adopting a Participatory Leadership Style
Activity 01: Holding Meetings with Process Leaders
Team leaders must recognize the importance of the level of participation of personnel in occupational health and safety management. To this end, the objectives of the program and the commitment and acceptance of the leaders and those involved in the implementation process were explained in various meetings.
Activity 02: Designing Integration Policies
To encourage all employees to actively participate in occupational health and safety management, a policy was designed for them to join follow-up meetings with senior management and other areas involved.
Activity 03: Implementing Integration Policies
The integration policy was divulged in talks and a schedule was created for all employees to participate gradually according to their work shifts.
Table 2 details the activities, objectives, and deliverables of the strategy to adopt a participative leadership style.
Table 2 Adopting a Participatory Leadership Style.
Activity | Objective | Deliverable |
---|---|---|
Holding Meetings with Process Leaders | Raise awareness among leaders of the importance of involving plant staff Promote the participation of leaders | Minutes of Agreement |
Designing Integration Policies | Policy diffusion | Written and printed policies |
Implementing Integration Policies | Promote the participation of employees in decision-making | Attendance minutes including employees |
Source: Prepared by the author.
Motivators
Strategy: Implementing and Empowering Security Facilitators
Activity 01: Preparing a Personnel Selection Plan
A selection plan was developed to screen and select safety facilitators for the bakery plant based on specific criteria and functions.
Activity 02: Identifying Key Personnel
A list of all the individuals who passed the screening process was prepared, and volunteers were invited to join the program after receiving training.
Activity 03: Training Security Facilitators
The selected security facilitators completed a training program to learn their functions and include them in the team as security leaders.
Activity 04: Empowering Security Facilitators
The security facilitators were publicly announced at a ceremony held during all three shifts. They were also awarded a certificate of achievement, empowering them to perform their duties.
Activity 05: Assigning Responsibilities
Facilitators, i.e., safety leaders, representing the workers were trained on safety topics of the awareness plan included in the OHS program and tasked with conducting safety talks. They were also responsible for ensuring all workers participated in these talks by assigning topics to each individual.
Table 3 details the activities, objectives, and deliverables of the strategy to implement and empower safety facilitators.
Table 3 Implementing and Empowering Security Facilitators.
Activity | Objective | Deliverable |
---|---|---|
Preparing a Personnel Selection Plan | Establish criteria for selecting suitable personnel | Plan drafted |
Identifying Key Personnel | Select suitable personnel | List of eligible people |
Training Security Facilitators | Provide facilitators with the necessary knowledge and skills that will enable them to perform their functions | Trained personnel Closing minutes Record |
Empowering Security Facilitators | Generate satisfaction among the personnel for their important job Transform leadership structures | Awards ceremony |
Assigning Responsibilities | Personnel involvement Promote participation in leadership talks | Fulfillment of talks plan |
Source: Prepared by the author.
Strategy: Developing a Culture Based on Achievement Orientation
As part of the strategy to develop a culture that fosters achievement orientation, the first step is to establish a goal of “zero accidents”. This goal is then communicated to the workers and compared against the results of other plants to motivate them to demonstrate their capabilities and achieve the objective. The aim is for the workers to make this goal a personal objective by increasing their competitiveness and striving to meet their objectives.
Activity 01: Implementing a Competitiveness Program
To create competitiveness among small work teams (SWTs) and maintain “zero accidents”, a program was implemented.
Activity 02: Monthly Reports on the Number of Accidents
The communications area announced these results using billboards, wall newspapers, talks, and televisions in the canteen.
Table 4 details the activities, objectives, and deliverables of the strategy to develop a culture based on achievement orientation.
Table 4 Developing a Cultured Based on Achievement Orientation.
Activity | Objective | Deliverable |
---|---|---|
Implementing a Competitiveness Program | Promote competitiveness among SWTs | Leaderboard per SWT |
Monthly Reports on the Number of Accidents | Raise personnel awareness of the achievement of objectives | Statistics per SWT |
Source: Prepared by the author.
