Servicios Personalizados
Revista
Articulo
Indicadores
-
Citado por SciELO
Links relacionados
-
Similares en SciELO
Compartir
Industrial Data
versión impresa ISSN 1560-9146versión On-line ISSN 1810-9993
Ind. data vol.25 no.1 Lima ene./jun. 2022 Epub 31-Jul-2022
http://dx.doi.org/10.15381/idata.v25i1.19686
Design and technology
Data Processor to Estimate Raw Meal Dosing for Cement Manufacture
1 Chemical engineer. Currently working as professor at Universidad Nacional de San Agustín (Arequipa, Peru). E-mail: npompilla@unsa.edu.pe
2 PhD in Environmental Science and Technology. Industrial engineer. Currently working as professor at Universidad Nacional de San Agustín (Arequipa, Peru). E-mail: ptanco@unsa.edu.pe
3 Master in Industrial Engineering. Currently working as professor at Universidad Nacional de San Agustín. (Arequipa, Peru). E-mail: oangulo@unsa.edu.pe
4 Bachiller in Chemical Engineering. Currently working as an independent consultant (Arequipa, Peru). E-mail: vgonza@gmail.com
5 Bachiller in Computer Science. Currently working as an independent consultant (Arequipa, Peru). E-mail: dneyra@gmail.com
In the cement industry, the dosing of raw materials is an important stage in which mixtures called cement raw materials are obtained. The chemical and mineralogical composition of the clinker and the type of cement to be produced will depend on the content of these raw mixtures. Empirical calculation methods are usually used to determine the appropriate raw meal proportions; in practice, application of such methods is difficult due to their complexity and the limited use of conventional programs. In this applied research, a data processor was designed to estimate the chemical composition of raw meal. The methodology involved the development of equations, the design of the program and its validation. Its functionality, effectiveness and interaction with the user were verified based on the results, obtaining a processor that adequately manage data related to raw materials and cement type, and obtains very acceptable results.
Keywords: cement; raw meal; data processor; dosing.
INTRODUCTION
Cement has become a necessary commodity for humankind and its industrialization has evolved greatly since ancient times. It is a building material that sets automatically as a result of chemical reactions with water. It is made of finely ground clinker and calcium sulfate or natural gypsum (Verein Deutscher Zementwerke [VDZ], 2012). The raw material undergoes several stages or transformation processes and rigorous quality control in order to obtain cement. One of the most important stages is the dosing of raw materials, where they are mixed in different proportions to obtain cement raw meal (Fernández, 1967; Soria, 1982) or raw flour with specific compositions, which is essential to obtain cements and clinkers with desired chemical and mineralogical compositions. The raw materials extracted from the soil or from quarries do not have homogeneous chemical and mineralogical composition, so it is necessary to adjust them by applying complex mathematical calculations (Duda, 1977) based on empirical modules that in practice are difficult due to their complexity and the use of Excel spreadsheets.
This research aimed to develop a data processor that simplifies the formulation of raw material mixtures for the dosing of raw materials -so as to obtain specific cement types with the desired chemical composition- and that provides accurate estimates of the correct raw material proportions. For this purpose, a practical, specific and flexible data processor was designed for the cement industry, using empirical formulas such as lime saturation factor and different cement modules (silica, alumina and hydraulic modules) widely used in the industry since ancient times, complex mathematical equations of up to four (4) variables, and computer program. Its functionality, effectiveness and interaction with the user was assessed based on the management of data related to the dosing of the raw material and the type of cement to be obtained.
The designed data processor becomes a useful field tool to assist cement manufacture companies and researchers, as well as to design new types of cement with the addition of new materials or new formulations. According to Vizcaíno-Andrés et al. (2015), the development of new cementitious systems to increase clinker substitution to 50% without significantly affecting cement performance is feasible. In turn, Verein Deutscher Zementwerke states that for cement to meet the stipulated quality requirements, the composition of the raw material must be respected (2012). The contribution of this article to knowledge is framed in the application of science to information and communication technology based on the Visual Studio Community 2015 software and C# programming language, which consisted of the application of various interfaces that facilitated the application of calculation methods, providing acceptable results with minimal errors whose values ranged between 0.0046% and 0.0262%. Such contribution is relevant and novel in terms of the application and usefulness of the data processor, considering that the program also had a SQL Server database that allowed an adequate management of the information related to the raw material, raw meal or raw flour, clinker and the type of cement to be obtained, and because the results obtained from the interaction were very acceptable. This research contributes to further the study on the subject by applying, on the one hand, computer programs and programming languages related to the technology and, on the other hand, mathematical equations and calculation methods existing in the cement industry.
