INTRODUCCIÓN
El Value Stream Mapping (VSM) es una herramienta visual del enfoque Lean Manufacturing (Paredes, 2017) que muestra el flujo de materiales y de información desde el proveedor hasta el comprador y que, al ser utilizada inicialmente para la descripción del proceso en estudio, es escrita a mano, característica distintiva en el desarrollo del trabajo de campo (Marudhamuthu et al., 2011; Xia y Sun, 2013). Permite reconocer tareas que no brindan «valor añadido», con la intención de ser eliminadas (Rajadell y Sánchez, 2011; Xia y Sun, 2013); además, es una herramienta para la competitividad, pues al analizar la situación presente a través del mapa actual y del mapa futuro y deseado, es posible identificar y eliminar el desperdicio, lo que conlleva a la agilización de procesos clave, reducción de costos y plazos de entrega e incremento de la calidad (Jeong y Yoon, 2016). Un análisis VSM comienza con la gráfica del mapa del estado actual, que se convierte en la línea base de la representación de las operaciones que se vienen llevando a cabo en la organización (Lucherini y Rapaccini, 2017).
Autores como Xia y Sun (2013) consideran que el mapa futuro debe ser diseñado con base en preguntas por niveles de VSM. En el nivel 1 (básico) se tienen las siguientes preguntas: ¿Cuál es el período de fabricación de la empresa de sus productos?, ¿los productos fabricados serán dirigidos a intermediarios o al consumidor final?, ¿en cuáles procedimientos de la cadena de valor es permitido incluir el flujo continuo?, ¿en qué lugar la empresa podrá usar los sistemas de flujo jalado? En el nivel 2 (heijunka), también conocido como nivelación de la producción, se tienen: ¿Qué único punto dentro de la línea de producción será considerado como proceso marcapaso para su programación operativa?, ¿cómo se nivelará la producción en el proceso de marcapasos?, ¿qué incremento regular de trabajo se va a utilizar para la producción y el retiro en el proceso marcapaso? Finalmente, en el nivel 3 (Kaizen o mejora) se cuestiona ¿Qué proceso de mejora será necesario?
En el Perú, las empresas del sector textil y de confecciones exhiben problemas en la gestión a nivel organizacional y también a nivel de calidad; asimismo, la capacidad ociosa de estas empresas es superior al 60%, debido en gran parte a la ausencia de carga de trabajo porque la mayoría de ellas no satisfacen las exigencias de calidad que demanda el mercado global (Arroyo, como se cita en Tinoco et al., 2016, p. 2). Por su parte, Becerra y Carbajal (2019) afirman que en la actualidad las empresas exportadoras del sector textil de prendas de vestir de tejido de punto de algodón, pequeños o medianas, presentan los siguientes inconvenientes: aumento de los costos del proceso (15%) causado por la cantidad de defectos en sus proceso de corte; excesos de 9 días respecto al lead time estándar para la elaboración de una muestra; un lead time elevado de 23 días en comparación a los 15 días que brindan los competidores en otros países; un lead time de 17 días en el proceso de compras, lo que implica 7 días más que el estándar del mercado, y una eficiencia estándar del proceso de desarrollo de producto del 67% a nivel nacional, lo que constituye un problema al ser un porcentaje bajo en comparación con el ideal establecido de 80.44%.
Se han realizado investigaciones que demuestran el uso de la herramienta VSM en empresas pertenecientes al sector textil y de confecciones con el fin de impulsar su competitividad. A nivel internacional, Loos et al. (2016) demuestran su aplicabilidad en el proceso de desarrollo de muestras textiles y concluyen que las personas que laboran en estos entornos no siempre descubren oportunidades de mejoras en sus operaciones; sin embargo, gracias al aporte de la herramienta fue posible diseñar sus secuencias y comprender qué actividades generan o no valor agregado, lo que condujo a desarrollar muestras exclusivas para los clientes y, por ende, a un incremento en el volumen de ventas de la empresa.
