INTRODUCCIÓN
En el país, la mayoría de las empresas u organizaciones aplican diversas teorías, técnicas y herramientas de mejora con la finalidad de aumentar su productividad; en muchos casos, se trata de imitar experiencias de mejoras que fueron aplicadas en otras empresas que dieron como resultado un incremento significativo de la productividad y, en consecuencia, una ventaja competitiva en relación a sus competidores. Es fundamental ejecutar de manera correcta un conjunto de herramientas de mejora continua que propicie un verdadero cambio dentro de la organización para mejorar la productividad, reducir costos y obtener un mayor margen de ganancias sostenible en el tiempo.
Las pymes, que representan la mayor parte de las empresas en el país, no cuentan con líneas de producción totalmente automatizadas, por lo que necesitan equilibrar correctamente cada estación de trabajo para así lograr aprovechar al máximo sus recursos. Por lo general, el montaje de maquinarias y la distribución de la línea de producción se realizan de manera empírica, sin aplicar técnicas o herramientas de mejora que ayuden a aprovechar los recursos disponibles en favor del incremento de la productividad. Para estos casos se debería buscar un conjunto de herramientas de mejora continua que se ajuste a las necesidades económicas, de espacio y demanda de cada organización.
El presente estudio se desarrolló en una empresa dedicada al procesamiento de vidrio templado utilizado en el rubro arquitectónico como parte de los acabados de la construcción. La mayoría de las máquinas utilizadas para el procesamiento de vidrio templado son de procedencia italiana y, a menudo, son adquiridas de diferentes proveedores, por motivos económicos o porque el proveedor no ofrece maquinaria para armar toda la línea de procesamiento. Esto hace que existan distintas capacidades de producción en las áreas de trabajo al momento del montaje de la línea de producción.
El propósito de este artículo es implementar un modelo de balance de línea que comprenderá el uso de herramientas de mejora continua y delean manufacturingpara toda la línea de producción (áreas de corte, pulido, entalle y horno), debido a que la empresa presenta problemas de baja productividad y desaprovechamiento de horas hombre, al no tener las áreas de trabajo correctamente balanceadas en sus capacidades de producción. A diferencia de otros trabajos de investigación y tesis en donde se desarrolla el uso del balance de línea como una herramienta de mejora para el incremento de la productividad basado en la elaboración de estrategias para equilibrar las capacidades de procesamiento de cada área de trabajo, aquí se empleará un “modelo de balance de línea” que consiste en una selección de herramientas de mejora continua ylean manufacturingque permitirá lograr un aumento de la productividad.
El modelo que se utilizará para balancear la línea de procesamiento de vidrio templado se basa en la ejecución de los 5 pasos de la teoría de restricciones (identificar, explotar, subordinar, elevar y repetir). Se utilizarán también herramientas delean manufacturing(detección y eliminación demudas) y de mejora continua (metodología 5S) al momento de ejecutar las acciones de mejora del paso 2 (explotar la restricción). Alcalde (2010) menciona que la metodología de las 5S se basa en el orden y la limpieza, pues esto permite crear una nueva cultura dentro de la organización. Al utilizar herramientas de mejora continua ya existentes en esta investigación, se podría decir que se está expandiendo su aplicación en el desarrollo de este modelo de balance de línea.
Para implementar el modelo de balance de línea, se tiene que realizar un análisis de los trabajos que se realizan en todas las áreas, esto incluye la revisión de los reportes de producción y los horarios de los turnos para obtener el tiempo que el operario utiliza para la producción en condiciones normales, a una velocidad y ritmo de trabajo que debería estar acorde con la demanda. Con esta información se puede obtener la capacidad de producción de cada área de trabajo en condiciones normales y así determinar cuál tiene la menor capacidad y sería la limitante dentro de la línea de producción.
Por todo lo expuesto, esta investigación tiene como objetivo principal definir si se encuentra una relación entre la implementación de este modelo de balance de línea y una mejora o incremento de la productividad en la empresa de procesamiento de vidrio templado que se está analizando. Será necesario el planteamiento de una hipótesis que posteriormente será contrastada con los resultados para verificar si existe una relación entre el modelo desarrollado y el incremento de la productividad. La hipótesis es la siguiente: “Mediante la aplicación de un modelo de balance de línea, se mejorará la productividad de una empresa de procesamiento de vidrio templado”.