Raw Meal Composition
The raw material used in the manufacture of cement makes up cement raw meal (Figure 1). These materials are mineral substances found in nature such as limestone, clay or marl and iron ore. The main raw material is limestone, composed of calcium carbonate (CaCO3), which represents approximately 80% of the content of cement raw meal (Rodríguez, 2017a) and usually has magnesium carbonate (MgCO3) impurities; clay, composed of hydrated aluminosilicate, represents the remaining 20% and usually has iron oxide impurities (Rodríguez, 2017a; Espinoza, 2015; Telschow, 2012). Raw materials and raw meal contain the essential components of cement which are lime or calcium oxide (CaO), silica or silicon dioxide (SiO2), alumina or aluminum trioxide (AI2O3), and iron ore or iron trioxide (Fe2O3) (VDZ, 2012; Ramírez, 2000), limestones (CaO contributors) and clays (SiO2, AI2O3 and Fe2O3 contributors) (British Geological Survey [BGS], 2005; Labahn & Kohlhaas, 1985). Occasionally, corrective ingredients are also used. These compounds are rarely found in a single raw material and in the needed proportion; to obtain a cement raw meal, a raw material with abundant calcareous components, i.e., rich in lime, is usually chosen along with other clayey or lime-poor components, the latter containing more alumina and iron oxides, these two components being limestone and clay (Duda, 1977).
Cement raw meal or raw flour is a mixture of dosed, ground and homogenized materials. The composition of the raw meal depends on the specifications of the type of cement to be produced, the production process to be followed and the equipment available. Due to its compounds, raw meal provides approximately 95% of the main oxides to the clinker; the materials are dosed according to the required chemical composition in the cement, so it is advisable to maintain a quality control of the raw materials, from their extraction to their use in the cement industry (Montante, 1999; López, 1997).
Raw Material Dosing in the Cement Manufacturing Process
As shown in Figure 2, the cement manufacturing process begins with the extraction of raw materials (limestone, clay and corrective materials), which are crushed and ground to reduce their size to approximately 2mm. Next follows the raw meal production stage, which involves the selection of materials according to the intended mix design (Asociación de Productores de Cemento [ASOCEM], 2016) or dosing of the raw material, which is then homogenized and ground in order to obtain a very fine material with a particle size of less than 0.2 mm (ASOCEM, 2016), known as cement raw meal or raw flour. This raw meal is introduced to a heat exchanger at temperatures between 950 and 1100°C where preheating occurs, then, it enters the rotary kiln to continue with the firing process, completing the decarbonation of the material and the physical-chemical transformation of the mineralogical compounds or clinkerization at temperatures between 1300 and 1450°C. Subsequently, it is rapidly cooled in grate coolers to a temperature between 90 and 120°C, resulting in clinker with alite and belite crystals (Espinoza, 2015; Ramayo, 2008; Brouwers, 2007). Finally, the clinker is mixed with gypsum and undergoes a final grinding to obtain cement, an extremely fine product (ASOCEM, 2016).
Obtaining the raw meal is a very important part of the process, especially the dosing of raw materials; it depends on correct dosing to obtain a mixture of raw meal or raw flour that, after becoming cement, complies with the quality requirements according to each country’s regulations (Espinoza, 2015). It is necessary to estimate a correct mix of raw materials in order to obtain cement and clinker types with the needed composition, both chemical and mineralogical. This is accomplished by dosing the raw material using mathematical calculations or methods used in the cement industry. For instance, among the most commonly used are the silicate, alumina and hydraulic cement module, the alligation alternate method, the lime saturation factor method and Kind’s formula, the latter two are applied for limestone and clay mixtures (Duda, 1977). However, these methods prove to be overly wearisome and complicated when more than two raw materials are used or several raw materials are combined.
