INTRODUCCIÓN
El cemento se ha convertido en un bien necesario para la humanidad y su industrialización ha evolucionado enormemente desde tiempos muy antiguos. Es un material de construcción que fragua automáticamente como consecuencia de las reacciones químicas con el agua, está constituido por clínker finamente molido y sulfato de calcio o yeso natural (Verein Deutscher Zementwerke [VDZ], 2012). Para producir el cemento la materia prima es sometida a diversas etapas o procesos de transformación y a un riguroso control de calidad. Una de las etapas de mayor importancia es la dosificación de materias primas donde se mezclan en diferentes proporciones y se obtienen crudos de cemento (Fernández, 1967; Soria, 1982) o harina cruda con composiciones determinadas, pues de ella depende el obtener tipos de cementos y clínkeres con composiciones químicas y mineralógicas deseadas. La materia prima que brinda el suelo o las que se extraen de las canteras no tienen composición química ni mineralógica homogénea, por lo que es necesario ajustar dichas composiciones mediante la aplicación de cálculos matemáticos complejos (Duda, 1977) basados en módulos empíricos que en la práctica presentan dificultad por su complejidad y las aplicaciones de hojas de Excel.
El objetivo de la presente investigación fue desarrollar un procesador de datos que facilite la formulación de mezclas de materias primas en la dosificación de crudos, para obtener cementos predeterminados con la composición química deseada, y que brinde resultados con precisión en la estimación de las proporciones correctas. Para ello, se diseñó un procesador de datos práctico, específico y flexible para la industria cementera, con la aplicación de fórmulas empíricas como el grado de saturación y diferentes módulos (de silicatos, de alúmina e hidráulico) ampliamente utilizados en la industria desde tiempos remotos, ecuaciones matemáticas complejas de hasta cuatro (4) variables, y programas computacionales. Su funcionalidad, efectividad e interacción con el usuario fue evaluada con base en el manejo de datos relacionados con la dosificación de la materia prima y el tipo de cemento a obtener.
El procesador de datos diseñado se convierte en una herramienta de campo útil para asistir a las empresas productoras de cemento e investigadores del rubro, asimismo, permite diseñar nuevos tipos de cemento con la introducción de nuevos materiales o nuevas formulaciones. Según Vizcaíno-Andrés et al. (2015), el desarrollo de nuevos sistemas cementosos para aumentar la sustitución de clínker al 50% sin influenciar significativamente la actuación del cemento es factible; por su parte, Verein Deutscher Zementwerke menciona que para que el cemento cumpla con los requisitos de calidad estipulados, se debe respetar la composición de la materia prima (2012). La contribución del presente artículo al conocimiento se enmarca en la aplicación de la ciencia a la tecnología de la información y comunicación con base en el programa Visual Studio Community 2015 y lenguaje de programación C#, el mismo que consistió en la aplicación de diversas interfaces que facilitaron la resolución de los métodos de cálculo, proporcionando resultados aceptables con mínimos errores cuyos valores oscilaron entre 0.0046% y 0.0262%. Dicho aporte es relevante y novedoso por la aplicación y utilidad del procesador de datos, puesto que el programa contó además con una base de datos SQL Server que permitió un adecuado manejo de la información relacionada con la materia prima, el crudo o harina cruda, el clínker y el tipo de cemento a obtener, y porque los resultados obtenidos de la interacción fueron muy aceptables. El aporte de esta investigación es de expansión porque, por un lado, se han aplicado programas informáticos y lenguajes de programación relacionados con la tecnología y, por otro lado, se han aplicado ecuaciones matemáticas y métodos de cálculo existentes en la industria cementera.