Strategy: Acknowledging Teams for Achieving Positive Occupational Health and Safety Results
Activity 01: Acknowledging Achievement of Objectives
Work teams were acknowledged each month they achieved “zero accidents”. At the end of the year, an awards ceremony was held for all personnel of the bakery plant for achieving 365 days without accidents. They received company products and a certificate, and a human chain was formed at the end to celebrate them for their achievement.
Activity 02: Forming Alliances Around Innovative Safety Ideas
As part of the company’s IMAGIX program, alliances were formed to acknowledge the best OHS ideas presented by workers. Incentives, such as food vouchers were given, allocating amounts according to the number of ideas generated.
Activity 03: Birthday Greetings and Congratulations
Workers were acknowledged and shown that they are important to the company and their colleagues, not only at a work level but also at a personal level (López & Romero, 2015).
Table 5 details the activities, objectives, and deliverables of the acknowledgment strategy for teams with positive results in OHS.
Table 5 Acknowledging Teams for Achieving Positive Occupational Health and Safety Results.
Activity | Objective | Deliverable |
---|---|---|
Acknowledging Achievement of Objectives | Generate satisfaction among the personnel for achieving the set objective | Ceremony with awarding of certificates |
Forming Alliances Around Innovative Safety Ideas | Raise awareness among staff in the achievement of objectives | OHS ideas generated and registered as innovative success |
Birthday Greetings and Congratulations | Show employees they are important | Announcement |
Source: Prepared by the author.
Table 6 shows the work Schedule for each strategy in the identified stages.
Table 6 Implementation of the Motivation Program.
Stage | Strategy | Activity | Description | Requirement | Duration | Responsible Person/Area |
---|---|---|---|---|---|---|
1 | Baseline Study Motivation-Accidents | Application of Motivation Questionnaire | The statistical summary of accidents was analyzed and a questionnaire was used to gather information. | Bond paper sheets Pens | 1 week | OHS Eng. |
2. Implementation of Hygiene Factors | Improvement of Critical Processes | Formation of Unity Team | The participation of key personnel such as the production coordinator, maintenance coordinator, plant personnel, and OHS team was established | Meeting room Laptop Multimedia projector | 8 weeks | OHS Eng. |
Identification of Critical Processes | After evaluating the critical processes in the IPERC, the process of transferring major inputs in the panettone line was chosen. | Plastic board | Unity | |||
Improvement Assessment | The engineering and maintenance team, along with the purchasing area, presented alternatives for the reconditioning of the structure, and the guidance line was selected as the best option. | Meeting room Laptop Multimedia projector Quotations | Unity | |||
Improvement Implementation | The implementation of the guidance line for the transfer of materials was completed. | Service Purchase Order | Engineering and Maintenance | |||
2. Implementation of Motivators | Adopting a Participative Leadership Style | Holding Meetings with Process Leaders | The meeting was attended by everyone, from the plant manager to the workers. | Meeting room Laptop Multimedia projector | 76 weeks | Unity |
Designing Integration Policies | Weekly meetings were conducted to review plant issues and a member of the plant personnel attended each meeting to follow up on safety improvements and/or observations. | Unity | ||||
Implementing Integration Policies | The safety policy was established as one of the pillars of the organization. | Minutes | Unity | |||
Implementing and Empowering Safety Facilitators | Preparing a Personnel Selection Plan | A list of plant personnel was obtained from the production coordinator. After evaluating the criteria and functions, the hierarchy of the team leaders was established. | Meeting room Laptop Multimedia projector | 8 weeks | OHS Team | |
Identifying Key Personnel | A screened list of eight (8) people who could perform the role of facilitator was obtained, and four (4) of them signed up as volunteers. | Payroll lists | OHS Eng. | |||