Asimismo, se elaborará una estructura de costos al inicio y al final de la aplicación del modelo para analizar el impacto económico del precio de venta del producto terminado sobre la empresa y, finalmente, se calculará el ROI para determinar si la inversión realizada fue beneficiosa para la empresa.
Balance de línea
Para Salazar (2019), el balance de línea es un método de gran importancia para controlar la producción, debido a que, si se logra un correcto equilibrio de la línea de producción, se podrá optimizar otras variables que influyen en la productividad, por ejemplo: el inventario de piezas por procesar, el tiempo promedio de procesamiento y los despachos parciales de piezas terminadas.
Según los autores Suñé et al. (2004), al momento de diseñar la línea de producción, se deben distribuir las tareas de tal manera que los recursos sean aprovechados en todo el proceso. Lo más complicado de balancear la línea de producción es dividir el proceso en estaciones de trabajo donde se ejecutará un grupo de tareas, de manera que la carga de trabajo sea la más óptima dentro del tiempo de ciclo de la producción. A propósito de esto último, García et al. (2004) indican que el objetivo de balancear una línea de producción es que cada estación de trabajo produzca un mismo metraje y tenga un mismo tiempo de ciclo de producción, para así evitar las acumulaciones de carga por procesar.
Los pasos para iniciar el balance de línea para Suñé et al. (2004) son los siguientes:
Definir e identificar todas las tareas que conforman al proceso de producción.
Determinar el tiempo estándar que se necesitará para el desarrollo de cada tarea.
Establecer los recursos que se necesitarán.
Determinar el orden de ejecución.
Meyers (2000) sostiene que una vez implementado el balance de línea se pueden identificar los cuellos de botella. La variabilidad de la demanda y el poseer maquinaria con capacidades diferentes hace que se requieran diferentes tiempos de procesamiento, lo que genera cuellos de botella dinámicos.
Para obtener una línea de producción balanceada, se necesita de una correcta aplicación teórica, redistribución de recursos e incluso inversiones económicas.
Para Calampa (2014), al balancear la línea de producción se logra:
Reducir y estandarizar los costos.
Elaborar una estructura de bonificaciones por la productividad alcanzada.
Obtener la cantidad de producción esperada dentro del plazo establecido.
Mejorar la gestión de la producción.
Incrementar la productividad general y el estímulo del personal.
Determinar tiempos y movimientos para mejorar la distribución de la carga de trabajo.
Eliminar los inventarios de piezas en proceso y los cuellos de botella.
Mejorar el flujo del proceso entre las áreas de producción.
Comprometer a los trabajadores en la eliminación de los 7 desperdicios omudasdellean Manufacturing(sobreproducción, tiempos de espera, transporte, procesos, inventarios, movimientos y productos defectuosos).
Teoría de restricciones (TOC)
En el balance de línea encontramos el término “cuello de botella”. En la Teoría de restricciones (TOC, por sus siglas en inglés) de Goldratt (2004), se menciona el concepto de “cuello de botella” como la falta de capacidad de una estación de trabajo para satisfacer la demanda de una estación anterior, estableciendo de esta manera una “restricción”. Según Saidi et al. (2017), son estos “cuellos de botella” los que determinan las capacidades de producción. En consecuencia, es la estación de trabajo con la mínima capacidad entre todas la que está generando un impacto negativo en el tiempo de ciclo total. Para Kikolski (2016), esto marca el ritmo del proceso productivo.
Chase et al. (2009) indican que la teoría de restricciones representa un conjunto de herramientas de mejora continua, la cual se logra aplicando estos 5 pasos:
Identificar la restricción. Se considera un paso complicado, pues es necesario evaluar el proceso en su totalidad y así detectar aquella actividad que restringe el flujo del proceso. Esto no se refiere solo al proceso, sino también a toda la organización.
Explotar la restricción. Se requiere encontrar métodos que sean capaces de aumentar la capacidad de la actividad limitante, es decir aumentar elthroughput(rapidez del sistema para aumentar sus ganancias).