Composición del crudo de cemento
La materia prima utilizada en la fabricación del cemento constituye el crudo de cemento (Figura 1), estas materias son sustancias minerales que se encuentran en la naturaleza como la caliza, arcilla o marga y mineral de hierro. La materia prima principal es la piedra caliza, compuesta por carbonato de calcio (CaCO3), pues representa aproximadamente el 80% del contenido del crudo de cemento (Rodríguez, 2017a) y suele tener impurezas de carbonato de magnesio (MgCO3); la arcilla, compuesta por silicato alumínico hidratado, representa el 20% restante y suele tener impurezas de óxido de hierro ((Rodríguez, 2017a; Espinoza, 2015; Telschow, 2012). Las materias primas y la harina cruda contienen los componentes esenciales del cemento que son la cal u óxido de calcio (CaO), la sílice o dióxido de silicio (SiO2), la alúmina o trióxido de aluminio (AI2O3), y el mineral de hierro o trióxido de hierro (Fe2O3) (VDZ, 2012; Ramírez, 2000), las calizas (aportadoras de CaO) y las arcillas (aportadoras de SiO2, AI2O3 y Fe2O3) (British Geological Survey [BGS], 2005; Labahn y Kohlhaas, 1985), en ocasiones, también se usan materiales correctores. Estos compuestos rara vez se encuentran en un solo material y en las proporciones deseadas; para obtener una mezcla de crudo de cemento, por lo general se elige una materia prima con abundantes componentes calcáreos, es decir, ricos en cal, con otros componentes arcillosos o pobres en cal, estos últimos contienen más alúmina y óxidos de hierro, estos dos componentes son la caliza y la arcilla (Duda, 1977).
El crudo de cemento o harina cruda es una mezcla de materiales dosificados, molidos y homogenizados. La composición de la harina cruda a obtener depende de las especificaciones del tipo de cemento a producir, del proceso productivo a seguir y de la instalación disponible. Por sus compuestos, la harina cruda le proporciona aproximadamente el 95% de los óxidos principales al clínker, los materiales se dosifican de acuerdo a la composición química deseada en el cemento, por lo que es conveniente mantener un control de calidad de las materias primas, desde su explotación hasta su uso en la industria cementera (Montante, 1999; López, 1997).
La dosificación de la materia prima en el procesamiento del cemento
El proceso de producción del cemento, como se muestra en la Figura 2, se inicia con la extracción de la materia prima (caliza, arcilla y correctores), la cual es triturada y molida para reducir su tamaño a 2mm aproximadamente. Se sigue con la etapa de la obtención del crudo que involucra la selección de los materiales de acuerdo al diseño de mezcla prevista (Asociación de Productores de Cemento [ASOCEM], 2016) o dosificación de la materia prima, que luego es homogenizada y molida a fin de obtener un material de gran finura con una granulometría menor a 0.2 mm (ASOCEM, 2016) que se conoce como crudo de cemento o harina cruda. Este crudo es introducido a un intercambiador de calor a temperaturas entre 950 y 1100°C donde ocurre la pre-calcinación, luego, ingresa al horno rotatorio para continuar con el proceso de cocción, completando la descarbonatación del material y la transformación físico-química de los compuestos mineralógicos o clinkerización a temperaturas entre 1300 y 1450°C. Posteriormente, se enfría rápidamente en enfriadores de parrilla hasta una temperatura entre 90 y 120°C, dando lugar a la obtención del clínker con la formación de cristales alita y belita (Espinoza, 2015; Ramayo, 2008; Brouwers, 2007). Finalmente, el clínker se mezcla con yeso y es sometido a una molienda final para obtener el cemento, un producto de alta finura (ASOCEM, 2016).
La obtención del crudo es una etapa de suma importancia, en especial la dosificación de materias primas; la obtención de una mezcla de crudo o harina cruda que tras convertirse en cemento cumpla con los requerimientos de calidad según normativa de cada país dependerá de una correcta dosificación (Espinoza, 2015). Para obtener tipos de cemento y clínkeres con la composición deseada, tanto química como mineralógica, es necesario estimar una mezcla correcta de materias primas. Esto se logra dosificando el crudo mediante cálculos matemáticos o métodos de cálculo utilizados en el rubro cementero, por ejemplo, entre los más utilizados se encuentran el método de cálculo según módulos de silicatos, de alúmina e hidráulico (o de agua), el método de cálculo cruzado, el método de grado de saturación de cal y la fórmula de Kind, estos últimos se aplican para mezclas de caliza y arcilla (Duda, 1977). Sin embargo, estos métodos resultan demasiado tediosos y complicados cuando se utiliza más de dos materias primas o se combinan varias materias primas.
