Servicios Personalizados
Revista
Articulo
Indicadores
-
Citado por SciELO
Links relacionados
-
Similares en SciELO
Compartir
Industrial Data
versión impresa ISSN 1560-9146versión On-line ISSN 1810-9993
Ind. data vol.25 no.1 Lima ene./jun. 2022 Epub 31-Jul-2022
http://dx.doi.org/10.15381/idata.v25i1.21499
Production and Management
Quantitative Measurement of Worker Protection from a Combined Perception of Occupational Safety and Health in a Graphic Advertising Company in Lima-Peru, 2021
1 Chemical Engineer and Economist. Currently teaching at Departamento de Diseño y Tecnología Industrial of the School of Industrial Engineering of the UNMSM (Lima, Peru). E-mail: mgodoym@unmsm.edu.pe
2 Industrial Engineer. Currently teaching at Departamento de Producción y Gestión of the School of Industrial Engineering of the UNMSM (Lima, Peru). E-mail: manuel.godoy@unmsm.edu.pe
3 Economist, researcher and business consultant. Currently working as an independent consultant (Lima, Peru). E-mail: gladysvdg@hotmail.com
The Occupational Health and Safety Management System (OHSMS) in the company under study was found to be deficient. The objective of this study is to identify which factors of an OHSMS are related to worker protection. For this descriptive and correlational study with a non-experimental cross-sectional design, data was collected using a survey addressed to 46 workers in June 2020. The result determined that there are 27 occupational risks affecting worker protection and the company; a Worker Protection Index (WPI) of 68% related to significant factors of the OHMSMS was also determined. It is concluded that the control measures on safe working environment, cleaning and maintenance and available common areas are the most significant factors related to worker protection in terms of reducing hazards, occupational risks, accidents and diseases. It is recommended that strategies be established to encourage worker commitment and participation.
Keywords: occupational risks; perception index; graphic advertising industry; occupational health and safety factors; worker protection.
INTRODUCTION
Safety in the workplace is a constant concern for the International Labor Organization (ILO) that should be a priority for all companies and institutions in every country. In its report, the ILO (2019) stated that 2.78 million deaths occur annually in the world due to work-related causes, of which 2.4 million are related to occupational diseases. These situations generate costs close to 3.94% relative to global GDP related to compensation, lost working man-hours, production stoppages, professional training and retraining, as well as medical care. Not to mention the suffering and emotional damage to the affected workers and their families. The high costs resulting from the lack of worker protection draw attention to this important issue that urgently needs to be resolved, where the human factor is the most relevant. Inter-American Development Bank (IDB) consultant Norman Mejía indicated in an interview that Peru registers a critical level in its fatality rate ranging between 13.5% and 13.8% (Gestión, 2016). This is compared to South America which reaches 13.5%; Europe, Japan and North America register a fatality rate of 3.5% (three times less than the cases in South America) and countries in Africa and Asia that register between 20% and 21.3%. The fatality or lethality rate is the probability of worker deaths caused by an unsafe work event (due to high occupational hazards) over a period of time, expressed as a rate per 10 000 workers.
Gonzáles, Mateo and Gonzáles (2010) define occupational hazards as the probability that a worker may suffer a work-related injury. Along these lines, Alvarez and Faizal (2012) mention that studies on occupational accidents and occupational diseases are classified by groups according to their impact on the integrity and health of the worker. The Ministerio de Trabajo y Promoción del Empleo (MTPE, 2021) reported in the 2020 SUNAFIL safety bulletins that in Peru alone more than 22 507 occupational accidents and 162 cases of fatal accidents were reported, indicating an annual fatality rate of 0.73% for 2020. This report shows that the most frequently reported accidents were those caused by false movements or physical exertion, falling objects, blows from objects, falling from heights, entrapment, collisions against objects and contact with chemicals. Statistically, physical exertion is the most frequent risk and annually accounts for about 12% in Peru. These involve lifting, pushing, pulling, handling, throwing objects, inadequate, prolonged and repetitive postures, which can cause occasional discomfort or non-lethal chronic problems (pain, discomfort, tension, irreversible deformities or even disability of the worker).
In today’s changing world, inclined to a high level of competitiveness, the ability to react and the time for decision making in companies are critical, therefore an efficient management is needed for the use of resources. In this context, human talent development must be guaranteed, yet, above all, worker protection must be ensured. In recent years, occupational health and safety in our country has acquired new guidelines and updates that have turned it into one of the most closely controlled standards for companies, even more so now that new regulations have been added due to the pandemic. As of 2020, COVID-19 has become the disease of greatest concern worldwide due to its high propagation rate and the respiratory and circulatory affections, in addition to other negative health consequences that it has on the human body. Therefore, companies must comply with the regulations of Law No. 29783 on Occupational Health and Safety and the Plan de Vigilancia COVID [COVID Surveillance Plan], Ministerial Resolution No. 972-2020 (2020), which will be taken as the legal basis for this study.