En el ámbito nacional, Lucioni (2018), gracias al VSM, identificó la sobreproducción, los productos defectuosos, la acumulación de inventario, el elevado tiempo de espera, el transporte innecesario y los defectos como tipos de desperdicio en una empresa de confección de prendas de exportación. Por su parte, Lecaros (2018), mediante el VSM actual, identificó la sobreproducción, los inventarios, el transporte, los movimientos innecesarios, los tiempos de espera, los procesos innecesarios, los defectos y los recursos humanos mal utilizados como mudas. Esto le permitió comparar las métricas diagnosticadas con las óptimas según la metodología Lean, es decir, el porcentaje mínimo que acepta la industria para considerar una empresa como competitiva. En su investigación, Lecaros (2018) determinó una eficiencia global de equipo (OEE) de 69.30%, que sirvió como punto base, y se fijó el objetivo de 75.00%; determinó el tiempo promedio entre fallas (MTBF) en 109.20 horas, que sirvió como punto base, y fijó el objetivo de 163.80 horas, y, en cuanto al tiempo promedio para reparar (MTTR), el punto base fue de 84.50 minutos y se estableció el objetivo de 59.11 minutos. De la misma manera, el VSM le permitió a Ruíz (2016) mapear la situación actual del área de operaciones de la empresa e identificar el ritmo de la demanda del cliente a través de la implementación del takt time. Sus resultados demostraron que, gracias a la implementación de actividades de valor en relación al indicador de porcentaje de entrega, se obtuvo un incremento de 24.14 % así como una reducción de 26.87 días en el tiempo de no valor agregado. No solo la industria de la confección de prendas de algodón ha sido beneficiada con el uso de VSM, también la de confección de prendas a base de fibras de alpaca para exportación. La aplicación de VSM les permitió a Moore y Norabuena (2019) analizar la cadena actual de suministros, especialmente en lo que respecta al proceso de producción de prendas confeccionadas con palitos de tejer en comunidades altoandinas, y puso en evidencia las ineficiencias existentes en cuanto a la entrega a tiempo del pedido, el escaso flujo de información y la ausencia de parámetros de calidad en la materia prima requerida.
Es menester indicar que resulta necesario e importante demostrar la aplicación de la herramienta VSM para obtener el mapa futuro en una empresa textil y de confección de prendas de exportación, dado que son las empresas que atienden mercados internacionales las que requieren con mayor precisión de productos calidad certificada, con precios competitivos, y rapidez en la entrega de pedidos, de allí que se fundamente el presente trabajo de investigación (Bardales, 2018).
La empresa en estudio se ubica en el departamento de Lima, Perú, y su principal actividad económica la producción y confección de polos de algodón y vestidos estampados para hombres y mujeres, tanto para niños como para adultos. Debido al incremento de los costos de insumos y a la disminución progresiva de la producción a causa de una gestión deficiente, la empresa se vio en la necesidad de utilizar herramientas de mejora continua para detectar problemas en el flujo de producción e identificar oportunidades de mejora para incrementar su competitividad. Por lo mencionado, el objetivo de este trabajo de investigación se basa en el desarrollo e implementación de un método de aplicación de la herramienta VSM para aumentar la competitividad en la empresa en estudio. La hipótesis que se pretende contrastar es que existe una diferencia significativa en la competitividad de la empresa antes y después de la implementación del método de aplicación de la herramienta VSM en la Empresa Textil y de Confecciones.
El propósito de este artículo es ser relevante y útil para la comunidad científica, por lo que se presenta como factor innovador el desarrollo de un método de aplicación de VSM que servirá como guía para implementar esta famosa herramienta en la industria textil y mejorar la competitividad de las empresas peruanas. A través de los resultados y la contrastación de hipótesis, se demostrará la validez práctica del método y abrirá las puertas a futuras investigaciones para aplicarlo en contextos similares.