Para la dosificación del crudo se deben determinar los porcentajes en peso de los componentes minerales de CaO, SiO2, Al2O3 y Fe2O3, se suele usar la nomenclatura C, S, A y F (Rodríguez, 2017b). Se mide la cantidad de CaO que produce el CaCO3 de la caliza y la cantidad de sílice, alúmina e hierro que posee la arcilla (Rodríguez, 2017a).También se realizan ajustes mediante módulos de control químico que relacionan los componentes minerales; a tales relaciones se les denomina factores de saturación, índices o módulos, los cuales han surgido a través del tiempo, debido al buen juicio y a los buenos resultados en su aplicación en la obtención de clínkeres y en la fabricación de diferentes tipos de cemento (Espinoza, 2015). Los módulos de control y rangos de valores necesarios son el módulo hidráulico, cuyos valores varían entre 1.7<HM<2.3; el grado de saturación por la cal medido mediante la fórmula de Kind, cuyos valores varían varía entre 0.8<KSk<0.95; el módulo de silicatos, cuyos valores varían entre 2.2<MS<2.6; y el módulo de alúmina, cuyos valores varían entre 1.5<TM<2.5 (Rodríguez, 2017a; Ramírez, 2000; Duda, 1977). Si los valores obtenidos en los módulos se encuentran entre los rangos determinados significa que la caliza y la arcilla utilizadas son aptas para la producción del cemento (Rodríguez, 2017a; Ramírez, 2000; Duda, 1977). Para conseguir la composición química deseada en el crudo de cemento con las materias primas disponibles, es necesario añadir ciertas cantidades de otras materias primas que actuarán como correctores, estos deben contener concentraciones elevadas de óxidos que se encuentran en cantidades escasas en las materias primas principales, y que son los que faltarán para obtener un crudo deseado, evitando el exceso de óxidos que no aportan para nada al proceso de la fabricación del cemento (Castillo, 2015; Ramayo, 2008).
Composición del clínker
El clínker es el producto intermedio y principal del cemento Portland, esencialmente es una mezcla de silicatos de calcio en mayor proporción y cantidades más pequeñas de aluminatos de calcio responsables de la reacción con el agua y fraguado del cemento (BGS, 2005). Se forma durante la calcinación de los componentes principales (caliza, arcilla, arena y minerales de hierro) y consiste en una serie de reacciones químicas que ocurren entre sólidos finamente divididos (Montante, 1999). Tras la calcinación, se produce la transformación físico-química de los compuestos minerales produciendo nuevos compuestos como el clínker. Como se muestra en la Figura 3, los nuevos compuestos formados son el 3CaO.SiO2, denominado silicato tricálcico (C3S); el 2CaO.SiO2, denominado silicato dicálcico (C2S); el 3CaO.Al2O3, denominado aluminato tricálcico (C3A); y el 4CaO [Al2O3.Fe2O3], denominado ferrito aluminato tetracálcico (C4AF) (Rodríguez, 2017b), que comúnmente se denominan alita, belita, aluminato y celita o ferrita respectivamente. Luego de un enfriado rápido se forman los cristales que en su mayoría son la alita y belita y en menor proporción de aluminato y celita (Rodríguez, 2017a; Espinoza, 2015; Ramayo, 2008; Brouwers, 2007; López, 2000).
La composición aproximada del clínker es de 46-79% de silicato tricálcico (C3S), 5-30% de silicato dicálcico (C2S), 6-18% de aluminato tricálcico (C3A), 4-16% de ferritoaluminato tetracálcico (C4AF), 0.1-4% de cal libre (CaO) y 0.7-1.5% de óxido de magnesio libre (MgO) (Sanjuán y Chinchón, 2014). Los silicatos y aluminatos de calcio confieren al cemento sus rasgos característicos de fraguado en presencia de agua (VDZ, 2012). Se distinguen dos fases en la formación del clínker, una fase sólida (compuesta por C3S y C2S) que constituye el 80% del clínker y una fase líquida (compuesta por C3A y C4AF) que constituye entre el 10 - 20%, estos últimos pegan, aglutinan o unen los silicatos tricálcicos y dicálcicos (Rodríguez, 2017a). La alita o silicato tricálcico es el compuesto que contiene más CaO y determina en gran medida las propiedades del cemento, endurece rápidamente y alcanza una gran resistencia; el aluminato tricálcico reacciona con el agua de forma inmediata, lo que propicia el rápido fraguado del cemento (Rodríguez, 2017a; Sanjuán y Chinchón, 2014; Montante, 1999). Se agrega yeso para retardar el fraguado. La cal libre (CaO) y la periclasa (MgO) son componentes minoritarios del clínker que reaccionan con el agua y forman hidróxido de calcio e hidróxido de magnesio, estos incrementan su volumen y pueden provocar expansiones dañinas por lo que el contenido de CaO y MgO libres está limitado según normatividad (Sanjuán y Chinchón, 2014; Montante, 1999); cada tipo de cemento contiene los cuatro compuestos principales, pero en diferentes proporciones.