In the safety framework, occupational hazards and risk prevention management systems are topics commonly addressed based on data obtained from safety performance results for studies using quantitative methodologies. Occupational safety, according to Cortés (2007), should concern the analysis of accident risks, identify and improve the factors involved in occupational health and safety (OHS), and gain control of the consequences by means of safety techniques (determined methods and procedures).
Several contributions from research carried out in Peru have been collected from the literature review for this article. For instance, Atencio (2013) aimed to design preventive measures with an occupational accident protocol for a company in the construction sector and to determine the incidence of occupational accidents considering their characteristics. Likewise, Mosqueira (2016) designed a new management system applied to OHS for the plastics industry and identified 577 occupational risks, 43.67% of which were related to physical and mechanical factors. In addition, Ureta (2018) identified the working conditions of the nursing staff of the “Zacarías Correa Valdivia” hospital in Huancavelica related to occupational risks within the hospital. He designed a questionnaire in which they had to choose between three types of conditions: good, fair and poor; he found that 63.5% work in regular social conditions (personal relationships and communication), 58.7% work in fair physical conditions (physical, environmental and material resources), and 38.1% work in fair psychological conditions (complexity, time, attention and speed). Fair conditions should be understood as the degree of perception of the work environment to perform work in safe, healthy conditions that are not demeaning to human dignity.
An Occupational Health and Safety Management System (OHSMS) is defined as the company’s conditions and factors to ensure worker protection and that are related to the preventive culture, governance and technology that could impact the OHS of workers (administrative, operators, temps) or external parties (contractors, visitors or anyone in the workplace). An OHSMS involves the following responsibilities: (1) employer responsibility, to provide health and safety to workers in accordance with current legislation, and (2) worker responsibility, to comply with the company's internal OHS regulations (RISSO). Worker protection is a key variable that must be taken into account in the assessment of an OHSMS. In the view of Brunette (2003), from the University of Massachusetts, worker protection must include the elements of the work system that are considered among the factors of industrial health and safety. Consequently, in her doctoral thesis, she identifies the following 9 dimensions:
Safe work environment (accident and risk free).
OHS training.
Standards and rules (to prevent accidents).
Personal protective equipment (EPP).
Safety signs (visual signage).
Cleaning and maintenance (of equipment and work areas).
Common areas available (stairs, corridors, gardens, etc.).
Sanitary facilities (clean and tidy).
Cafeterias and canteens (clean and tidy).
The graphic printing production process mainly involves the use of printing presses, inks, dyes and chemical solvents. Consequently, the chemical exposure to strong fumes is high in this sector. All gas is considered a risk and a chemical pollutant, which reaches the lungs when inhaled and, when mixed with air, spreads quickly in the environment. It can be identified when an odor is perceived, and both its concentration and exposure time must be maintained within permissible limits so as not to affect health. Article 1 of MINSA’s DS No. 015-2005-SA, which sets out regulations on permissible limit values for chemical agents in work environments, stipulates that companies must llevar control de riesgos inherentes a exposición, principalmente por inhalación, de agentes químicos presentes en los puestos de trabajo [control the inherent exposure risks, mainly by inhalation, of chemical agents present in the workplace] (MINSA, 2005). Risks from vibrations and noise also cause diseases that lead to hearing disorders such as hypoacusis. On the other hand, the risk from viruses and bacteria is a permanent danger in companies due to the high potential for contagion. In recent times, pandemic outbreaks have made it necessary for health authorities to adopt measures to contain the spread of the disease by developing protocols for the control of biological agents, such as the COVID-19 Surveillance Plan pursuant to RM No. 972-2020-MINSA. Any biological risk involves the presence of a biological agent (virus, bacteria and fungi) that can be detrimental to health depending on its level of danger, which is determined by the worker’s exposure time and the concentration of the biological agent. Risk increases when work activities are performed in enclosed spaces.
The concepts of work and worker have evolved over time. It has become increasingly relevant to take into account the personnel to identify risk agents that affect OHS; therefore, it is necessary to consider each worker’s individual perception, in order to obtain a collective (group) perception that, when measured, becomes a new variable that has been called “worker’s perception of protection” in this study. It determines the effectiveness of an OHSMS, as the worker feels protected by the company when enjoying good health and well-being (absence of illness or risk of accident).