Subordinar todo a la restricción. Se hace que la limitante opere al 100% de su capacidad máxima, puesto que es la que marca el ritmo de trabajo.
Elevar la restricción. Se debe aumentar la capacidad de la restricción, aquí se puede considerar el uso de recursos económicos.
Verificar si existe una nueva restricción. Si la limitante inicial es eliminada, se procede a reiniciar los pasos anteriores con la siguiente limitante del proceso productivo.
Metodología de las 5S
Según Hernández (2016), el objetivo de las 5S es mejorar el orden de las áreas de trabajo y que esto se mantenga en el tiempo; de este modo, será posible perfeccionar las condiciones de trabajo, el clima organizacional y el desempeño laboral, lo que resultará en el aumento de la productividad y la mejora de la calidad de los productos.
La primera S,seiri(clasificación), según Bonilla et al. (2010), consiste en clasificar los objetos en útiles y no útiles para solamente conservar los que son de utilidad y retirar los que no lo son porque ocupan espacio.
La segunda S,seiton(ordenar), según Bonilla et al. (2010), consiste en organizar los elementos clasificados del paso anterior, de manera que se puedan ubicar con facilidad, lo que permite ahorrar tiempo y evitar movimientos innecesarios.
La tercera S,seiso(limpieza), consiste en identificar y eliminar las fuentes de suciedad; según lo mencionado por Rey (2005), se debe realizar el aseo de la zona de trabajo para mantenerla libre de suciedad e incentivar al trabajador a que lo realice de forma diaria al inicio y final de la jornada laboral.
La cuarta S,seiketsu(estandarización), parte de las 3 S anteriores y su finalidad es evitar el retraso en las etapas previas, cuya ejecución debe ser parte de la rutina diaria. Para Cuatrecasas y Torrel (2010), la estandarización trata de formar un hábito en los trabajadores para el cumplimiento de los pasos anteriores. Tener una buena organización y orden será esencial para lograr la estandarización.
La última S,shitsuke(disciplina), según Dorbessan (2010), es la parte más trascendente debido a que se encarga de buscar el cumplimiento de las 4 S anteriores. Impulsa la práctica de la disciplina con un espíritu proactivo, ya que los beneficios serán provechosos, tanto para la empresa como para los trabajadores. En la medida que los trabajadores sean disciplinados y comprometidos, la empresa logrará grandes resultados en cuanto a calidad y niveles de productividad.
Mudas: Desperdicios
Uno de los objetivos básicos dellean manufacturinges eliminar o disminuir los desperdicios omudasque resultan de diversas tareas y que no generan valor alguno. Socconini (2019) menciona que ellean manufacturingclasifica las variedades demudasen siete grupos:
- Sobreproducción: consiste en producir en exceso a lo programado.
- Espera: tiempo de retraso que se genera entre el operador y la máquina que está operando.
- Transporte de materiales y herramientas: desplazamiento inútil de personas o piezas en proceso que no genera valor.
- Procesos innecesarios: procesos que no incrementan el valor del producto final.
- Sobreinventario: materiales, piezas en proceso o productos terminados que se producen en abundancia y exceden la demanda del área comercial.
- Movimientos innecesarios del trabajador: movimientos de materiales o herramientas que se realizan dentro del proceso, que no generan valor y, por el contrario, incrementan los costos.
- Productos defectuosos: pérdida de recursos que se utilizaron al momento de producir un producto no conforme.
Productividad
Para García (2006), la productividad es el nivel de rendimiento con que se utilizan los recursos disponibles para lograr los objetivos; indica también que la productividad de una empresa se examina con el fin de determinar los problemas que la afectan y, posteriormente, establecer las estrategias para darles solución.
La OIT (1996) define la productividad como una relación entre las unidades producidas y el insumo utilizado, indica además que la productividad puede verse afectada por diferentes factores externos, así como por deficiencias en sus actividades internas.
METODOLOGÍA
La presente investigación es de tipo aplicada y de diseño experimental, dado que la variable independiente “modelo de balance de línea” se manipula de manera intencional, lo cual produce un efecto en la variable dependiente “productividad”.