METODOLOGÍA
Se inició con la contextualización de la información de la producción del cemento, se procedió a determinar los parámetros de la dosificación de materias primas para obtener la composición de crudos de cemento idóneos en la producción de clínkeres y tipos de cemento con las características deseadas. Para diseñar el procesador de datos, se procedió a deducir y desarrollar las ecuaciones matemáticas necesarias para luego convertirlas en códigos del lenguaje C# e insertarlas en el programa; además se aplicó Visual Studio Community 2015 y el lenguaje de programación C#, el cual posee herramientas necesarias para crear programas (Johnson, 2015) e interfaces adecuadas para la interacción de los usuarios y un manejo de datos con SQLServer (Pompilla, Gonza y Vera, 2019). El diseño del programa presenta entorno amigable, es fácil de instalar y sencillo de utilizar para que ingenieros, investigadores y usuarios de la industria cementera puedan contar con una herramienta que agilice los cálculos y sobre todo sea usado en campo. La eficacia de los cálculos, la aplicación y funcionalidad del procesador de datos fueron validadas en campo, utilizando materias primas provenientes de la cantera cementera Yura S.A.
Desarrollo de ecuaciones para el diseño del programa
Para calcular la composición del crudo de cemento se disponen de ecuaciones matemáticas, cuya aplicación determinan las proporciones de materias primas que se requiere para mezclar y obtener un crudo, clínker y cemento con composiciones químicas y mineralógicas deseadas. El clínker de cemento Portland está compuesto por componen óxidos como: CaO (óxido de calcio o cal), SiO2 (óxido de silicio o sílice), Al2O3, (óxido de aluminio o alúmina) y Fe2O3 (óxido de hierro); el componente u óxido que se encuentra en mayor cantidad es el CaO y en menor proporción se tiene al SiO2, Al2O3 y Fe2O3.
Los diferentes métodos de cálculo que relacionan las composiciones de la materia prima, del crudo, del clínker y del cemento incluyen los cuatro óxidos antes mencionados, a cualquier otro componente que intervenga se le denomina «restos» cuya finalidad es delimitar las ecuaciones matemáticas a excepción del SO3 por ser un componente restrictivo; también es necesario considerar las «pérdidas en rojo» que vienen a ser parte del material que se vaporiza en el proceso durante la cocción (Pompilla et al., 2019). Para conocer en qué relación porcentual se encuentran los diversos componentes en el producto final, se usan los módulos de cemento cuyos valores son característicos de cada tipo de cemento Portland. A lo largo de los años, en la industria cementera se ha trabajado de manera empírica utilizando ecuaciones y fórmulas denominadas módulos del cemento y que a través del tiempo han dado buenos resultados que se siguen utilizando en la actualidad.
Los cálculos que resuelve el programa en el dosificado del crudo consideran la cantidad o número de materias primas y los óxidos principales que son CaO, SiO2, Al2O3 y Fe2O3. Los métodos desarrollados utilizan ecuaciones matemáticas que relacionan dos, tres o cuatro materias primas. En el caso de utilizar dos materias primas, se mezclan un material calcáreo y un material arcilloso, el material calcáreo contiene alta proporción de CaO y el material arcilloso contiene mayor cantidad de SiO2, Al2O3 y Fe2O3. Se puede hacer uso de dos métodos de cálculo, uno de ellos es el método hidráulico (HM), la ecuación (1), que relaciona los cuatro óxidos principales y cuyo valor para un cemento estándar se encuentra en el intervalo de 1.7 a 2.3 (Pompilla et al., 2019; Duda, 1977); el otro se denomina fórmula de Kind (Ksk), ecuación (2), que relaciona el grado de saturación por la cal, cuyo valor varía entre 0.80 y 0.95.
Las proporciones de los componentes del crudo se determinan mediante la relación de 1 parte de arcilla por X partes de caliza, aplicando las ecuaciones (3) y (4) se obtiene el valor de X partes de caliza mediante el uso del módulo hidráulico (HM) y la fórmula Kind (Ksk) (Pompilla et al., 2019; Duda, 1977). Cabe resaltar que en adelante se utilizará la simbología cal para la caliza, arc para la arcilla, corI para el corrector I y corII para el corrector II.