This study was conducted in a medium-sized company in the graphics and advertising sector in Lima, Peru, which is primarily engaged in the printing of banners and installation of advertising billboards, that reports shortcomings in the OHSMS assessment for worker protection. In June 2020, a preliminary study was carried out by the company’s OHS committee on the OHS assessment, which focused on three aspects: occupational risks, current regulations and worker protection. Regarding occupational risks, 27 potential risks were identified in the workplace, including chemical, biological, physical, ergonomic, and psychosocial risks that may affect worker protection, causing severe damage and affecting the company. Metalworking and digital printing are the processes that pose the greatest risk, and the most frequent accidents are caused by personnel falling from heights, electric shocks, dislocations, sprains, hand injuries and cuts, exposure to noise and vibrations. The most frequent occupational diseases include hypoacusis, hernia, low back pain, and COVID-19. It is concluded that preventive measures should be implemented within the company’s processes to address these occupational risks. As for the regulations, according to the provisions of Law No. 29783 and the COVID Surveillance Plan pursuant to R.M. No. 972-2020, it is apparent that the company does not guarantee the effectiveness of a management system that complies with the regulations in force to ensure worker protection. It is concluded that, due to non-compliance with current regulations, the company would potentially face fines amounting to 1.358 million soles, which represents 34% of its annual turnover, based on the scale of fines established by SUNAFIL, set forth in Law No. 28806 and in D.S. No. 019-2006-TR of the MTPE. As for worker protection, the company has not conducted a personnel assessment, nor is the degree of perception of its workers with respect to safety known. It is concluded that it is necessary to obtain this information immediately via a measuring instrument.
For this reason, we have designed a survey as an accessible means to determine the worker's perception degree regarding the safety of the work environment, whether it is an optimal and safe place, the situations that pose a threat to their safety and health, as well as suggestions to improve their work environment.
The general objective of this research is to determine the factors of the OHSMS that are related to worker protection in a graphic and advertising company in Lima-Peru. The results will be used to determine the necessary preventive measures to be implemented and included in the company. Therefore, it is crucial to determine the worker’s perception of protection. Hence, this research contributes to generating knowledge with the design and application of an indicator referred to as the worker protection index (WPI), expressed as a percentage and calculated from the respondents’ answers on an ordinal scale; it provides information on the worker’s individual perception of the occupational risks to which they are exposed and on the protection measures provided by the company, considering the dimensions related to the study. In the analysis of the results, the WPI considers time, person, place and personal perception. From the data it is possible to observe the evolution and trend according to the changes perceived. This research can be considered relevant and novel because no studies considering the perception of workers with respect to OHS in companies of the sector have been conducted in Peru yet. This research contribution is far-reaching and could be considered as part of the application of Law No. 29783 in accordance with its Protection Principle, seeing that companies do not consider the workers’ perception as a measurable indicator of the level of performance of the OHSMS provided by the company. This would make it possible to establish measures to correct deficiencies, raise awareness among employers in decision-making, and encourage occupational risk protection management with the participation of all personnel. The effectiveness of the OHSMS will depend on the data collected through the survey, identification of OHSMS factors and critical points from the personnel’s point of view that might have an impact on the causes of incidents and accidents, which is an essential part of occupational monitoring. Also, the OHSMS factors have been related to the preventive culture, governance and technology that the company offers to its workers. Table 1 shows the general hypothesis and its two variables and dimensions.
METHODOLOGY
This applied research used a descriptive and correlational approach to better analyze the characteristics of the dimensions of the OHSMS factors based on the workers’ perception. A personal survey was used to collect the necessary data and thus provide a more accurate group labor perception, allowing us to portray a situation within the Peruvian company in the graphic and advertising sector during the COVID-19 period. Based on the information obtained from the survey, it was possible to have a general picture of the OHSMS, the risks and hazards in a shared work environment, and the measures to be applied for collective labor prevention and protection.
This research follows a cross-sectional (non-experimental) design, and uses statistics such as the correlation coefficient test for independent samples to demonstrate the hypothesis of the study. According to Spearman’s theory (1984), ordinal variables, based on data collected from a perception, tend to have a greater probability of not conforming to a normal distribution, and these are precisely the conditions of this study. Such tests are intended to evaluate the degree of interdependence between two random variables, with a confidence level of 95%, and to determine whether there are significant differences between the variables (not exceeding an error of 0.05). Thus, it will be possible to relate the variables to each other so as to determine a correlation matrix that will be used to select the variables with the highest correlation, ideally greater than 50%, and thus establish a proposal for the OSHMS factors that influence worker protection. The Spearman’s coefficient (Rho) scale is presented in Table 2.
Table 2 Spearman’s Rho Correlation Coefficient.
Range | Correlation |
---|---|
De 0.00 a 0.25 | 1. Negligible or none |
De 0.26 a 0.50 | 2. Weak |
De 0.51 a 0.75 | 3. Moderate to strong |
De 0.76 a 1.00 | 4. Strong to perfect |
Source: Martínez, et al. (2009).
The study population was comprised of 50 workers exposed to occupational risks in the company. Simple random sampling and a finite population formulation were used, where N = 50 workers, “p” represents the possibility of occurrence of the event (p = 0.5), “q” represents the possibility of non-occurrence of the event (q = 0.5), “E” represents the sampling error of 5% (E = 0.05), and “Z” represents a statistic at a 95% confidence level (Z = 1.96), thus sample #1 is made up of 46 workers.