For the dosing of the raw meal, the percentages of the mineral components CaO, SiO2, Al2O3 and Fe2O3 must be determined by weight; the nomenclature C, S, A and F is commonly used (Rodríguez, 2017b). The amount of CaO produced by CaCO3 in limestone and the amount of silica, alumina and iron in clay are measured (Rodríguez, 2017a). Adjustments are also made using chemical control modules that establish a relationship between the mineral components; such relationships are called saturation factors, ratios or modules, which have emerged over time, owing to good judgment and good results with regard to clinker production and the manufacture of different types of cement (Espinoza, 2015). The control modules and ranges of values required are the hydraulic module, which values vary between 1.7 < HM < 2.3; the lime saturation factor measured by Kind’s formula, which values vary between 0.8 < KSk < 0.95; the silicate module, which values vary between 2.2 < MS < 2. 6; and the alumina ratio, which values vary between 1.5 < TM < 2.5 (Rodríguez, 2017a; Ramírez, 2000; Duda, 1977). If the values obtained in the modules are between the determined ranges it means that the limestone and clay used are suitable for cement manufacturing (Rodríguez, 2017a; Ramírez, 2000; Duda, 1977). To obtain a cement raw meal that complies with the desired chemical composition using the available raw materials, it is necessary to add certain quantities of other raw materials that will act as corrective materials, which must contain high concentrations of the oxides present in small quantities in the main raw materials, and which are necessary to obtain a desired raw meal, avoiding the excess of oxides that do not contribute to the cement manufacturing process (Castillo, 2015; Ramayo, 2008).
Clinker Composition
Clinker is the intermediate and main product of Portland cement, and it is “essentially a mixture of calcium silicates and smaller amounts of calcium aluminates responsible that react with water and cause cement to set” (BGS, 2005, p. 3). It is produced upon firing of the main components (limestone, clay, sand and iron) and a series of chemical reactions that occur between finely ground solids (Montante, 1999). Upon firing, the physicochemical transformation of the mineral components takes place, producing new compounds such as clinker. As shown in Figure 3, the new compounds formed are 3CaO.SiO2, called tricalcium silicate (C3S); 2CaO.SiO2, called dicalcium silicate (C2S); 3CaO. Al2O3, referred to as tricalcium aluminate (C3A); and 4CaO [Al2O3.Fe2O3], referred to as tetracalcium ferrite aluminate (C4AF) (Rodríguez, 2017b), which are commonly referred to as alite, belite, aluminate, and celite or ferrite, respectively. After a rapid cool down, crystals are formed, which are mostly alite and belite, and aluminate and celite in smaller proportions (Rodríguez, 2017a; Espinoza, 2015; Ramayo, 2008; Brouwers, 2007; López, 2000).
On average, clinker composition is 46%-79% tricalcium silicate (C3S), 5-30% dicalcium silicate (C2S), 6-18% tricalcium aluminate (C3A), 4-16% tetracalcium ferritoaluminate (C4AF), 0.1-4% free lime (CaO) and 0.7-1.5% free magnesium oxide (MgO) (Sanjuán and Chinchón, 2014). Calcium silicates and aluminates give cement its distinctive setting characteristics in the presence of water (VDZ, 2012). Two phases are distinguished in the formation of clinker, a solid phase (composed of C3S and C2S) that constitutes 80% of the clinker and a liquid phase (composed of C3A and C4AF) that constitutes between 10 - 20%, the latter bond, agglutinate or bind the tricalcium and dicalcium silicates (Rodríguez, 2017a). Alite or tricalcium silicate is the compound that contains the most CaO and largely determines the properties of cement, hardens quickly and achieves high strength; tricalcium aluminate reacts with water immediately, which is conducive to the rapid setting of cement (Rodríguez, 2017a; Sanjuán and Chinchón, 2014; Montante, 1999). Gypsum is added to slow setting. Free lime (CaO) and periclase (MgO) are lesser components of clinker that react with water to form calcium hydroxide and magnesium hydroxide, increasing their volume which can cause harmful expansions, so the content of free CaO and MgO is limited by regulations (Sanjuán & Chinchón, 2014; Montante, 1999). Each type of cement contains the four main compounds, but in different proportions.