Línea de procesamiento de vidrio templado
El estudio se realizó en la empresa Glasstempcorr, ubicada en el distrito de Ventanilla. La planta está sobre un terreno de aproximadamente 5000 m2y la línea de procesamiento está compuesta por las áreas de corte, canteo, entalle, lavadora y horno. En la actualidad, la productividad de la línea de procesamiento no se encuentra en un nivel adecuado debido al poco control de los trabajos entre las áreas, los reprocesos y desechos. Por esa razón, se recurre a la aplicación de un modelo de balance de línea basado en el desarrollo de los 5 pasos de la teoría de restricciones, como herramienta de mejora continua, para que al momento de aplicar las acciones de mejora se utilicen la detección y eliminación demudasde manera conjunta con la implementación de la metodología de las 5S en el área de trabajo en donde se detecte la restricción. Este modelado se puede apreciar de manera gráfica en la Figura 1.
Evaluación e implementación de la teoría de restricciones (TOC)
Se procede con la aplicación del paso 1. Como se cuenta con la data histórica de producción, se pueden obtener las capacidades de cada área y un promedio de metros cuadrados de vidrio templado procesado de los últimos 3 meses. Con esos datos es posible determinar el área que tiene la menor capacidad de procesamiento y por lo tanto genera la restricción. En la Figura 2, se concluye que la restricción de la línea recae en el área de entalle. En esta etapa inicial, se puede elaborar una estructura de costos para hallar el valor del costo unitario y así compararlo con el valor que se obtendría después de la implementación del modelo de balance de línea.
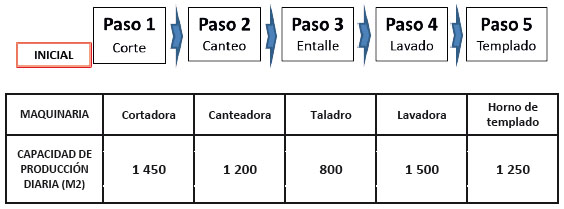
Fuente: Elaboraciónpropia
Figura 2 .Capacidades iniciales de producción en la línea de procesamiento.
Para el paso 2, se requiere explotar la restricción, por lo que se tienen que realizar acciones que ayuden a incrementar la capacidad de procesamiento del área de entalle solo con los recursos propios del área (operarios y maquinaria). Se aplican dos herramientas de mejora continua de forma paralela, las cuales forman parte del modelo propuesto; la primera fue la implementación de las 5S. Previo a dicha implementación, se realizó una línea base, se tomaron fotos de las condiciones anormales y se otorgó un puntaje a cada categoría (clasificación, orden, limpieza, estandarizar y mantener) para así poder determinar los puntos a corregir. El jefe de calidad, con el apoyo de los encargados del área, dirige la implementación, la cual constaba de tres fases: en la primera fase, se capacita y sensibiliza al personal involucrado; en la segunda fase, se implementa la metodología; y en la tercera fase, se realiza un seguimiento de todo lo realizado anteriormente.
La segunda herramienta es la detección y eliminación de lasmudasque existan dentro del proceso productivo, la cual es utilizada enlean manufacturing. Al analizar el proceso de entalle, se encuentranmudasrelacionadas con tiempos de espera ocasionadas por falta de información de los trabajos a realizar y por paradas debido a mantenimientos no programados; asimismo, se detecta un porcentaje considerable de productos defectuosos, lo cual genera desperdicio de materia prima y horas-hombre. Se tienen que desarrollar planes de acción para reducir estos desperdicios, tales como preparar con anticipación toda la información de los trabajos a realizar, mejorar el programa mensual de mantenimiento preventivo y capacitar al personal para disminuir los productos defectuosos por mala manipulación. Una vez ejecutadas las acciones de mejora, la línea de procesamiento quedaría balanceada, tal como se puede apreciar en la Figura 3.