Lean Manufacturing
El Lean Manufacturing es un paradigma de organización y de manejo de la cadena de suministro que incluye a personas, materiales, máquinas y métodos. Sus principales funciones son mejorar la calidad y la eficiencia mediante la eliminación continua del despilfarro e incrementar la satisfacción del cliente (Socconini, 2019). La metodología Lean Manufacturing es ideal para contextos en los que la fabricación de los productos se realiza mediante procesos discretos y repetitivos, ya sea para volúmenes pequeños, medianos o grandes (Soler, 2015). Se debe tener en cuenta ciertos factores para su correcta aplicación, como por ejemplo disponer de un equipo bien adaptado y el conocimiento de recopilación y análisis de información (Kafuku, 2019).
Cadena de suministro
Se define como un sistema de información que involucra personas, labores y bienes, y cuya relación permite que un producto llegue del productor al consumidor. Abarca también la relación entre la gestión de proveedores, la compra de materias primas, la fabricación y repartición del producto final. Sin embargo, la cadena de suministro no debe limitarse a los eslabones que la componen, sino que debe caracterizarse por sus atributos claves de funcionamiento (Santander et al., 2014).
Mapeo de flujo de valor (VSM)
El VSM es una herramienta conceptual que esquematiza la cadena de valor, dando énfasis a la circulación de materiales e información, los cuales parten del proveedor y se dirigen al cliente (Jimmerson, 2017). El objetivo de esta herramienta es expresar de manera sencilla las actividades productivas para identificar la cadena de valor, detectar de manera global dónde hay tareas que no agregan valor a la empresa, e identificar los procesos en los que se presentan cuantiosos desperdicios (Rohac y Januska, 2015).
Método de aplicación de la herramienta VSM en la industria textil
El método expuesto en esta investigación se basa en la aplicación de la herramienta VSM para mejorar la competitividad de una empresa textil y de confección. En la Figura 1, se ilustra el método planteado.
METODOLOGÍA
La investigación se encuentra inserta dentro del estudio de caso. Yin, McCutcheon y Meredith, citados por Jeong y Yoon (2016), consideran esta metodología apropiada si se presentan tres condiciones: la primera, relacionada con el análisis de una situación en particular dentro de su contexto originario o natural; la segunda, relacionada con la poca o nula capacidad de manipulación del evento por parte del investigador, y, la tercera, relacionada con la pregunta ¿cómo? La pregunta en el presente trabajo fue ¿Cómo se aplica el VSM para obtener el mapa futuro de la organización en estudio?
Para Amador y García (2019), el VSM es una metodología para la aplicación del mapeo de la cadena de valor, que cuenta con los pasos siguientes:
Paso 1: Elección de un área productiva crítica
Paso 2: Elaboración del estado actual del mapa
2.1. Inspección documentaria existente
2.2. Reconocimiento de procesos principales
2.3. Definir data inexistente que debe recopilarse
2.4. Recolectar la información
Paso 3: Análisis del mapa del estado actual
Paso 4: Mapa del estado futuro
4.1. Cálculo del takt time
4.2. Determinar el tiempo deseado
4.3. Ejecución de herramientas de mejora
La recolección de los datos se realizó en primer lugar a través de entrevistas personales a un total de 16 responsables distribuidos en las áreas de Tendido, Corte, Costura, Bordado, Estampado, Acabado y Detector de Metal; se utilizó la representación escrita manual para elaborar el mapa actual con el fin de no perjudicar el desarrollo de las actividades operativas de la organización. En este tipo de estudios de caso es usual apelar al método de triangulación de sujetos (Díaz et al., 2011) para asegurar la calidad de los datos y resultados obtenidos, por lo que se contrastaron los resultados obtenidos de las entrevistas personales realizadas al personal encargado de cada una de las áreas involucradas en el estudio.
RESULTADOS
Fase 1: Evaluación externa de la empresa
1. Actividad económica
La empresa objeto de estudio está especializada en la fabricación de prendas en tejido de punto; posee además dos plantas especializadas en tejido y tintura localizadas en Perú, cuyos productos se fabrican y exportan a mercados como Estados Unidos y Brasil.
2. Productos principales
Polos camiseros sport elegante de algodón para varón y dama
Vestidos para dama en tela estampada y otros productos para niños
3. Definir a los proveedores
Proveedor de avíos
La solicitud se realiza por correo electrónico. En promedio, se necesitan 6 botones decorativos por prenda, con una merma del 2%. La entrega se realiza cada 2 semanas.