Para el caso de tres materias primas se utilizan caliza, arcilla y correctores, los correctores son materias primas que contienen óxidos fundamentales que escasean en la materia prima principal. Es posible usar el módulo de silicatos (SM) mediante la ecuación (5) cuyos valores oscilan entre 2.2 y 2.6 para un cemento normal y la fórmula de Kind para determinar las proporciones de caliza y arcilla. Para la aplicación de la fórmula Kind se tiene la ecuación (6) y para el módulo de silicato la ecuación (7), las ecuaciones (8) y (9) proporcionan las proporciones de caliza (X) y de arcilla (Y) (Pompilla et al., 2019; Duda, 1977).
Donde los valores de r, s y t son variables. Las proporciones de caliza (X) y arcilla (Y) resultan de aplicar las ecuaciones (8) y (9).
Para el caso de cuatro materias primas se utilizan caliza, arcilla y dos correctores que contienen óxidos fundamentales que escasean en la materia prima principal. Los cálculos numéricos son similares al caso de tres materias primas, con la diferencia del aumento de una ecuación al tratarse de 3 incógnitas: X, Y, Z (como partes de caliza, arcilla y corrector I). Para este caso se emplea el módulo de alúmina (TM) según la ecuación (10), cuyo valor oscila entre 1.5 - 2.5, y la fórmula de Kind en la ecuación (11). Para el módulo de silicatos (SM) se tiene la ecuación (12) y para el módulo de alúmina se tiene la ecuación (13). Finalmente, se asume u como valor de variable, X partes de caliza, Y partes de arcilla y Z partes del corrector I y corrector II (Pompilla et al., 2019; Duda, 1977).
Los cálculos del módulo de silicatos (SM) y del módulo de alúmina (TM) se realizan mediante las ecuaciones (12) y (13).
Los valores de X, Y, Z se calculan mediante las ecuaciones (14), (15) y (16).
Datos del programa y requisitos mínimos
Las fórmulas descritas y las ecuaciones desarrolladas fueron convertidas en códigos o lenguaje de programación C# para insertarlas en el programa; además, se complementó con las aplicaciones de diseño de un entorno interactivo adecuado. Para el cálculo de los módulos del cemento, de las proporciones de mezcla de dos, tres o cuatro materias primas y de los componentes del crudo de cemento en los valores de X, Y, Z el programa hace uso de las ecuaciones anteriormente descritas en su lenguaje propio.
El programa fue desarrollado en Visual Studio Community 2015, con NET Framework 4.6 y base de datos SQLServer local (.mdf), con el lenguaje de Programación C#. Para usar el programa es necesario que el usuario cuente como mínimo con: procesador de 1 GHz, Windows 7, RAM 512 y NET Framework 4.6 preinstalado.
Código del programa
El código constituye el conjunto de líneas de texto con los pasos que debe seguir la computadora para ejecutar un programa previamente traducido al código binario; en el presente caso el código del procesador de datos diseñado es el siguiente:
private double f_HM(double s, double a, double f, double c)
{
return c/(s+a+f);
}
private double f_KS(double s, double a, double f, double c)
{
return (c-((1.65*a)+(0.35*f)))/(2.8*s);
}
private double f_SM(double s, double a, double f)
{
return s/(a+f);
}
private double f_TM(double a, double f)
{
return a/f;
}
private double f_X()
{
double a1 = (2.8*cemento*caliza)+(1.65*caliza)+(0.35*caliza)-(caliza);
double b1 = (2.8*cemento*arcilla)+(1.65*arcilla)+(0.35*arcilla)-(arcilla);
double c1 = corrector1-(2.8*cemento*corrector1+1.65*corrector1+0.35*corrector1);