Training Safety Facilitators | A detailed program focused on basic safety knowledge and soft skill reinforcement was prepared. | Didactic material Bond paper sheets Printer Pens Construction paper | OHS Eng. | |||
Empowering Safety Facilitators | The facilitators’ formal presentation ceremony was held physically as scheduled (publication on panels and bulletin boards). | Training room Certificates | OHS Team | |||
Assigning Responsibilities | The entire bakery team, from management to plant workers, participated in the program. | Scheduling lists Didactic material | 76 weeks | OHS Eng. | ||
Developing a Culture Based on Achievement Orientation | Implementing a Competitiveness Program | The Invictus program was carried out, associating soccer with “zero accidents”. Safety talks disseminated accident statistics. | Banner Advertising material | 76 weeks | OHS Eng | |
Monthly Reports on the Number of Accidents | A 2 m by 1 m banner was made and placed in the most visible part of the company. | Banner Advertising material | OHS Eng. | |||
Acknowledging Teams for Achieving Positive Occupational Health and Safety Results | Acknowledging Achievement of Objectives | A awards ceremony was held, and certificates signed by the general manager and plant manager were handed out; a warm congratulatory gesture was made at the end. | Training room Certificates Snacks Delivery basket | 76 weeks | OHS Eng. | |
Forming Alliances Around Innovative Safety Ideas | The bakery team developed 123 innovative ideas. | Food vouchers | Head of Communications | |||
Birthday Greetings and Congratulations | Employee birthdays are now displayed on TV screens in the canteen. | Digital transmission | Head of Communications | |||
Follow-up | Assessing Performance After Direct Implementation of IPLEFOR Program | Monitoring of Indicators Assessment of Tasks OHS Results per SWT | In this phase of implementation, the OHS engineer no longer intervenes directly, but instead, the plant coordinator works with the facilitators. According to Bradle’s curve, the company is in the independent phase, and the goal of achieving “zero accidents” is possible with the mindset of “zero accidents by choice” and “safety is my responsibility”. | Notebook | 36 weeks | Production Coordinator and assistants Facilitators |
Measuring After Implementation Motivation-Accidents | Application of Motivation Questionnaire | The statistical summary of accidents was analyzed and a questionnaire was used to gather information. | Bond paper sheets Pens | 1 week | OHS Eng. |
Source: Prepared by the author.
Hypothesis Testing
The Wilcoxon signed-rank test for related samples (related, matched, or paired data) was used for hypothesis testing, which is used for independent samples. For this statistical test, the conditions that must be fulfilled are the same except for the autonomy of the samples, so dependence between both is required. In this test, there are two moments, the first before implementation, and the second after implementation. The first stage serves as a control or baseline to identify the changes that occur after the implementation of an experimental variable.
RESULTS
The chart presented in Figure 5 displays the various stages from the baseline study to the end of the program implementation. The chart shows that during the first 15 months (Stage 1), 13 accidents occurred in the bakery plant which was the starting point of the study. In the following 12 months (Stage 2), the motivation program was implemented and directly intervened, resulting in a reduction of accidents to seven (7). This is a 46% reduction in accidents. Finally, in the last 9 months (Stage 3) of follow-up without direct intervention, the chart shows that the occurrence of accidents was reduced to zero (0).
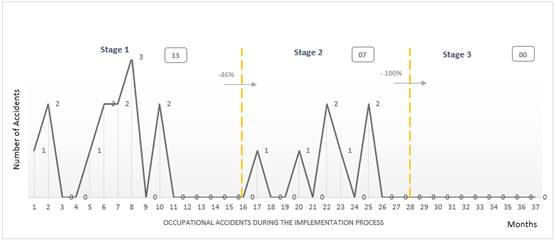
Source: Prepared by the author.
Figure 5 Results of the Implementation of the IPLEFOR Motivation Program.
The safety indicators of the entire company, including all production lines and plants at the Lima headquarters, have significantly improved after the implementation of the motivation program. As shown in Figure 6, the severity rate has reduced by 62%, dropping to 41.26. Similarly, the frequency index has decreased by 73%, dropping to 1.55 by the end of 2019.