Proveedor de telas estampadas
La solicitud se realiza por correo electrónico. Consumo por tallas XS/1 S/2 M/3 L/1. La entrega se realiza cada 3 días.
Proveedor de tela de punto de la Empresa Textil y de Confecciones planta 1 Los Olivos
La solicitud se realiza por correo electrónico. Consumo por tallas S/3 M/2 L/2 XL/2. La entrega se realiza cada 2 días.
4. Clientes principales
Sus clientes directos son reconocidas tiendas por departamento como Black Denim, Lilly Pulitzer, Infinity, Polo Ralph Lauren y Tommy Bahama. Los clientes más recurrentes tienden a realizar pedidos semanalmente y las entregas se realizan cada 3 semanas por embarque.
5. Definir exigencias del cliente
El cliente de polos de determinada marca exige que sus prendas lleven un sticker detector de metal que indique que sus prendas son de alta calidad y no contienen ningún metal dañino.
Confecciones Perú exige a sus clientes realizar sus pedidos con 6 semanas de antelación.
En promedio, se fabrica un total de 12 000 prendas al mes por cada bloque: 4000 prendas de moda/mes, 6000 t-shirt básico/mes y 2000 prendas de tela estampada/mes.
Fase 2: Evaluación interna de la empresa
1. Calcular la producción diaria
Cantidad de unidades que puede fabricar la empresa durante un día de jornada laboral
La representación gráfica del flujo de información se muestra en la Figura 2, que comprende los clientes, el Área de Control de Producción de la empresa, y los proveedores.
2. Calcular el tiempo disponible y el takt time
La empresa trabaja 25 días al mes, 2 turnos en todas las áreas, cada turno es de 8.5 horas más horas extras si es necesario, 2 descansos de 10 minutos por turno y la hora de almuerzo es sin pago.
Tiempo disponible por turno = (8.5 h * 60 min − 2 * 20 min) * 60 s = 28 200 s
3. Recolectar información y mapear el flujo de los procesos con VSM
Área de Tendido
Equipo manual, 2 operarios por mesa de tendido (4 mesas), tiempo de ciclo igual a 59.46 s, tiempo de cambio entre tallas igual a 2 min y fiabilidad de 80%. Inventario antes del proceso: 3 días (retraso del proveedor), 1 día de reposo de la tela y el inventario después del proceso: 0.5 días.
Área de Corte
Equipo manual, 1 operario por máquina, 3 módulos de trabajo, tiempo de ciclo igual a 49.20 s, tiempo de cambio entre tallas igual a 5 min y fiabilidad de 100%. Inventario después del proceso de 1 día para costura.
Se observa la representación gráfica de las áreas de Tendido y Corte con sus respectivos inventarios en proceso en la Figura 3.
Área de Costura
Equipo manual, 1 operario por operación (promedio = 16), tiempo de ciclo igual a 616.86 s/prenda, tiempo de cambio entre tallas igual a 1 min y fiabilidad de 80%. Inventario después del proceso: 1 semana.
Área de Bordado
Equipo manual, 1 operario, tiempo de ciclo igual a 73.08 s/prenda, tiempo de cambio entre tallas igual a 60 s y fiabilidad de 100%. Inventario después del proceso: 3500 prendas básicas y 500 prendas moda.
Área de Estampado
Equipo manual, 3 operarios por máquina (2 máquinas), tiempo de ciclo igual a 64.68 s/prenda, cambio entre tallas igual a 60 s y fiabilidad de 100%. Inventario después del proceso: 4500 prendas básicas y 500 de moda.
La representación gráfica de las áreas de Costura, Bordado y Estampado con sus respectivos inventarios en proceso se muestran en la Figura 4.