METHODOLOGY
The first step was to contextualize the cement manufacturing data, before moving on to determine the parameters of the raw material dosing to obtain the composition of cement raw meal suitable for the production of clinker and types of cement with the desired characteristics. The data processor was designed by finding and determining the necessary mathematical equations and then converting them into C# language codes and inserting them into the program. In addition, Visual Studio Community 2015 and the C# programming language were used, which has the necessary tools to create programs (Johnson, 2015) and suitable interfaces for user interaction and data management with SQLServer (Pompilla, Gonza & Vera, 2019). The program design is user-friendly, easy to install and simple to use so that engineers, researchers and users of the cement industry can have a tool that expedites calculations and, above all, can be used in the field. The effectiveness of the calculations, the application and functionality of the data processor were validated in the field, using raw materials from the Yura S.A. cement quarry.
Equations for the Design of the Program
There are mathematical equations available to calculate the composition of raw cement, which determine the proportions of raw materials required to blend and obtain a raw meal, clinker and cement with the desired chemical and mineralogical compositions. Portland cement clinker is composed of oxides such as CaO (calcium oxide or lime), SiO2 (silicon oxide or silica), Al2O3 (aluminum oxide or alumina) and Fe2O3 (iron oxide); the component or oxide that is found in greater quantities is CaO and SiO2, Al2O3 and Fe2O3 are found in smaller proportions.
The different calculation methods that relate the compositions of the raw material, raw meal, clinker and cement include the four aforementioned oxides, any other component that intervenes is called “rest” whose purpose is to delimit the mathematical equations with the exception of SO3 because it is a restrictive component; it is also necessary to consider the “loss on ignition” value, which is the material that vaporizes during the firing process (Pompilla et al., 2019). To know the percentage ratio of the various components in the final product, cement modules are used, with values that are characteristic of each type of Portland cement. Over the years, the cement industry has worked empirically using equations and formulas called cement modules, which over time have given good results and are still used today.
Estimates performed by the program for raw meal dosing consider the quantity or number of raw materials and the main oxides used, which are CaO, SiO2, Al2O3 and Fe2O3. The methods described use mathematical equations that relate two, three or four raw materials. For two raw materials, a calcareous and a clayey material are mixed, the calcareous material contains a high proportion of CaO and the clayey material contains a higher amount of SiO2, Al2O3 and Fe2O3. It is possible to employ two calculation methods, one of them is the hydraulic method (HM), equation (1), which relates the four main oxides and whose value for a standard cement is in the range of 1.7 to 2.3 (Pompilla et al., 2019; Duda, 1977); the other is Kind’s formula (Ksk), equation (2), which relates the degree of saturation by lime, whose value fluctuates between 0.80 and 0.95.
To determine the proportions, X parts of limestone will be needed for 1 part of clay; the value of X is obtained by applying equations (3) and (4), using the hydraulic module (HM) and Kind’s (Ksk) formula (Pompilla et al., 2019; Duda, 1977). It should be noted that henceforth cal will be used for limestone, arc for clay, corI for corrective material I and corII for corrective material II.
As for three raw materials, limestone, clay and corrective materials are used; corrective materials are raw materials that contain fundamental oxides that are scarce in the main raw material. The silicate module (SM), using equation (5), which values range between 2.2 and 2.6 for a normal cement, and Kind’s formula can be used to determine the proportions of limestone and clay. Kind’s formula uses equation (6) and the silicate module uses equation (7); equations (8) and (9) provide the proportions of limestone (X) and clay (Y) (Pompilla et al., 2019; Duda, 1977).
Where the values of r, s and t are variable. Limestone (X) and clay (Y) proportions result from applying equations (8) and (9).