As shown in Figure 7, the implementation of the program has resulted in a substantial improvement in the level of acknowledgment and achievement orientation. Before implementation, the level was at 16%, but by the end of implementation and follow-up, it increased to 75%, which represents an increase of 59%. Moreover, the data also indicates that the higher the level of acknowledgment and achievement orientation (upward trend), the lower the number of accidents (downward trend).
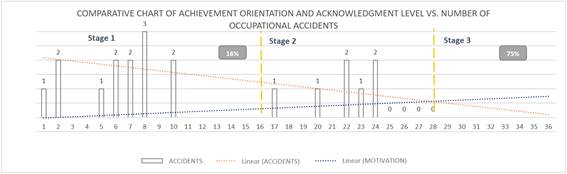
Source: Prepared by the author.
Figure 7 Results of Level of Acknowledgment and Achievement Orientation.
In Figure 8, the increase in each dimension evaluated after the implementation of the IPLEFOR motivation program is shown in greater detail. The level of achievement orientation increased by 47%, while acknowledgment increased by 69%.
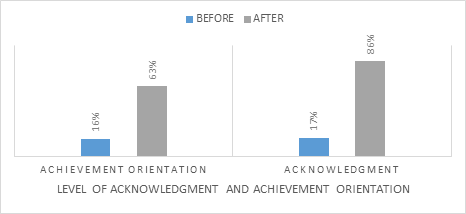
Source: Prepared by the author.
Figure 8 Results of Level of Acknowledgment and Achievement Orientation Before and After Implementation.
The results of all factors are presented in Tables 7 and 8. The motivation program is based on the dimensions that have had the greatest impact after implementation, namely, achievement orientation, acknowledgment, and physical conditions of the work environment. Other factors, such as personal growth and development, experienced a 20% increase in satisfaction, administration and company policy experienced a 3% increase, and interpersonal relations experienced a 12% increase. In other words, all factors experienced an increase, with the first three having the greatest impact.
Table 7 Results Before the Application of the Questionnaire by Dimensions.
Before Implementation | |||||
---|---|---|---|---|---|
Strongly Disagree | Disagree | Indifferent | Agree | Strongly Agree | |
Achievement Orientation | 3% | 10% | 71% | 13% | 3% |
Personal Growth and Development | 5% | 20% | 63% | 10% | 3% |
Acknowledgment | 22% | 56% | 5% | 14% | 3% |
Company Management and Policies | 4% | 27% | 21% | 39% | 9% |
Interpersonal Relations | 11% | 45% | 17% | 22% | 6% |
Physical Conditions of the Work Environment | 2% | 8% | 38% | 45% | 7% |
Source: Prepared by the author.
Table 8 Results After the Application of the Questionnaire by Dimensions.
After Implementation | |||||
---|---|---|---|---|---|
Strongly Disagree | Disagree | Indifferent | Agree | Strongly Agree | |
Achievement Orientation | 2% | 8% | 27% | 59% | 4% |
Personal Growth and Development | 4% | 12% | 50% | 27% | 6% |
Acknowledgment | 5% | 7% | 2% | 74% | 12% |
Company Management and Policies | 4% | 25% | 20% | 42% | 9% |
Interpersonal Relations | 6% | 38% | 16% | 34% | 6% |
Physical Conditions of the Work Environment | 1% | 3% | 37% | 49% | 10% |
Source: Prepared by the author.
Hypothesis Testing
In order to determine whether the data follows a normal distribution or not, the Kolmogorov-Smirnov normality analysis was used. As per the results presented in Table 9, the significance level is less than 0.05, which indicates that the data is not normally distributed. Therefore, the Wilcoxon nonparametric test for related samples was used to diagnose the implementation of the program.
The hypotheses for the study are as follows:
H0: The implementation of a motivation program has no significant impact on reducing accidents.
Hi: The implementation of a motivation program has a significant impact on reducing accidents.