double a2 = cemento*(caliza+caliza)-caliza;
double b2 = cemento*(arcilla+arcilla)-arcilla;
double c2 = corrector1-cemento*(corrector1+corrector1);
return (c1*b2-c2*b1)/(a1*b2-a2*b1);
}
private double f_Y()
{
double a1 = (2.8*cemento*caliza)+(1.65*caliza)+(0.35*caliza)-(caliza);
double b1 = (2.8*cemento*arcilla)+1.65*arcilla+0.35*arcilla-arcilla;
double c1 = corrector1-(2.8*cemento*corrector1+1.65*corrector1+0.35*corrector1);
double a2 = cemento*(caliza+caliza)-caliza;
double b2 = cemento*(arcilla+arcilla)-arcilla;
double c2 = corrector1-cemento*(corrector1+corrector1);
return (a1*c2-a2*c1)/(a1*b2-a2*b1);
}
Puesta en funcionamiento del procesador de datos
La puesta en funcionamiento del procesador de datos tuvo como objetivo comprobar su efectividad en el manejo de datos, para ello se validó con tres muestras de materias primas cuyos análisis fueron obtenidos de los archivos del área de Control de Calidad de la empresa cementera Yura S.A. de los años 2014, 2015 y 2016 (Arenas, 2016; Llacsa, 2015), como se observa en la Tabla 1. Las combinaciones de las materias primas dan lugar a los crudos los que se muestran en la Tabla 2 y la composición química de los clínkeres obtenidos se muestran en la Tabla 3. En primer lugar, se realizaron se realizaron los cálculos de forma manual, con lo que se obtuvieron los datos de la dosificación de la materia prima; en segundo lugar, se usaron hojas de cálculos Excel para obtener datos con mayor velocidad; en tercer lugar, se aplicó el procesador de datos diseñado y al que se le denominó PRO4MIXCEM (Pompilla et al., 2017) realizando los mismos cálculos. Finalmente, se verificó el funcionamiento y efectividad del procesador de datos, comparando las tres formas de proceder del cálculo, en donde se observaron mínimas diferencias en la obtención de resultados y se advirtieron las ventajas del uso del procesador de datos diseñado frente a las dos primeras formas de realizar los cálculos.
Tabla 1 Composición química de la materia prima del cemento Portland en diferentes muestras.
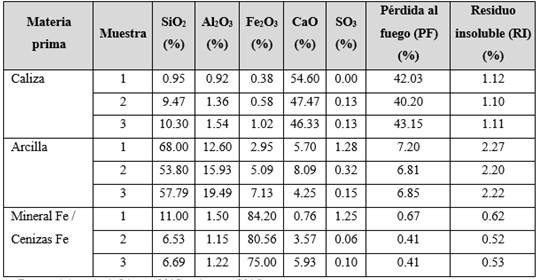
Fuente: Adaptado de Llacsa (2015) y Arenas (2016).
Tabla 2 Composición química de crudo de cemento Portland en diferentes muestras.
Muestras de crudo | SiO2 (%) | Al2O3 (%) | Fe2O3 (%) | CaO (%) | SO3 (%) | Pérdida al fuego (PF) (%) | Residuo insoluble (RI) (%) |
---|---|---|---|---|---|---|---|
Crudo 1 | 14.64 | 3.28 | 2.15 | 43.92 | 0.28 | 34.38 | 1.34 |
Crudo 2 | 13.94 | 2.17 | 1.89 | 43.25 | 0.09 | 31.20 | 1.42 |
Crudo 3 | 13.64 | 2.11 | 2.88 | 42.57 | 0.08 | 32.06 | 0.98 |
Fuente: Adaptado de Llacsa (2015) y Arenas (2016).
Tabla 3 Composición química de clínker de cemento Portland en diferentes muestras.
Muestras de clínker | SiO2 (%) | Al2O3 (%) | Fe2O3 (%) | CaO (%) | SO3 (%) | Pérdida al fuego (PF) (%) | Residuo insoluble (RI) (%) |
---|---|---|---|---|---|---|---|
Clínker 1 | 22.31 | 5.01 | 3.28 | 66.93 | 0.43 | 0.00 | 2.04 |
Clínker 2 | 22.32 | 3.89 | 3.19 | 65.85 | 0.33 | 0.50 | 1.99 |
Clínker 3 | 21.51 | 3.70 | 4.49 | 65.19 | 0.52 | 0.35 | 2.13 |
Fuente: Adaptado de Llacsa (2015) y Arenas (2016).
RESULTADOS Y DISCUSIÓN
Al realizar la aplicación y validación del procesador de datos se evaluó su funcionalidad verificando la facilidad de manejo del programa, su efectividad en brindar datos verídicos y reales, su interacción con el usuario con entornos de fácil acceso y entendimiento del usuario. Se obtuvieron los siguientes resultados.