The survey and data analysis were used for data collection. The survey, with its instrument No. 1, was addressed to sample #1 of 46 workers and taken in June 2020. Nine dimensions of the variable “OSHMS factors” were analyzed in the survey according to the individual perception of each worker, allowing the definition of a measurable indicator called “worker protection index” (WPI). For the data analysis, the company's monthly statistical data related to occupational accidents (OT), occupational diseases (OD) and dangerous incidents (PI) were also used, all measured as number of unsafe events occurred over one year (from April 2019 to March 2020) and distributed respectively per worker, in addition, the WPI is included to determine the dimensions of the variable “worker protection”. It is worth mentioning that the statistical data provided by the company have been considered as valid under a commitment of Management to make the necessary adjustments, appealing to the Principle of Primacy of Reality according to Law No. 29783.
The survey consisted of a questionnaire with 34 questions to analyze nine dimensions taken from Brunette's study (2003), as shown in Table 4. Polytomous questions with a five-point Likert scale are also used to measure different constructs. The Likert (1932) scale is one of the most widely used for measuring attitude. According to Ospina et al. (2005), the Likert scale allows determining an order of objects, classifying individuals according to the degree to which they possess a certain attribute, but it does not provide an idea of the distance that exists between them. For this case, 5 ordinal grades are used, as shown in Table 3. The worker protection index (IPT) was considered when processing the survey responses, which is a percentage index calculated from the sum of the survey responses (June 2020) divided by 7820 maximum points obtained by multiplying 34 questions with 5 maximum points and 46 workers, that is, 34x5x46. Thus, it is possible to collect the necessary data and create a table containing the answers of 46 workers and the results of 4 indicators of the annual OHS management in particular. The data is then processed for hypothesis testing using SPSS 26 software.
Table 3 Likert Scale Applied in the Survey.
Scale | 1st | 2nd | 3rd | 4th | 5th |
---|---|---|---|---|---|
Level of agreement | Strongly disagree | Disagree | Neither agree nor disagree | Agree | Strongly agree |
Source: Ospina et al. (2005).
A content validation test was conducted to validate instrument No. 1 with the support of three experts who evaluated the instrument as recommended. Based on Hernández, Fernández and Baptista (2014), each judge, independently, proceeds to i) read the objectives and data collection instructions given to him/her, ii) carefully read each of the items of the instrument, iii) evaluate each of the items, on the corresponding five-point Likert scale, taking into account the criteria of relevance, conceptual clarity, wording and terminology, levels of difficulty and format, taken from Hernández et al. (2014), and iv) each of the experts ticks the grade on the Likert scale from 1 to 5, choosing the option closest to their qualitative appreciation. To determine the content or construct validity coefficient by experts, we used Cronbach’s alpha.
The formula is as follows:
Where is the Cronbach’s alpha coefficient, K is the item tested,
/is the sum of variances of item i and
/ is the total variance of the sum of items. The following criteria are established for validity and consistency: >0.9 Excellent, <0.81 and 1>; Very high, <0.8 and 0.9>; Fair, <0.71 and 0.80>; Acceptable, <0.6 and 0.7>; Poor, and <0.6 Unacceptable. A value higher than 0.8 is recommended.
Table 4 Questionnaire Survey (instrument No. 1).
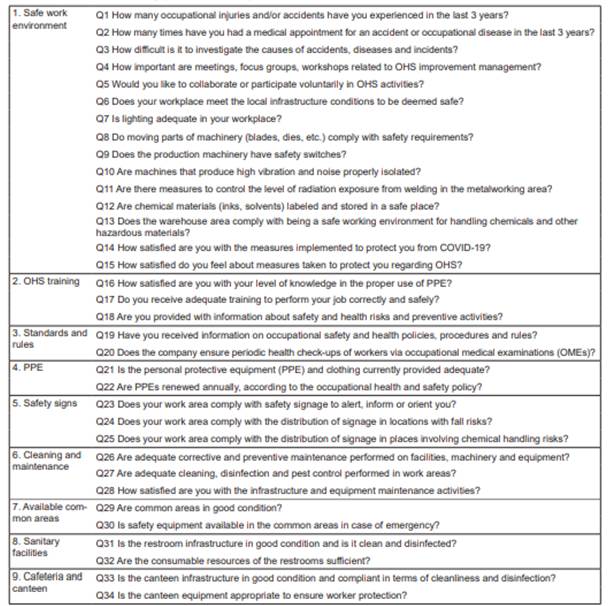
Source: Prepared by the authors based on Brunette (2003).
All data were tabulated and then stored in a database that was distributed per worker for the hypothesis testing of the study. The correlational study used normality and Spearman correlation tests to determine the degree of association between the significant factors of the OHSMS and the OHS management performance indicators (DI, OA, OD and WPI), and to measure the effectiveness of the OHSMS as a whole in identifying risk agents, analyzing the occurrence of unsafe events, classifying exposure to occupational hazards and contributing to the occupational monitoring process conducted by the company. The following statistical hypotheses are used for the normality test: the null hypothesis (H0), which states that the database conforms to a normal distribution, and the alternative hypothesis (H1), which states that the database does not conform to a normal distribution. Upon applying the Kolmogorov-Smirnov (KS) statistical test for a sample n=46 workers, the p values obtained have a significance of less than 0.05, so the H0 is rejected and the H1 is accepted. In other words, the study variables in the database do not fit a normal distribution, for which the non-parametric method Spearman correlation test was used. Consequently, it is possible to analyze the variables without manipulating them and determine the relationship between the independent variables (GS-SSO factors) and the dependent variable (worker protection).