As for four raw materials, limestone, clay and two corrective materials containing fundamental oxides that are scarce in the main raw material are used. Calculations are similar to those for three raw materials, with the difference of the increase of one equation for three variables: X, Y, Z (as parts of limestone, clay and corrector I). In this case, we use the alumina ratio (TM) following equation (10), which value ranges between 1.5 - 2.5, and Kind’s formula using equation (11). As for the silicate module (SM), equation (12) is used, and for the alumina module, equation (13) is used. Finally, u is assigned as variable value, X parts of limestone, Y parts of clay and Z parts of corrective material I and corrective material II (Pompilla et al., 2019; Duda, 1977).
The silicate module (SM) and alumina ratio (TM) calculations are calculated using equations (12) and (13).
The values of X, Y, Z are calculated using equations (14), (15) and (16).
Program Data and Minimum Requirements
The above formulas and equations were converted into C# codes or programming language to be entered into the program; furthermore, it was complemented with the design applications of a suitable interactive environment. For the calculation of the cement modules, the mixing ratios of two, three or four raw materials and the components of the cement raw material in the values of X, Y, Z, the program uses the above-described equations in its own language.
The program was developed in Visual Studio Community 2015 with .NET Framework 4.6 and local SQLServer database (.mdf), with C# programming language. Users must have at least 1 GHz processor, Windows 7, 512 RAM and NET Framework 4.6 preinstalled to use the program.
Programming Code
A code is the set of written instructions to be followed by the computer to execute a program previously translated into binary code; in this case, the code of the designed data processor is the following:
private double f_HM(double s, double a, double f, double c)
{
return c/(s+a+f);
}
private double f_KS(double s, double a, double f, double c)
{
return (c-((1.65*a)+(0.35*f)))/(2.8*s);
}
private double f_SM(double s, double a, double f)
{
return s/(a+f);
}
private double f_TM(double a, double f)
{
return a/f;
}
private double f_X()
{
double a1 = (2.8*cemento*caliza)+(1.65*caliza)+(0.35*caliza)-(caliza);
double b1 = (2.8*cemento*arcilla)+(1.65*arcilla)+(0.35*arcilla)-(arcilla);
double c1 = corrector1-(2.8*cemento*corrector1+1.65*corrector1+0.35*corrector1);
double a2 = cemento*(caliza+caliza)-caliza;
double b2 = cemento*(arcilla+arcilla)-arcilla;
double c2 = corrector1-cemento*(corrector1+corrector1);
return (c1*b2-c2*b1)/(a1*b2-a2*b1);
}
private double f_Y()
{
double a1 = (2.8*cemento*caliza)+(1.65*caliza)+(0.35*caliza)-(caliza);
double b1 = (2.8*cemento*arcilla)+1.65*arcilla+0.35*arcilla-arcilla;
double c1 = corrector1-(2.8*cemento*corrector1+1.65*corrector1+0.35*corrector1);
double a2 = cemento*(caliza+caliza)-caliza;
double b2 = cemento*(arcilla+arcilla)-arcilla;
double c2 = corrector1-cemento*(corrector1+corrector1);
return (a1*c2-a2*c1)/(a1*b2-a2*b1);
}
Data Processor Start-Up
The start-up of the data processor was aimed at testing its effectiveness in data processing, for this purpose three raw material samples were used to validate it. The analyses were obtained from the archives of the Quality Control area of the cement company Yura S.A. corresponding to the years 2014, 2015 and 2016 (Arenas, 2016; Llacsa, 2015), as shown in Table 1. The combinations of raw materials resulted in the raw meals shown in Table 2 and the chemical composition of the clinkers obtained shown in Table 3. First, calculations were performed manually, obtaining the raw material dosing data; second, Excel spreadsheets were used to obtain data more rapidly; third, the data processor designed and named PRO4MIXCEM (Pompilla et al., 2017) performed the same calculations. The performance and effectiveness of the data processor was finally verified by comparing the three methods of calculation, where minimal differences were observed in the results obtained and the advantages of using the designed data processor compared to the first two methods of performing the calculations were noted.
Table 1 Chemical Composition of Portland Cement Raw Material in Different Samples.