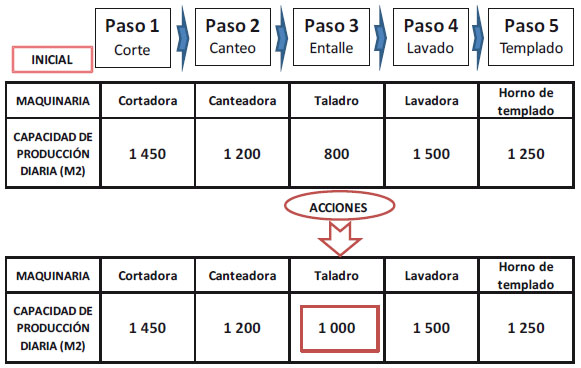
Fuente: Elaboración propia.
Figura 3 Valoresde capacidades de producción luego de la aplicación de acciones de mejora del paso 2.
El paso 3 consiste en subordinar todo lo demás a la actual capacidad de la restricción, lo que significa que el área de entalle es la que marca el ritmo de trabajo y, por consiguiente, se deben racionar los recursos que se emplean en las demás áreas de producción (operario y maquinaria) hasta lograr una capacidad que supere por poco a la de entalle para así lograr una capacidad de procesamiento homogénea en toda la línea. Es pertinente contar con el apoyo de la gerencia para llevar a cabo este paso, puesto que con frecuencia se debe convencer a los directivos sobre la necesidad de reducir el ritmo de trabajo en otras áreas que generan producción en exceso.
El paso 4 consiste en elevar la restricción, para lo cual se necesitará hacer una inversión económica que consiste en la adquisición de un taladro manual y la contratación de 2 operarios, con lo cual la capacidad del área de entalle incrementa a 1300 m2, como se puede apreciar en la Figura 4. En esta etapa se puede elaborar otra estructura de costo unitario para compararlo con el inicial.
El paso 5 consiste en verificar si el proceso limitante quedó eliminado. En nuestro caso se puede apreciar que ahora el área de entalle dejó de ser una restricción y el área de canteo pasó a serlo; por lo cual, se tendrían que ejecutar nuevamente los pasos anteriores hasta obtener una capacidad de procesamiento acorde a la demanda planteada por el área comercial.
RESULTADOS
La aplicación del modelo de balance de línea permite comparar la capacidad de producción antes y después de la implementación del modelo. En esta investigación, se realizará primero una contrastación de la hipótesis planteada, la cual consiste en determinar si se logró incrementar la productividad de la línea de procesamiento de vidrio templado. Para esto, se presenta la Tabla 1 con información de la producción extraída desde enero de 2019 hasta febrero del 2020, en donde se puede apreciar el índice de productividad de los meses en los que se aplicó el modelo de balance línea. En la información presentada del año 2019, se puede apreciar el índice de productividad antes de la aplicación del modelo de balance de línea. De enero a junio de 2020, se aprecia un incremento del índice de productividad debido a las primeras acciones de mejora realizadas con los propios recursos del área; es importante tener en cuenta que en marzo solo se trabajó hasta el día 16 y en abril no se registra la cantidad de producción puesto que la planta estuvo cerrada por la pandemia del COVID-19. Finalmente, entre julio de 2020 y febrero de 2021 se obtienen otros valores del índice de productividad después de la aplicación del paso 4 de la teoría de restricciones (TOC).
Prueba de hipótesis
Para comprobar la hipótesis planteada, primero se extrae información de la productividad de la Tabla 1 y se ejecuta en el programa Minitab 18 para así poder determinar si la data tiene o no distribución normal.
Del Minitab 18, se extraen las figuras 5 y 6 del comparativo de la productividad al inicio y después de la aplicación el modelo.