RESULTS
General Descriptive Results
Regarding the OHSMS factors, from the survey conducted in June 2020 to a sample of 46 workers from various areas such as production, warehouse and administrative offices, it is concluded that there it is necessary to strengthen the occupational safety and health culture of workers to ensure their protection. The main results obtained are presented below:
Fifty-three percent of respondents report not having heard about Law No. 29783 (question 19).
Seventy-six percent of respondents report having difficulty in investigating the causes of unsafe events (IP, AT, EO) (question 3).
Sixty-five percent of respondents report that the clothing and PPE are not adequate (question 21).
Sixty-three percent of respondents report that they do not receive adequate feedback on occupational risks and preventive activities (questions 17 and 18).
Ninety-eight percent of respondent consider it important to hold meetings, focus groups and workshops on OHS management improvement (question 4).
Seventy percent of respondent indicate that they do not wish to participate in OHS activities or collaborate as a team member, auditor or researcher (question 5), which contradicts the above.
Regarding worker protection, using the data analysis technique, it is concluded that the existing OHSMS does not guarantee worker protection. The main results obtained are presented below:
A total of 16 dangerous incidents (DI) were reported in one year; however, the survey indicated that there were approximately 61 cases that were not reported to SUNAFIL, because the worker did not suffer major injuries, as shown in Table 5.
A total of 21 occupational accidents (OA) were reported in one year, of which 6 were serious cases. These were: falls of personnel from heights (1), electric shock (1), dislocations (1), hand injuries and cuts (1), exposure to noise and vibrations (1) and sprains (1), as shown in Table 5.
A total of 4 occupational diseases (OD) were reported in one year. These were: hearing loss (1), hernia (1), low back pain (1) and COVID-19 (1). Regarding the latter, one worker contracted the disease in April 2020 outside the company, which did not escalate and was kept under control, as shown in Table 5.
The worker protection perception index (WPI) reached a score of 5283 points (0.67557, i.e. 68% over the target of 7820 points) according to the cumulative result in the surveys, as shown in Table 5.
Validity of the Instrument
The judgment of three experts were considered for content validity, the results of which were as follows: expert 1, 73%; expert 2, 87%; expert 3, 91%. An internal consistency test was also conducted by means of a Cronbach’s Alpha reliability analysis using SPSS statistical software for 46 cases and 13 items, with a total reliability result of 0.896, i.e. 89.6%, which is higher than 80%. Upon measuring reliability per item, the values obtained are higher than 80%, as shown in Table 6. As the experts reported a result higher than 80% and the reliability analysis of the data was higher than 80%, it can be concluded that instrument No. 1 is valid.
Table 6 Reliability Results in SPSS.
Scale Mean (if item deleted) | Scale Variance (if item deleted) | Coefficient (Cronbach’s α) | |
---|---|---|---|
Total Reliability Statistics | 414.717391 | 3639.807246 | 0.896 |
Item 1. Safe work environment | 379.7609 | 3342.319 | 0.889 |
Item 2. Available common areas | 379.7174 | 3121.141 | 0.887 |
Item 3. Cafeteria and canteen | 378.0870 | 3263.592 | 0.891 |
Item 4. Sanitary facilities | 379.1739 | 2766.191 | 0.881 |
Item 5. Personal protective equipment | 384.1739 | 2905.302 | 0.876 |
Item 6. OHS training | 382.7826 | 3173.596 | 0.886 |
Item 7. Cleaning and maintenance | 383.9783 | 2911.888 | 0.874 |
Item 8. Standards and rules | 384.1739 | 2972.636 | 0.880 |
Item 9. Safety signs | 381.6304 | 3182.016 | 0.887 |
Item 10. Dangerous incidents (DI) | 414.3696 | 3626.994 | 0.901 |
Item 11. Occupational accidents (OA) | 414.2609 | 3618.108 | 0.901 |
Item 12. Occupational diseases (OD) | 414.6304 | 3643.794 | 0.902 |
Item 13. Worker protection index (WPI) | 299.8696 | 2140.871 | 0.874 |
Source: Statistical study run in SPSS based on June 2020 data.
Hypothesis Testing
First, the null hypothesis (H0) and the alternative hypothesis (H1) are established. On the one hand, H1 states that there are no OHSMS factors strongly related to worker protection in a graphics and advertising company in Lima-Peru. On the other hand, H1 states that there are OHSMS factors strongly related to worker protection in a graphics and advertising company in Lima-Peru. Afterwards, the error range of the study is established, with a 95% confidence level and 5% alpha error (α) = .05. Then, the statistical method is specified. The KS statistical test indicates that the variables have a non-normal distribution, so Spearman's correlation coefficient should be used. Finally, the p-value is calculated based on the nonparametric correlations and the study variables, using the most significant ones for the analysis. Only those that exceed 50% correlation (correlation between moderate and strong) were considered, as shown in Table 7.