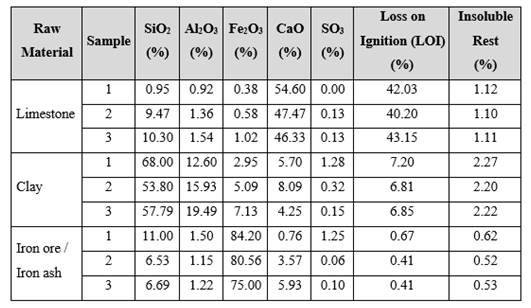
Source: Adapted from Llacsa (2015) and Arenas (2016).
Table 2 Chemical Composition of Portland Cement Raw Meal in Different Samples.
Raw Meal Samples | SiO2 (%) | Al2O3 (%) | Fe2O3 (%) | CaO (%) | SO3 (%) | Loss on Ignition (LOI) (%) | Insoluble Rest (%) |
---|---|---|---|---|---|---|---|
Raw Meal 1 | 14.64 | 3.28 | 2.15 | 43.92 | 0.28 | 34.38 | 1.34 |
Raw Meal 2 | 13.94 | 2.17 | 1.89 | 43.25 | 0.09 | 31.20 | 1.42 |
Raw Meal 3 | 13.64 | 2.11 | 2.88 | 42.57 | 0.08 | 32.06 | 0.98 |
Source: Adapted from Llacsa (2015) and Arenas (2016).
Table 3 Chemical Composition of Portland Cement Clinker in Different Samples.
Clinker Samples | SiO2 (%) | Al2O3 (%) | Fe2O3 (%) | CaO (%) | SO3 (%) | Loss on Ignition (LOI) (%) | Insoluble Rest (%) |
---|---|---|---|---|---|---|---|
Clinker 1 | 22.31 | 5.01 | 3.28 | 66.93 | 0.43 | 0.00 | 2.04 |
Clinker 2 | 22.32 | 3.89 | 3.19 | 65.85 | 0.33 | 0.50 | 1.99 |
Clinker 3 | 21.51 | 3.70 | 4.49 | 65.19 | 0.52 | 0.35 | 2.13 |
Source: Adapted from Llacsa (2015) and Arenas (2016).
RESULTS AND DISCUSSION
During the application and validation of the data processor, its functionality was evaluated by verifying the ease of use of the program, its effectiveness in providing true and real data, its interaction with the user with easily accessible environments and user understanding. The following results were obtained.
Functionality, Effectiveness and User Interaction
The program featured several interfaces. The login interface has two options. The first one is for registered users and the second one is for free users, with a “New” option to register the new user. For the implementation of the program, a test user (negu) was used to log in, as shown in Figure 4.
After logging into the program, it directed us to the Control Panel Interface, as shown in Figure 5, which provides access to all the visible functions corresponding to the different operations involved in obtaining and designing cement. From there, we had access to the registered database of cement types, raw materials and results in order to make modifications, as well as to delete and/or create data.
In the Cement-Database Interface the desired cement type was chosen and entered. The new cement was named Cemento Prueba [Test Cement], as shown in Figure 6. The desired chemical composition for this type of cement was entered, extracted from Table 3: 22.31% SiO2, 5.01% Al2O3, 3.28% Fe2O3, 66.93% CaO and 0.43% SO3. Upon entering the chemical composition, the program provides a hydraulic module of 2.1873, a Ksk of 0.9207, a silicate module of 2.6912 and an alumina ratio of 1.5274. It should be noted that all the data entered into the program is stored in its database.
The raw material to be used, which consisted of limestone, clay and corrective material rich in Fe2O3, was entered into the program. At the Cement-Raw Material Interface, a limestone named Caliza Prueba [Test Limestone], a clay named Arcilla Prueba [Test Clay] and some corrector material rich in Fe2O3 named Cenizas Fe de Prueba [Test Iron Ash] were input, which data were extracted from Table 1 and stored in the database, as shown in Figure 7.
Using the values input in the Cement Type and Raw Materials Interfaces and stored in the database, the correct raw material dosing was determined in the Cement Production Interface as shown in Figure 8. In this interface, the type or types of cement to be obtained were selected. As for Cemento Prueba, the number of raw materials was specified (three), and as well as the amount of cement (clinker weight) to be obtained, which was 100 MT.