Funcionalidad, efectividad e interacción con el usuario
El programa presentó diversas interfaces. La interfaz de ingreso tiene dos opciones, la primera como usuario registrado y la segunda como usuario libre, presenta una opción «Nuevo» que registra al nuevo usuario. Para la aplicación del programa se accedió con el usuario de prueba (negu), como se observa en la Figura 4.
Luego de ingresar al programa, este condujo a la interfaz Panel de Control, como se muestra en la Figura 5, desde el cual se accede a todas las funciones visibles que son las diferentes operaciones de la obtención y diseño del cemento; se tuvo acceso a la base de datos registrados de tipos de cementos, materias primas y resultados con la finalidad de realizar modificaciones, además de eliminar y/o crear datos.
En la interfaz cemento-base de datos se eligió y registró el tipo de cemento deseado, en este caso el nuevo cemento fue denominado Cemento Prueba, como se muestra en la Figura 6. Se ingresó la composición química deseada para este tipo de cemento, extraída de la Tabla 3: 22.31% de SiO2, 5.01% de Al2O3, 3.28% de Fe2O3, 66.93% de CaO y 0.43% de SO3. Al ingresar la composición química el programa provee un módulo hidráulico de 2.1873, un Ksk de 0.9207, un módulo de silicatos de 2.6912 y un módulo de alúmina de 1.5274; cabe señalar que todos los datos que se ingresan al programa almacenados en su base de datos.
El programa permitió registrar la materia prima a utilizar que consiste en de caliza, arcilla y un corrector rico en Fe2O3. En la interfaz cemento-materia prima se registró a una caliza llamada Caliza Prueba, una arcilla de nombre Arcilla Prueba y un corrector rico en Fe2O3 de nombre Cenizas Fe de Prueba, cuyos datos fueron extraídos de la Tabla 1 y almacenados en la base de datos, tal y como se observa en la Figura 7.
Con los valores ingresados en las interfaces del tipo de cemento y materia prima y registrados en la base de datos, se determinó la dosificación correcta de materia prima en la interfaz obtención del cemento como se muestra en la Figura 8. En esta interfaz se eligió el tipo o tipos de cemento que se deseaba obtener, en el caso Cemento Prueba, se definió el número de materias primas (tres) y la cantidad de cemento (peso del clínker) que se deseaba obtener, que fue 100 TM.
En la interfaz selección de materias primas se verifica el número de materias primas a utilizar, para el presente caso fueron 3, se seleccionaron las materias primas utilizadas y previamente guardadas como Caliza Prueba, Arcilla Prueba y MFe. Cenizas Fe Prueba (MFe especifica el tipo de corrector), como se observa en la Figura 9, finalmente se procedió a calcular para obtener los resultados.
El programa realizó los cálculos necesarios proporcionando los resultados en la interfaz de resultados con los que se obtuvieron los valores de caliza, arcilla y mineral de Fe, como se observa en la Figura 10. Para el presente caso se obtuvo 52.3536 partes de caliza, 13.5005 partes de arcilla y 1 parte de mineral de Fe; porcentajes de 78.3102% de caliza, 20.194% de arcilla y 1.4958% de mineral de Fe y los pesos (relativos al peso del crudo). Además, se muestra la composición química del crudo de cemento calculado y la composición del clínker junto con sus módulos que son comparados con el tipo de cemento deseado, en este caso Cemento Prueba. Como se observa, los módulos tienen una ligera diferencia que indica un error mínimo que fluctúa entre 0 y 0.0262, estos datos también pueden ser almacenados en la base de datos del programa.
CONCLUSIONES
Ha sido posible diseñar un procesador de datos práctico y específico con el fin de agilizar los cálculos en tiempo real, es decir, obtener resultados de mezclas de crudos de cemento de manera inmediata, y por ende obtener clínkeres y tipos de cementos con la composición química y mineralógica deseada, en comparación con otros métodos de cálculos que suelen ser largos y tediosos. El procesador de datos diseñado presenta un entorno amigable que facilita la interacción con el usuario y brinda resultados con prontitud; asimismo, resulta útil y adecuado como herramienta de apoyo a la industria cementera. Además de utilizarse para obtener mezclas de dosificación de materias primas, es adecuado para obtener nuevos tipos de cementos, para obtener nuevas formulaciones o introducir nuevas materias primas, dado que muchos investigadores buscan un desarrollo sostenible de la industria del cemento.