Table 10 summarizes the results of the hypothesis testing with the Wilcoxon signed-rank test. Since the significance level is less than 0.05, the null hypothesis is rejected. Additionally, Table 11 presents the summary of the Wilcoxon signed-rank test for related samples, where the asymptotic significance is less than 5%. Hence, the null hypothesis is rejected, and the alternative hypothesis is accepted, indicating that there is a significant change after the implementation of the motivational program.
Table 9 Normality Test.
Kolmogorov-Smirnov | |||
---|---|---|---|
Statistic | df | Sig. | |
Pretest | .139 | 117 | .000 |
Posttest | .127 | 117 | .000 |
Source: Prepared by the author.
Table 10 Hypothesis Testing Summary.
Null Hypothesis | Test | Sig. | Decision | |
---|---|---|---|---|
1 | The median difference between pretest and posttest is equal to 0 | Wilcoxon Signed-Rank Test for Related Samples | .000 | Reject null hypothesis |
Source: Prepared by the author.
Table 11 Wilcoxon Signed-Rank Test for Related Samples Summary.
Total N | 117 |
Test Statistic | 5591 |
Standard Error | 358.167 |
Standardized Test Statistic | 6.299 |
Asymptotic Sig. (2-sided test) | .000 |
Source: Prepared by the author.
Table 12 presents comparative statistics that demonstrate the effectiveness of the IPLEFOR program. The data shows that the program resulted in an 8-point increase in the implementation of safety protocols, which resulted in a significant reduction in accidents. The implementation of a motivational program has proven to be a successful strategy for achieving this reduction.
DISCUSSION
The implementation of the IPLEFOR program resulted in a 100% reduction in accidents in the bakery plant over 21 months. The third stage of the program was particularly crucial as it demonstrated the sustainability of the program that was implemented during the second stage. In the third stage, the workers themselves carried out the program, which indicates that they were in the independent stage of the Bradley curve in safety culture. This means that they were motivated to take care of themselves as a personal goal, rather than being afraid of sanctions or following rules imposed by the company.
It is worth noting that the program focused on improving occupational health and safety, particularly at the plant with the highest accident rates. After implementation, the program delivered satisfactory results. A key aspect of this program was its focus on influencing the human factor, which is crucial for accident reduction management. This reinforces the idea that human behavior interventions are an effective accident-reduction strategy. It is important to mention that the baseline study showed that the company complied with basic occupational health and safety conditions. However, despite covering these basic needs, there was still no reduction in accidents. As a result, the IPLEFOR motivation program was implemented.
Based on the results of the motivation questionnaire, it is evident that the program was more focused on achievement orientation and recognition rather than hygiene dimensions, which did not experience much variation.
Moreover, upon comparing results, it is evident that investing in motivational factors yields better results than investing in hygienic factors.
Finally, the study also confirmed the hypothesis that implementing a motivation program reduces work accidents in the manufacturing company. Therefore, this new methodology can be a valuable scientific contribution and aid in the effective management of organizations to reduce accidents.
CONCLUSIONS
The main aim of this research was to determine whether implementing a motivation program would lead to a reduction in work accidents at CNCH’s bakery plant. By using quantitative analysis and monitoring interactions, as well as collecting statistical data, it was concluded that the motivation program was effective in reducing accidents. The results showed that the IPLEFOR program reduced the number of accidents by 100% in a period of 21 months, thus achieving its objective.
Moreover, the bakery plant witnessed a notable improvement in compliance with occupational health and safety objectives, as evidenced by a 62% drop in the severity rate and a 73% drop in the frequency index. These results suggest that the reduction of accident rates in the bakery plant has a significant impact on the indicators of the entire company. Therefore, it can be concluded that a motivation program can positively influence compliance with OHS objectives at the corporate level.
The results of the achievement orientation and acknowledgment dimensions indicate that an increase in the level of achievement orientation and acknowledgment can significantly reduce accidents. This is evidenced by a 47% increase in achievement orientation, a 69% increase in acknowledgment, and a 100% reduction in accidents.