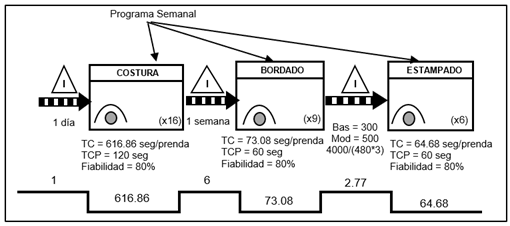
Fuente: Elaboración propia.
Figura 4 Representación gráfica de las áreas de Costura, Bordado y Estampado.
Área de Acabados
Equipo manual, 9 operarios (3 líneas de producción), tiempo de ciclo igual a 616.86 s/prenda, cambio entre tallas igual a 60 s, fiabilidad de 100%. Inventario después del proceso: 3500 básicos (área detectora de metal) y 2000 de moda (área de despacho).
Área de Detector de Metal
Necesita 1 operario, tiempo de ciclo igual a 2.76 s/prenda, tiempo de cambio entre tallas: ninguno, fiabilidad de 100% y, una vez en el área de Detector de Metal, los camiones van cada 3 semanas al puerto de embarque.
Despacho
Necesita 3 operarios, tiempo de ciclo igual a 30 s/prenda y, una vez en expedición, los camiones van cada 3 semanas al puerto para el embarque.
La representación gráfica de las áreas de Acabados y Despacho con sus respectivos inventarios en proceso se muestra en la Figura 5.
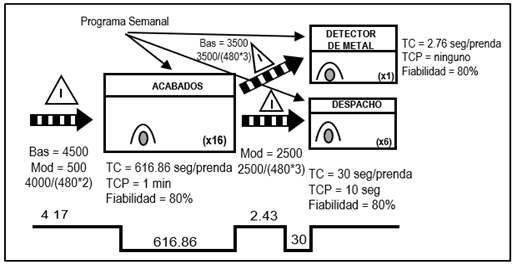
Fuente: Elaboración propia.
Figura 5 Representación gráfica de las áreas de Acabados y Despacho (proceso final).
Las representaciones gráficas anteriores (Figuras 2, 3, 4 y 5) permiten la elaboración del VSM actual de la Empresa Textil y de Confecciones (Figura 6).
Fase 3: Elaboración de VSM futuro
Pregunta 1: ¿Cuál es el ciclo de producción de la Empresa Textil y de Confecciones para sus productos?
Tiempo de trabajo disponible del turno = (8.5 h * 60 min * 60 s) = 30 600 segundos
Tiempo que no se dedica al trabajo = (20 min/turno * 60 s) * 2 turnos = 2400 segundos
Tiempo disponible = 30 6000 s − 2400 s = 28 200 segundos
Demanda del cliente por turno = (12 000/mes ÷ 25 días)/2 turnos = 240 unidades/turno
Ciclo de producción = 28 200 s ÷ 240 unidades = 117.5 s/unidad
Pregunta 2: ¿Debería la Empresa Textil y de Confecciones guardar sus soportes en sus supermercados productos finiquitados o producirlo directamente para envío?
La Empresa Textil y de Confecciones cuenta con una fiabilidad de 80%, por lo que un inventario de productos terminados es innecesario. Si hay supermercado, debe pasar de Costura a Acabados, se debe eliminar la inspección y realizarse una evaluación de control de calidad.
En la Figura 7, se representa gráficamente el tiempo de transporte y la cantidad de prendas entre los procesos de acabados y despacho, así como vaporizado y control de calidad.
Pregunta 3: ¿En qué procesos de la cadena de valor puede la Empresa Textil y de Confecciones introducir el flujo continuo?
Como máximo debería haber 9 operarios en el ciclo de producción, pero no es así. Es posible fusionar operaciones compatibles y luego convertirlas en células para mejorar su tiempo de ciclo. En la Figura 8, se observa el histograma de los tiempos de ciclo de cada proceso y su comparación con el takt time; además, en la Tabla 1 se observan procesos con tiempos de ciclo parecidos, tales como «tendido» y «corte», «bordado» y «estampado».
Tabla 1 Tiempos en cada máquina.