Table 7 Factor Correlation: OSHMS and Worker Protection.
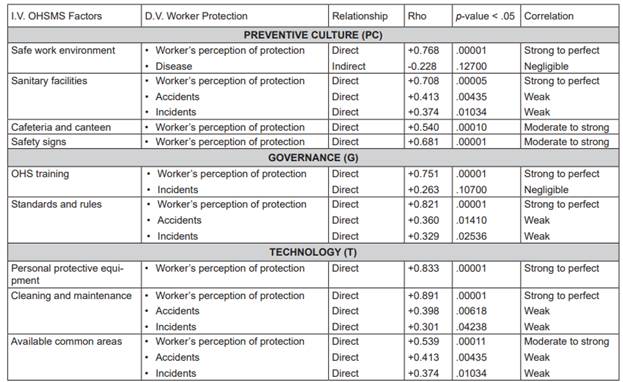
Source: Statistical study run in SPSS based on June 2020 data.
Considering that there are significant relationships (p-value < 0.05), H0 is rejected and H1 is accepted. That is, there are factors of the preventive culture (PC), governance (G), and technology (T) of the OHSMS that are significantly related to worker protection in a graphics and advertising company in Lima-Peru. Figure 1 shows the main relationships.
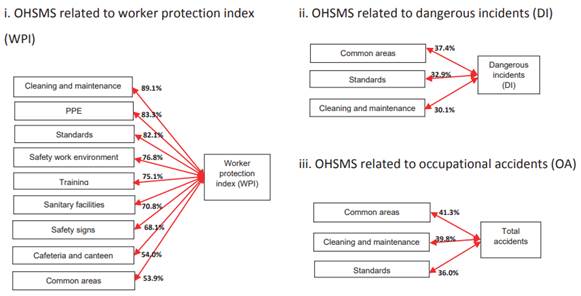
Source: Statistical based on June 2020 data.
Figure 1 Relationship between OHSMS and Worker Protection.
From the above, the following is determined:
There is a correlation of 89.1% between variable worker’s perception of protection and factor cleaning and maintenance (T), thus, there is a strong and perfect correlation between them.
There is a correlation of 83.3% between variable worker’s perception of protection and factor PPE (T), thus, there is a strong and perfect correlation between them.
There is a correlation of 82.1% between variable worker’s perception of protection and factor standards (G), thus, there is a strong and perfect correlation between them.
There is a correlation of 76.8% between variable worker’s perception of protection and factor safe work environment (PC), thus, there is a strong and perfect correlation between them.
There is a correlation of 75.1% between variable worker’s perception of protection and factor OHS training (G), thus, there is a strong and perfect correlation between them.
There is a correlation of 68.1% between variable worker’s perception of protection and factor safety signs (PC), thus, there is a moderate and strong correlation between them.
There is a correlation of 54.0% between variable worker’s perception of protection and factor cafeteria and canteen (PC), thus, there is a moderate and strong correlation between them.
There is a correlation of 53.9% between variable worker’s perception of protection and factor sanitary facilities (PC), thus, there is a moderate and strong correlation between them.
There is a correlation of 53.9% between variable worker’s perception of protection and factor available common areas (T), thus, there is a moderate and strong correlation between them.
DISCUSSION
A worker protection index (IPT) of 68% was determined from the surveys (June 2020) and it was possible to associate it with OSHSMS factors. In relation to preventive culture, a deficiency in the investigation actions regarding TA, OE, PI, as well as the poor monitoring, evaluation and continuous improvement of the OHS, among others, contribute to the poor efficiency of the OHSMS. Therefore, the employer and the company’s workers must join forces to achieve a culture based on OHS and personal well-being, and to avoid occupational hazards and risks. In relation to governance, management’s non-compliance with OSHMS conditions and factors related to policy, review and leadership, as well as the lack of worker commitment and participation, are visible. All this clearly shows the need for greater interdependent interaction between management and workers, increasing the worker’s perception of protection. In relation to technology, a poor OHS training level was identified, as well as the need to revamp materials, machinery and equipment, as the company’s current plans contemplate the use of clean technologies that do not pollute or cause environmental disruptions.