Although reducing accidents remains a challenge, it is evident that influencing human behavior yields satisfactory results. The motivation questionnaire showed a 26% increase in satisfaction levels, indicating that motivating personnel from a safety and occupational health perspective has the potential to reduce the number of accidents.
The program consisted of three stages, with the final one being crucial since it demonstrated that the program was sustainable without direct intervention from the OHS team. Consequently, the bakery plant was able to establish an independent occupational health and safety culture, where safety is a matter of conviction rather than obligation.
ACKNOWLEDGMENT
To the company under study for their commitment to safety by providing the necessary resources with no expense spared and prioritizing safety above all else.
REFERENCES
Atkinson, J. (1958). Towards experimental analysis of human motivation in terms of motives, expectancies and incentives. En J. Atkinson (Ed.), Motives in fantasy, action and society. Princeton, NJ, EE. UU.: Van Nostrand. [ Links ]
Denton, K. (1986). Seguridad industrial. Ciudad de México, México: McGraw-Hill. [ Links ]
González, A., Bonilla, J., Quintero, M., Reyes, C., y Chavarro, A. (2016). Análisis de las causas y consecuencias de los accidentes laborales ocurridos en dos proyectos de construcción. Revista Ingeniería de Construcción, 31(1). [ Links ]
Heinrich, H. W., Petersen, D., y Roos, N. R. (1980). Industrial Accident Prevention (5th edition). Nueva York, NY, EE. UU.: Mc-Graw Hill. [ Links ]
ILOSTAT. (s.f.). Statistics on safety and health at work. https://ilostat.ilo.org/topics/safety-and-health-at-work/ [ Links ]
Instituto Nacional de Seguridad e Higiene en el Trabajo. (1982). Estadísticas de accidentabilidad en la empresa. Caso Práctico (NTP 2). [ Links ]
Islas, M. E., y Meliá, J. L. (1991). Accidentes de trabajo. Intervención y propuestas teóricas. Revista Lationamericana de Psicología, 23(3), 323-348. [ Links ]
Ley N.° 29783. (2011, sábado 26 de agosto). Ley de seguridad y salud en el trabajo. Diario oficial El Peruano. [ Links ]
López Beltrán, J. G., y Romero Cribilleros, E. N. (2015). Programa de motivación basado en la teoría de dos factores para mejorar el desempeño laboral en la Caja Municipal Sullana - Sede Trujillo. (Tesis de grado). Universidad Nacional de Trujillo, Trujillo. [ Links ]
Maslow, A. H. (1987). Motivation and Personality. New York, NY, EE. UU.: Addison-Wesley Longman. [ Links ]
Ministerio de Trabajo y Promoción del Empleo. (2020). Notificaciones de accidentes de trabajo, incidentes peligrosos y enfermedades ocupacionales. https://www.gob.pe/institucion/mtpe/informes-publicaciones/454630-boletin-estadistico-mensual-edicion-enero-2020 [ Links ]
Rivas Cruzado, R. K. (2020). Programa de motivación para mejorar el desempeño laboral en la empresa créditos y cobranzas s.a.c, Chiclayo 2018. (Tesis de grado). Universidad Señor de Sipán, Pimentel. https://repositorio.uss.edu.pe/bitstream/handle/20.500.12802/7398/Rivas%20Cruzado%2c%20Ruleysbi%20Katheryne.pdf?sequence=1&isAllowed=y [ Links ]
Robbins, S. P. (2004). Comportamiento organizacional. México D.F., México: Pearson Educación. [ Links ]
Salinas, M. (2018). Accidentes de trabajo. Consecuencias jurídicas. https://www.cerem.pe/blog/accidentes-de-trabajo-consecuencias-juridicas [ Links ]
Young, P. T. (1961). Motivation and emotion. New York, NY, EE. UU.: Wiley. [ Links ]
Received: February 14, 2023; Accepted: April 17, 2023; pub: December 20, 2023