Ítem | Máquina | Tiempo |
---|---|---|
1 | Tendido | 59.46 s |
2 | Corte | 49.2 s |
3 | Costura | 616.86 s |
4 | Bordado | 73.08 s |
5 | Estampado | 68.64 s |
6 | Acabados | 162.84 s |
7 | Despacho | 30 s |
8 | Takt time | 117.5 s |
Fuente: Elaboración propia.
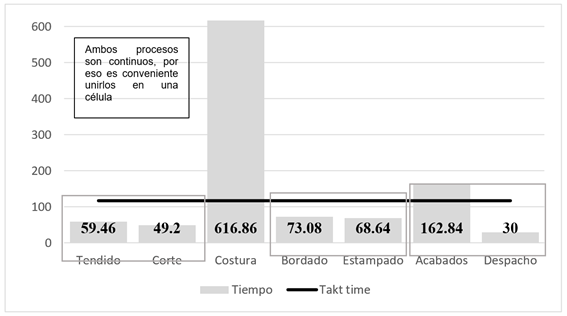
Fuente: Elaboración propia.
Los procesos se unen para equilibrar el número de operarios, puesto que hay operarios con tiempo muerto.
Figura 8 Histograma de los tiempos de ciclo de cada proceso y su comparación con el takt time.
Después de observar que los tiempos de ciclo de «tendido» y «corte», y «bordado» y «estampado» son similares, se aplicará la herramienta de célula en U y L respectivamente para unir los procesos en flujo continuo, lo que permite eliminar los inventarios en proceso y reducir el número de operarios (Figura 9).
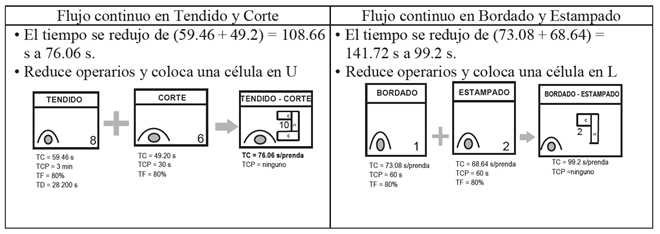
Fuente: Elaboración propia.
Figura 9 Mejoras en el flujo continuo en las áreas de Tendido y Corte y Bordado y Estampado.
Capacitando al personal del Área de Despacho, se logró que solo una persona esté a cargo y que otra pasara al Área de Acabados, donde se requiere más atención para doblar las prendas (Figura 10).
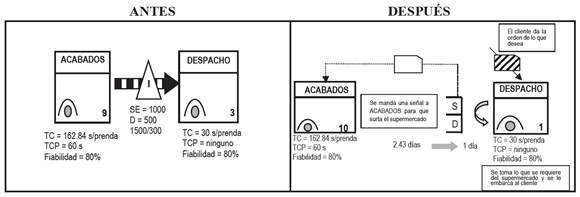
Fuente: Elaboración propia.
Figura 10 Mejoras en el flujo continuo de inventario en las áreas de Acabados y Despacho.
Pregunta 4: ¿En dónde tendrá que usar la Empresa Textil y de Confecciones los sistemas de flujo jalado con supermercados?
Se necesitará un supermercado para los polos de moda, básicos y estampados, ya que tienen gran fluctuación de venta durante el año; además, es necesario controlar la producción de polos de moda, básicos y estampados para varones y mujeres mediante su extracción del supermercado (flujo jalado).
Sugerencia
Anaqueles adecuados con capacidad suficiente y distribuidos de acuerdo al modelo, talla y color
Incrementar la frecuencia del cambio de modelo y talla (manufactura lean)
Prendas de moda = 6000/25 = 240 pda/día
Prendas estilo básico = 4000/25 = 160 pda/día
Prendas de tela estampada = 2000/25 = 80 pda/día
Tamaño de separaciones entre anaqueles
Cada espacio del anaquel tendrá una capacidad para una hora de trabajo o 33 prendas. Llevarán tarjeta Kanban de retiro.
El operario que va a transportar las 33 prendas/hora de corte a la célula de costura dejará su tarjeta Kanban, que será recibida por el operario del área de corte, quien sabrá que deberá producir otro lote de 33 prendas (Figura 11).