Based on the statistical analysis, it was determined that the OSHMS factors are closely related to worker protection in a graphics and advertising company in Lima-Peru. The hypothesis testing results showed that the worker’s perception of protection is related to the factors of the preventive culture. As a result, the worker’s perception of protection has a correlation of 76.8% with factor safe work environments, 68.1% with factor safety signage, 54.0% with factor cafeteria and canteen, and 70.8% with factor sanitary facilities. Regarding governance factors, the worker’s perception of protection has a correlation of 82.1% with factor standards and rules and a correlation of 75.1% with factor OHS training. Regarding technology factors, the worker’s perception of protection has a correlation of 83.3% with PPE, 89.1% with cleaning and maintenance, and 53.9% with available common areas. On the other hand, it was determined that occupational accidents (OA) have a correlation of 41.3% with factor hygiene facilities, 32.9% with factor standards and rules, 30.1% with factor cleaning and maintenance, and 37.4% with factor available common areas. It was also determined that dangerous incidents (DI) have a correlation of 37.4% with factor sanitary facilities, 32.9% with factor standards and rules, 30.1% with factor cleaning and maintenance, and 37.4% with factor available common areas.
Our findings are related to those of Huancahuari (2009), who considered preventive culture and technology as important factors in his study. The author demonstrated that the growth of the industrial mining sector brings with it an irreversible increase in occupational diseases and that the use of new technologies has given rise to a new condition: stress. For this reason, he considered that the prevention of occupational risks is the responsibility of the company. Regarding governance factors, Zapata (2016) in her study regarding the process of caring for adults, evidences that occupational risks determine disorders of physical and emotional well-being. Therefore, Zapata (2016) states that it is necessary to adopt and strengthen leadership with an institutional commitment to OHS, in accordance with the requirements of the applicable law.
CONCLUSIONS AND RECOMMENDATIONS
The OSHMS factors are closely related to worker protection. Proving that control measures addressing the factors safe work environment, cleanliness and maintenance, and available common areas are the most effective in reducing hazards, mitigating occupational risks, and minimizing unsafe events (DI, OA, OD). Currently, there are no risk control measures in place at the company to ensure worker protection. On the other hand, sometimes it is the workers themselves who engage in unsafe behavior, which may be due to the demands and urgency of the work, lack of training, lack of knowledge of hazards, noncompliance with labor standards, and lack of risk control measures in the workplace.
The OSHMS indicators establish the degree of effectiveness of risk management and prevention to ensure worker protection, which allows establishing an evaluation framework and level of relationship to worker protection compliance. Unsafe events have been investigated in this study on the basis of the severity of the potential risk or harm caused. The results have enabled corrective actions to be taken for OSHMS and risk prevention. According to the company’s last OHS assessment, 27 occupational hazards provoked unsafe events in the last year: 16 DIs, 21 OAs and 4 ODs. In addition, based on the surveys (June 2020), a 68% worker protection index (IPT) was determined and related to significant factors of the OHSMS. Measuring workers’ perceptions from the initial subjective and individual perspective was key to obtaining a true combined rating that will serve as a basis for decision-making and defining future corrective actions to achieve greater worker participation.
Companies should measure the worker’s perception of protection, since the need to include the worker in the OHSMS has been evidenced in this study. This indicator could encourage greater worker participation in risk prevention management; it would also allow a better perception and identification of OHS factors in the workplace, facilitate the analysis of the occurrence of unsafe events, enable a rating of exposure to occupational hazards to be obtained, and serve as a complement to the occupational monitoring conducted by the company.
Preventive culture should be adopted with corporate responsibility and effectively involve the entire chain of command, especially the company's managers and employees, who should work in coordination to encourage and support actions to control occupational risks, as well as to spread and comply with the OSHMS standards.
Personnel training in preventive culture should be reinforced, understanding that prevention is not only about training, but is the starting point to achieve additional mechanisms that lead to a methodology of action to achieve an effective prevention management. Thus, under the regulatory and supervisory eye of the State, employers and workers reach a true preventive culture that is fully assimilated to create a better preventive climate in the company, positively perceived by the workers and that encourages them to take an active part and to continuous improvement.
For a future research, it is recommended to identify the most significant conditioning factors that allow obtaining high-impact results to improve the worker’s perception of protection, as the survey has 34 questions and 9 dimensions. The use of other advanced statistical methods, such as exploratory factor analysis and confirmatory factor analysis, which can be applied to doctoral level research, can provide greater precision.
It is recommended to replicate this study in similar organizations to compare the findings against those of this study, and thereby establish an application methodology that can be adopted as a good practice for the effectiveness of the OHSMS.
ACKNOWLEDGMENTS
To my beloved wife Gladys Leonor Villasante and my children Manuel Josué, Hugo Enrique, Héctor Andrés and Dora Genoveva, my fondest thanks for their unconditional support. Sincerely, with my love.
To my professors of the Postgraduate Unit of the FII of the UNMSM. My gratitude and respect for the support and the guidance I received and continue to receive from them. My special thanks to my advisor PhD Oscar Rafael Tinoco Gómez for his support, guidance and valuable time invested to make this study a reality.