The number of raw materials to be used is verified in the Raw Material Selection Interface. In this case, three (3) raw materials were selected and previously saved as Caliza Prueba [Test Limestone], Arcilla Prueba [Test Clay] and MFe. Ceniza Fe Prueba [Test Iron Ash] (MFe specifies the type of corrective material), as shown in Figure 9, and finally calculations were made.
The program performed the necessary calculations providing the results in the results interface with which the values of limestone, clay and iron ore were obtained, as shown in Figure 10. For this case, 52.3536 parts of limestone, 13.5005 parts of clay and 1 part of iron ore; 78.3102% of limestone, 20.194% of clay and 1.4958% of iron ore; and the weights (relative to the raw meal weight) were obtained. In addition, the chemical composition of the calculated cement raw meal and the clinker composition are shown along with their modules which are compared to the desired cement type, in this case Cemento Prueba [Test cement]. As can be seen, the modules differ slightly indicating a minimum error that fluctuates between 0 and 0.0262, this data can also be stored in the program’s database.
CONCLUSIONS
It was possible to design a practical and specific data processor to expedite calculations in real time, obtaining results of cement raw mixtures immediately, and thus obtaining clinkers and types of cements with the desired chemical and mineralogical composition, compared to other calculation methods that are usually long and complex. The designed data processor features a user-friendly environment that facilitates interaction with the user and provides results promptly; it is also useful and suitable as a support tool for the cement industry. It is suitable not only for obtaining raw material dosing, but also for obtaining new types of cements, new formulations or for introducing new raw materials, considering that many researchers are looking for a sustainable development of the cement industry.
ACKNOWLEDGMENTS
The authors extend their gratitude to Universidad Nacional de San Agustín de Arequipa for the support in the development of this research work.
REFERENCES
Arenas, C. J. (2016). Estudio comparativo de métodos vía clásica y vía instrumental (RI y DRX) para la determinación del contenido de puzolana en cementos con adición. (Tesis de grado). Universidad Nacional de San Agustín, Arequipa. http://repositorio.unsa.edu.pe/handle/UNSA/3270 [ Links ]
Asociación de Productores de Cemento. (2016). ¿Cuál es el proceso de fabricación del cemento?http://www.asocem.org.pe/productos-a/cual-es-el-proceso-de-fabricacion-del-cemento [ Links ]
British Geological Survey. (2005). Mineral profile: cement raw materials. https://www.cemnet.com/public/courses/srm01L1/story_content/external_files/Cement%20Raw%20Materials.pdf [ Links ]
Brouwers, H. J. H. (2007). Composición de la pasta de cemento Portland (Parte I).Cemento-Hormigón, (904), 4-28. https://josbrouwers.bwk.tue.nl/publications/Journal44.pdf [ Links ]
Castillo, P. (2015). Manual Práctico de Combustión y Clinkerización. https://vdocuments.mx/manual-practico-de-combustion-y-clinkerizacion.html [ Links ]
Duda, Walter. (1977). Manual Tecnológico del cemento. Barcelona, España: Editores Técnicos Asociados. [ Links ]
Espinoza, J. D. (2015).Desarrollar un modelo matemático de mezclas de materias primas en la línea de molienda de crudo caso: planta Guapán. (Tesis de pregrado). Universidad de cuenca, Cuenca. http://dspace.ucuenca.edu.ec/handle/123456789/21504 [ Links ]
Fernández, J. (1967). Dosificación de crudos de cemento Portland mediante el módulo de cal. Materiales de Construcción ,(125), 27-46. https://doi.org/10.3989/mc.1967.v17.i125.1665 [ Links ]