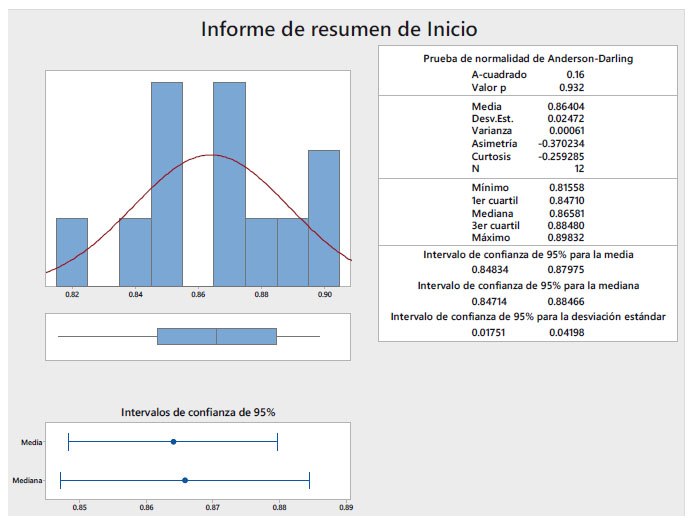
Fuente: Elaboración propia.
Figura 5. Gráfica de la distribución de la normalidad de los valores de la productividad al inicio de la aplicación.
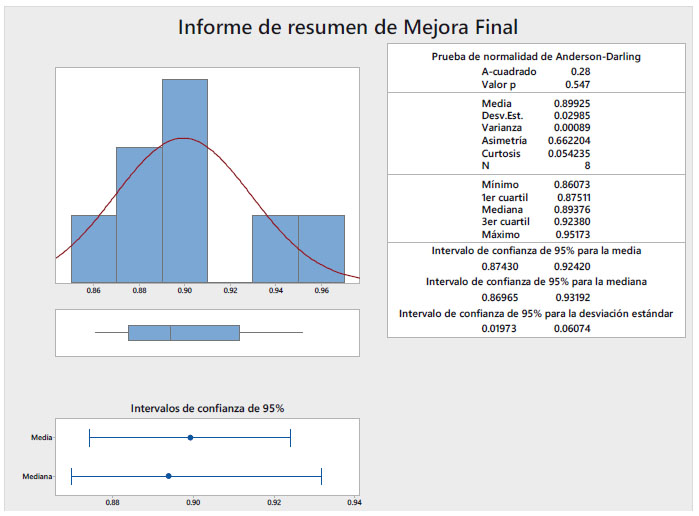
Fuente: Elaboración propia.
Figura 6. Gráfica de la distribución de la normalidad de los valores de la productividad después de la aplicación del modelo.
De la prueba de normalidad realizada, se determinó que la distribución es normal debido a que elp-valor es mayor que 0.05, la curva que se muestra tiene forma de campana y, si se traza una línea vertical, cruza la media y la mediana.
Una vez determinado que, para la información recolectada, la data tiene un comportamiento paramétrico, se procede a utilizar la prueba t de Student para 2 muestras para comprar la productividad al inicio y al final de la aplicación del modelo y demostrar la hipótesis.
Prueba T e IC para dos muestras: Inicio y Mejora final
Método
μ₁: media de Inicio
µ₂: media de Mejora final
Diferencia: μ₁ - µ₂
No se presupuso igualdad de varianzas para este análisis.
Estadísticas descriptivas
Estimación de la diferencia
Prueba
Hipótesis nula H0: μ₁ - µ₂ = 0
Hipótesis alterna H₁: μ₁ - µ₂ < 0
Se tiene en consideración que si se obtiene unp-valor ≥ 0.05, se aceptará como respuesta válida la H0. Pero si se obtiene unp-valor < 0.05, se aceptará como respuesta válida la Hay se rechaza la H0.
Dado que el valor depes menor que 0.05, se debe rechazar la hipótesis nula y aceptar la alterna, la cual indica que la diferencia µ1- µ2< 0, lo cual demuestra que el porcentaje de productividad aumentó a partir de julio del 2020. Con esta comparación se constata que la hipótesis es correcta a l afirmar que “Mediante la aplicación de un modelo de línea, se mejorará la productividad de una empresa de procesamiento de vidrio templado”.
Análisis económico
Se realizará un comparativo de los costos unitarios promedios al inicio y después de la aplicación de los 5 pasos del TOC para analizar los resultados obtenidos. En la Tabla 2, se puede apreciar una estructura de costos al inicio del estudio
Tabla 2. Estructura de costos inicial para el paso 1. Estructura de costos - Condiciones iniciales. Valores promedio para una demanda de 800 m2
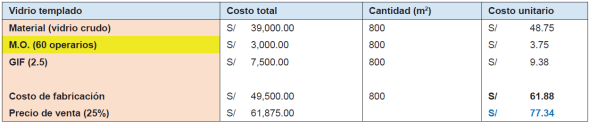
GIF = Gasto indirecto de fabricación que equivale a 2.5 veces el costo de la mano de obra (M.O.)