REFERENCES
Álvarez, F., y Faizal, E. (2012). Riesgos laborales. Cómo prevenirlos en el ambiente de trabajo. Bogotá, Colombia: Ediciones de la U. [ Links ]
Atencio, C. (2013). Estudio de accidentes laborales como acción preventiva en una empresa constructora. (Tesis de maestría). Universidad Nacional Mayor de San Marcos, Lima. http:// http://cybertesis.unmsm.edu.pe/handle/20.500.12672/3503 [ Links ]
Brunette, M. J. (julio de 2003). Satisfacción, salud y seguridad ocupacional en el Perú. Economía y Sociedad, (49), 47-52. http://cies.org.pe/sites/default/files/files/otros/economiaysociedad/brunette.pdf [ Links ]
Cortés, J. (2007). Seguridad e Higiene en el Trabajo: Técnicas de Prevención de Riesgos Laborales (9a ed.). Madrid, España: Editorial Tébar S.L. [ Links ]
Gestión. (2016, 30 de junio ). Perú sale ‘jalado’ en sus cifras sobre fatalidad laboral. https://gestion.pe/economia/peru-sale-jalado-cifras-fatalidad-laboral-125466?href=tepuedeinteresar [ Links ]
Gonzáles, A., Mateo, P., y Gonzáles, D. (2010). Manual para prevención de riesgos laborales en las oficinas. Madrid, España: FC Editorial. [ Links ]
Hernández, R., Fernández, C., y Baptista, M. (2014). Metodología de la investigación (6a ed.). México D. F., México: McGraw Hill. [ Links ]
Huancahuari, S. (2009). La Prevención de los riesgos ocupacionales mineros como responsabilidad de la empresa. (Tesis doctoral). Universidad Nacional Mayor de San Marcos, Lima. [ Links ]
Likert, R. (1932). A Technique for Measurement Attitudes . Archives of Psychology, 22(140). https://legacy.voteview.com/pdf/Likert_1932.pdf [ Links ]
Decreto Supremo N.° 015-2005-SA. Reglamento sobre Valores Límite Permisibles para Agentes Químicos en el Ambiente de Trabajo. Diario Oficial El Peruano (2005, 6 de julio). https://www.gob.pe/institucion/minsa/normas-legales/252380-015-2005-sa . [ Links ]
Resolución Ministerial N.° 972-2020-MINSA. Lineamientos para la vigilancia, prevención y control de la salud por exposición al SARS-CoV-2. Diario Oficial El Peruano (2020, 27 de noviembre). https://www.gob.pe/institucion/minsa/normas-legales/1366422-972-2020-minsa [ Links ]
Martínez, R., Tuya, L., Martínez, M., Pérez, A., y Cánovas, A. (2009). El coeficiente de correlación de los rangos de Spearman, caracterización.Revista Habanera de Ciencias Médicas ,8(2). [ Links ]
Ministerio de Trabajo y Promoción del Empleo. (2021, 15 de abril). Estadísticas de Notificaciones de Accidentes de Trabajo, Incidentes Peligrosos y Enfermedades Ocupacionales por Actividad Económica correspondiente al año 2020. https://www.gob.pe/institucion/mtpe/informes-publicaciones/2038032-estadisticas-de-notificaciones-de-accidentes-de-trabajo-incidentes-peligrosos-y-enfermedades-ocupacionales-por-actividad-economica-correspondiente-al-ano-2020 [ Links ]
Mosqueira, H. (2016). Diseño de sistema de gestión de seguridad y salud en el trabajo para industria de plásticos - procomsac - en Chiclayo. (Tesis de maestría). Universidad Nacional de Trujillo, Trujillo. http://dspace.unitru.edu.pe/handle/UNITRU/2966 [ Links ]
Organización Internacional del Trabajo. (12 de abril de 2019). Seguridad y salud en el trabajo. https://www.ilo.org/global/standards/subjects-covered-by-international-labour-standards/occupational-safety-and-health/lang--es/index.htm [ Links ]
Ospina, B., Sandoval, J., Aristizábal, C., y Ramírez, M. (2005). La escala de Likert en la valoración de los conocimientos y las actitudes de los profesionales de enfermería en el cuidado de la salud. Antioquia, 2003. Investigación y Educación en Enfermería, 23(1), 14-29. http://www.scielo.org.co/scielo.php?pid=S0120-53072005000100002&script=sci_abstract&tlng=es [ Links ]
Spearman, C. (1984). Critical Values of the Spearman’s Ranked Correlation Coefficient (rho). En Spearman, Spearman Correlation Coefficient (pág. Table B.19). ZAR. http://webspace.ship.edu/pgmarr/geo441/tables/spearman%20ranked%20correlation%20table.pdf [ Links ]
Ureta, R. (2018). Condiciones de trabajo hospitalario y riesgos laborales en profesionales de enfermería en el Hospital Regional Zacarias Correa Valdivia - Huancavelica. (Tesis doctoral). Universidad Nacional de Huancavelica, Huancavelica. http://repositorio.unh.edu.pe/handle/UNH/2060 [ Links ]
Zapata, I. (2016). Riesgos laborales en el proceso de cuidado a la personal adulta: percepción de las enfermeras. (Tesis doctoral). Universidad Católica Los Ángeles de Chimbote, Chimbote. [ Links ]
Received: November 02, 2021; Accepted: February 14, 2022