Johnson, B. (2015). Professional Visual Studio 2015 (1a ed.). John Wiley & Sons Inc. [ Links ]
Labahn, O., y Kohlhaas B. (1985). Prontuario del cemento. Barcelona, España: Editores Técnicos Asociados S.A. [ Links ]
Llacsa, V. R. (2015) Informe Técnico del Uso del equipo de Rayos X - Fluorescencia en el Control de Materia Prima, Producto Intermedio y Producto Final en la empresa Yura S.A. (Tesis de grado). Universidad Nacional de San Agustín, Arequipa. http://repositorio.unsa.edu.pe/handle/UNSA/3431 [ Links ]
López, P. (1997). Efecto de la incorporación de níquel en el clinker de cemento. (Tesis de maestría). Universidad Autónoma de Nuevo León, Nuevo León. http://eprints.uanl.mx/7734/1/1020120121.PDF [ Links ]
López, C. (2000). Estudio de aditivos aluminosos en el clinker y propiedades del cemento Portland. (Tesis de maestría). Universidad Autónoma de Nuevo León, Nuevo León. http://eprints.uanl.mx/7664/1/1020130155.PDF [ Links ]
Montante, M. (1999). Uso de aditivos en la producción de clinker de cemento Portland. (Tesis de maestría). Universidad Autónoma de Nuevo León, Nuevo León. http://eprints.uanl.mx/7935/1/1020125506.PDF [ Links ]
Pompilla, N., Gonza, V., y Neyra, D. (2017). PRO4MIXCEM Procesador de datos. Derecho de Autor. Registro de Programas de Ordenador (Software). N.° Partida Registral 00022-2017. Arequipa, Perú. http://servicio.indecopi.gob.pe/portal/SAE/ [ Links ]
Pompilla, N., Gonza, V., y Neyra, D. (2019). Procesador de datos como medio didáctico en la enseñanza-aprendizaje de asignaturas de materiales industriales en ingenierías. En E. Román, M. Porras, A. Madrigal, P. Medina y M. Ruíz (Eds.), Escenarios Educativos Latinoamericanos. Una mirada desde las universidades (pp. 126-141). Manabí, Ecuador: Ediciones UTM. [ Links ]
Ramayo, M. (2008).Dimensionamiento de un horno rotatorio para la producción de Clinker de cemento Portland. (Proyecto de fin de carrera). Universidad de Cádiz, Cádiz. http://hdl.handle.net/10498/6392 [ Links ]
Ramírez C., A. (2000).Rediseño de harinas crudas que permitan mayores incrementos en las adiciones activas. (Tesis de maestría). Universidad Autónoma de Nuevo León, Nuevo León. http://eprints.uanl.mx/id/eprint/796 [ Links ]
Rodríguez, A. (2017a, 1 de abril). Fabricación del Cemento de base Pórtland. [Video]. Youtube. https://www.youtube.com/watch?v=Oqrr9f9ZNPc [ Links ]
Rodríguez, A. (2017 b, 5 de abril). Composición potencial del Clínker de cemento Portland. [Video]. Youtube. https://www.youtube.com/watch?v=CG4n3liTG3o [ Links ]
Sanjuán, M., y Chinchón, S. (2014). Introducción a la fabricación y normalización del cemento portland. San Vicente del Raspeig, España: Publicaciones de la Universidad de Alicante. http://hdl.handle.net/10045/45347 [ Links ]
Soria, F. (1982). Composición quimicomineralógica de las materias primas y ahorro de energía en la industria del cemento. Materiales de Construcción, 32(186), 61-78. https://doi.org/10.3989/mc.1982.v32.i186.1029 [ Links ]
Telschow, S. (2012).Clinker Burning Kinetics and Mechanism. (Tesis doctoral). Technical University of Denmark, Kongens Lyngby. https://orbit.dtu.dk/en/publications/clinker-burning-kinetics-and-mechanism [ Links ]
Verein Deutscher Zementwerke. (2012). Environmental Data of the German Cement Industry. https://www.vdz-online.de/fileadmin/wissensportal/publikationen/umweltschutz/Umweltdaten/VDZ_Umweltdaten_Environmental_Data_2012.pdf [ Links ]
Vizcaíno-Andrés, L.M., Sánchez-Berriel, S., Damas-Carrera, S., Pérez-Hernández, A., Scrivener, K.L., y Martirena-Hernández, J.F. (2015). Industrial trial to produce a low clinker, low carbon cement. Materiales de Construcción,65(317), e045. https://doi.org/10.3989/mc.2015.00614 [ Links ]
Received: February 26, 2021; Accepted: January 03, 2022