Fuente: Elaboración propia.
Del cuadro presentado, se deduce que el valor unitario de venta por m2es de S/ 77.34, que equivale a $ 21.48 ≈ $ 22.00, el precio actual del mercado por m2para un vidrio de 8 milímetros de espesor, esto calculado para una capacidad de procesamiento de línea de 800 m2. En la Tabla 3, se puede apreciar la estructura de costos resultante después de la aplicación del paso 4.
Tabla 3 Estructura de costos al final del paso 4. Estructura de costos - Condiciones finales. Valores promedio para una demanda de 1200 m2. Se adquirió un taladro manual y se contrató a dos operarios.
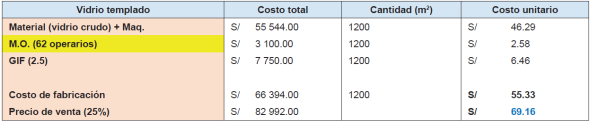
GIF = Gasto indirecto de fabricación que equivale a 2.5 veces el costo de la mano de obra (M.O.)
Fuente: Elaboración propia.
Del cuadro final, se observa que el valor unitario de venta por m2ha disminuido a S/ 69.16, que equivale a $ 19.21 ≈ $ 20.00, esto también está calculado para vidrios de 8 milímetros de espesor y para una capacidad final de procesamiento de la línea de 1200 m2. En esta tabla, se ha considerado el costo de la maquinaria adquirida (1 taladro) y su valor se ha distribuido para una vida útil de 5 años. El monto del precio de venta final está por debajo del precio del mercado, lo que permite a la empresa ofrecer al cliente un precio menor al del mercado sin afectar sus ganancias.
Se realiza un análisis sobre la rentabilidad de la inversión en el área de entalle para determinar qué tan lucrativa resultó para la empresa. De los valores obtenidos en las Tablas 1 y 2, se elabora la Tabla 4 para hallar el valor del retorno sobre la inversión (ROI) utilizando la fórmula mostrada abajo.
G = S/ 528,000.00 Ganancia
I = S/ 422,350.00 Inversión
Del resultado obtenido, se puede deducir que por cada sol que se ha invertido en este modelo de balanceo de línea se obtendrán S/ 0.20 de ganancia, lo cual hace rentable al proyecto.
DISCUSIÓN
Este modelo de balance de línea tiene como estructura principal la ejecución de los 5 pasos de la teoría de restricciones. A partir de esto, al momento de la aplicación del paso 2, se identificó una serie de acciones de mejora, pero sin la ayuda de inversión económica, utilizando únicamente recursos propios del área analizada en la cual se detectó la restricción. Para el desarrollo de las acciones de mejora, se contempló la eliminación de lasmudas, que son los desperdicios detectados en el área de entalle, y, de manera conjunta, se implementaron las 5S, con énfasis en las tres primeras, debido a que se obtuvo una calificación baja en el informe de la línea base. Durante la ejecución de la metodología 5S, el jefe de calidad designó como responsables de la ejecución a los encargados del área de producción “entalle” (uno de cada turno: día y noche), los cuales tienen a su cargo la distribución de tareas de 5 operarios. Para Vargas (2002), la designación de un responsable es importante puesto que ayuda con el cumplimiento continuo de esta herramienta y, además, contribuye con la integración y capacitación de los trabajadores.
El modelo de balance de línea (variable independiente) aplicado influyó la productividad (variable dependiente), dado que se validó la hipótesis planteada por medio de un software estadístico. Tras el análisis de la estructura de costos final, se obtuvo un precio unitario de venta de S/ 69.11, que es menor al precio unitario de venta de la estructura de costos inicial, S/ 77.34. Esto resulta favorable para la empresa porque el producto se puede ofrecer a un precio inferior al del mercado, lo que permite captar más clientes sin que el margen de ganancias se vea afectado. La línea de producción quedará balanceada a una capacidad de 1200 m2, lo cual representa un aumento de 400 m2sobre la capacidad inicial; este balance de línea permitió aprovechar los recursos del área, tanto el uso y disponibilidad de la maquinaria como el tiempo empleado por los operarios.