Pregunta 5: ¿Qué punto preciso de la cadena de producción va a elegir la Empresa Textil y de Confecciones (como proceso marcapaso) para su programación?
Los procesos anteriores al proceso marcapaso deben estar en flujo continuo, para la Empresa Textil y de Confecciones el punto de programación es la célula de Bordado-Estampado. Es imposible programar antes, pues los tiempos de ciclo de las áreas de Corte y Costura presentan una diferencia considerable.
Pregunta 6: ¿Cómo podría la Empresa Textil y de Confecciones nivelar la combinación de productos en el proceso marcapaso?
En la célula de Bordado-Estampado, la combinación de prendas que se produce durante un turno se nivela a través del flujo jalado de las prendas que se hayan retirado sin tener que mantener tanto inventario en el supermercado de prendas de Teñido-Corte (Figura 12).
Pitch = takt time × cantidad por paquete (1 paquete = 10 prendas).
Pitch = 117.5 × 10 = 1175 s = 19 min 35 s
Pregunta 7: ¿Qué incremento regular de trabajo va a utilizar la Empresa Textil y de Confecciones para la producción y el retiro en el proceso marcapaso?
En la Empresa Textil y de Confecciones se produce un incremento del trabajo en el módulo Bordado-Estampado: 117.5 segundos del tiempo de ciclo de producción × 33 prendas = 64.63 minutos. Este es el paso de la producción de prendas que corresponde a una tarjeta por cada 33 prendas. La Tabla 2, denominada caja de nivelación, muestra la programación de los turnos de producción.
Tabla 2 Caja de nivelación de los turnos de producción.
Turno 1 | 08:00 | 09:00 | 10:00 | 11:00 | 12:00 | 01:00 |
Turno 2 | 03:00 | 04:00 | 05:00 | 06:00 | 07:00 | 08:00 |
Prendas de moda | M | M | ||||
Prendas estilo básico | B | B | ||||
Prendas de tela estampada | E | E |
Fuente: Elaboración propia.
Pregunta 8: ¿Qué mejoras afines a los procesos se necesitarán para que el flujo de la cadena de valor de la Empresa Textil y de Confecciones sea el que describe el mapa del estado futuro?
A continuación, se listan las mejoras afines necesarias:
Reducir a cero el tiempo de cambio de productos en el Área de Corte y bajar a cero el tamaño de lote para llegar a la meta de «cada pieza, cada turno».
Eliminar el tiempo (10 min) que se necesita para el cambio entre los tipos de prenda (básico, moda y estampada) para lograr un flujo continuo.
Mejorar el tiempo de producción en el proceso de costura implementando 5’S.
Eliminar el desperdicio de la célula de bordado y estampado para reducir la duración de la tarea a 99.2 segundos o menos a través de la aplicación de 5’S.
Estos elementos se encuentran en el mapa futuro con el ícono de Kaizen en la Figura 13.
Los resultados de la comparación entre el estado actual y el futuro son favorables gracias a la nivelación de producción en las células de Tendido-Corte, Bordado-Estampado y Acabado-Despacho. La empresa puede reducir aún más la cantidad de prendas en proceso y terminadas almacenadas en los supermercados. Sus condiciones ponen de manifiesto la importancia de la fiabilidad de los equipos y la capacidad de predecir la producción en función del ciclo. En la Tabla 3, se muestra el antes, con producción en flujo nivelado, y con producción con nivelación de la rotación total de inventarios y se observa una reducción de los plazos de entrega y un incremento de la rotación total del inventario.
Tabla 3 Reducción de los plazos de entrega e incremento de la rotación total anual del inventario.
Rollos | Tendido y Corte | Costura | Bordado y Estampado | Detector de Metales | Plazo de entrega de producción | Rotación total del inventario | |
Antes | 4 días | 1.5 días | 6 días | 6.94 días | 4.1 días | 2.76 días | 14 días |
Producción en flujo continuo | 3 días | 1 días | 4 días | 3 días | 2 días | 1.9 días | 20 días |
Producción con nivelación | 2 días | 0.5 días | 2.5 días | 1.5 días | 1 días | 1.5 días | 33 días |
Fuente: Elaboración propia.
Rotación total del inventario = Días totales por año / Plazo de entrega de producción
Días totales por año: 25 días × 12 = 300
Antes: 300/20.87 = 14.37 <> 14
Producción con flujo continuo: 300/14.9 = 20.13 <> 20
Producción con flujo nivelado: 300/9 = 33.33 <> 33
CONTRASTACIÓN DE HIPÓTESIS
En el presente estudio se planteó la pregunta de investigación: ¿El método de aplicación de VSM es capaz de aumentar la competitividad en una empresa textil y de confección? A partir de esa interrogante, se planteó hipótesis general que se muestra a continuación:
Ho = No existe una diferencia significativa en la competitividad antes y después de la implementación del método de aplicación de VSM.
Ha = Existe una diferencia significativa en la competitividad antes y después de la implementación del método de aplicación de VSM.
Inicialmente, para verificar la distribución de los datos, se realizó la prueba de normalidad de Anderson-Darling por medio del software MINITAB 2018 con la que se obtuvo un valor p de 0.161. Teniendo en cuenta que el coeficiente de significancia era 0.05, se concluyó que los datos seguían una distribución normal.
Posteriormente, se realizó la prueba t de Student para contrastar la hipótesis planteada con la que se obtuvo un valor t de 8.31 y un valor p de 0.0000. Dado que el valor t es significativamente mayor que el valor p, se rechaza la Ho y se acepta la Ha, por lo que se puede afirmar que existe una diferencia significativa en la competitividad antes y después de la implementación del método de aplicación de VSM.
DISCUSIÓN
De acuerdo a los resultados obtenidos a través de la aplicación del VSM, se obtuvo un takt time de 117.5 s/prenda, es decir, ese es el tiempo que la compañía deberá emplear para producir el producto y satisfacer al cliente. En cuanto al tiempo transcurrido desde que se inicia un proceso de producción hasta que se completa (lead time), en el mapa actual se obtiene un resultado de 20.87 días, pero en el mapa futuro este se redujo hasta 16.7 días, es decir, ese es el tiempo que tardará el producto en salir y ser entregado al cliente. Asimismo, en el mapa actual se obtiene un tiempo de valor agregado (TVA) de 1060.08 segundos, entendiéndose como el tiempo en que el producto tarda en fabricarse o en transformarse hasta conseguir el resultado final. Estos resultados son concordantes con los obtenidos por Lucioni (2018), Lecaros (2018) y Ruíz (2016) sobre la utilidad de la herramienta VSM como instrumento de diagnóstico que, al determinar los desperdicios en los procesos operativos de empresas textiles y confecciones, les permite, junto con otras prácticas de la metodología Lean, incrementar su productividad. Asimismo, ratifica lo vertido por Rajadell y Sánchez (2011) y Xia y Sun (2013), quienes sostienen que, al ser una herramienta visual, identifica las actividades que no aportan valor añadido a la organización.
CONCLUSIONES
Este estudio presenta un método de aplicación práctica de Value Stream Mapping como una herramienta para la competitividad en una Empresa Textil y de Confecciones de prendas de exportación, para lo que se hace uso de la metodología del caso único con el fin de obtener un análisis detallado sobre el tema en estudio. Mediante la recopilación de datos e información sobre la empresa con el fin de obtener el mapa de flujo de valor, fue posible detectar las oportunidades de mejora en una empresa como esta. Aplicando la gestión diaria operativa, se identificaron los problemas presentes durante el día con la ayuda de tableros comparativos entre procedimientos estándar y reales. Esta medida benefició considerablemente el flujo productivo, pues permitió reducir desperdicios y establecer un flujo continuo del producto. Los factores mencionados se tradujeron en una disminución de tiempos y desperdicios, lo que generó una reducción de costos y un incremento de la productividad y la competitividad en los procesos de la organización.