Para Niebel y Freivalds (2004), la posibilidad para que un negocio crezca y aumente sus ganancias radica en el aumento de su productividad. Este mejoramiento de la productividad se traduce en un incremento de la cantidad de producción durante las horas de trabajo empleadas, tal como se puede apreciar al final de la aplicación del paso 4 del TOC, en donde la capacidad de la producción aumentó después de la implementación de las acciones de mejora y la inversión.
Para Andrade (2011), es más sencillo medir los beneficios que la adquisición de un activo tangible (maquinaria) puede generar para la empresa, que evaluar inversiones cuando el bien adquirido se relaciona, por ejemplo, con la contratación de personal. En esta investigación, se pudo determinar el valor de la rentabilidad con mayor facilidad debido a que gran parte de esta consistió en la adquisición de un taladro y el personal contratado solo aumentó en 2 operarios.
CONCLUSIONES
Para la implementación del modelo de balance de línea, esta investigación se basó en la ejecución de los 5 pasos de la teoría de restricciones, y se obtuvieron buenos resultados al utilizar herramientas delean manufacturing, como la detección y eliminación de desperdicios omudas, y herramientas de mejora continua, como la metodología de las 5S. Dichas herramientas fueron aplicadas de manera conjunta en las acciones de mejora establecidas en el paso 2 de la teoría de restricciones.
Para implementar correctamente la metodología 5S en el área de entalle y lograr una calificación aceptable en una auditoría final, es muy importante la capacitación del encargado de producción del área, quien guiará e involucrará al personal a su cargo para cumplir con los objetivos planteados.
Los resultados obtenidos tras la aplicación del modelo de balance de línea y la demostración de la hipótesis permitieron determinar que sí hubo una mejora en la productividad, dado que al ejecutar las acciones de mejora fue posible aprovechar mejor los recursos del área y obtener una mayor capacidad de procesamiento, y, en consecuencia, disminuir los costos de producción, lo que se pudo apreciar en la estructura de costos final.
Respecto al análisis sobre la investigación realizada, en este proyecto es factible medir el valor del ROI de la implementación del modelo de balance de línea, según el cual se obtuvieron resultados positivos para la rentabilidad de la empresa.
Este modelo de balance de línea se podría aplicar en una primera instancia a otras organizaciones del mismo rubro, puesto que la mayoría de las empresas de procesamiento de vidrio templado del país (7 en total) suele tener la misma problemática de contar con una baja productividad en sus procesos. Esto dado que sus líneas de producción son muy similares y están conformadas por el mismo tipo de maquinaria y distribución de operarios, por lo tanto, se tendrían las mismas condiciones iniciales y se podría lograr un incremento de la productividad después de la aplicación del modelo de balance de línea, en vista de que fue beneficiosa para este caso de estudio.
RECOMENDACIONES
Se recomienda analizar la línea de procesamiento de vidrio templado de manera continua, tomando como referencia el modelo de balance de línea planteado con la finalidad de erradicar de manera oportuna las nuevas restricciones que puedan presentarse en la línea de producción y así evitar que se convierta en una limitante.
No se deben equilibrar las capacidades productivas de cada área de producción de forma individual; el objetivo debe ser obtener un flujo de producción equivalente al exigido por la demanda del área comercial.
Se pueden aplicar herramientas delean manufacturingy de mejora continua como la detección y eliminación demudas, y la metodología de las 5S, que fueron utilizadas en el modelo de balance de línea. Estas pueden ser aplicadas en otras áreas de la empresa como mantenimiento, almacenes, oficina, etc., para obtener resultados positivos.
La capacitación constante de los trabajadores (encargados de área) que apoyarán en la implementación de la tecnología 5S es importante, debido a que ellos tienen contacto directo con los operarios de su turno de trabajo y son quienes manejan las máquinas.