Serviços Personalizados
Journal
Artigo
Indicadores
-
Citado por SciELO
Links relacionados
-
Similares em SciELO
Compartilhar
Industrial Data
versão impressa ISSN 1560-9146versão On-line ISSN 1810-9993
Ind. data vol.26 no.1 Lima jan./jun. 2023
http://dx.doi.org/10.15381/idata.v26i1.23828
Production and Management
Ludic Experience Using Lean Manufacturing Standard Operating Sheet Tool to Improve the Teaching and Learning of Standardized Work
1PhD in Education from Universidad San Martín de Porres (Lima, Perú). Master’s degree in Industrial Engineering from Universidade Federal de Santa Catarina (Florianópolis, Brazil). Currently working as an independent consultant. E-mail: flor.tapia@urp.edu.pe
This study proposes the application of a ludic and practical experience, which includes the use of the standard operation sheet tool for the purpose of improving the teaching and learning of standardized work. In this way, the study helps to solve the problem of the communication of standards in companies, and improve the capabilities and competences of Industrial Engineering students.
The study is applied and relational. It was aimed at comparing the difference in the assembly cycle time of a pegboard before and after teaching and learning the operation sheet standard, by means of a parametric repeated measures test, in order to verify if the assembly cycle time decreases.
The results obtained confirmed the research hypothesis, reduced the variability of communication of the standard and improved the integration of teamwork.
Keywords: Standard operating sheet; standardized work; lean manufacturing; games
INTRODUCTION
What thought is triggered in the brain when we talk about standardization? Perhaps it evokes industrial engineers implementing new rules on how to achieve a compliant product or process. Is there something wrong with that thought? That will depend on how that rule was born and what is the concept of standard and standardization.
According to Rother (2010), a standard is a description of how a process should operate. It is a rule that injects order and provides clear elements on how a product or process should be made in order to minimize waste and/or maximize added value.
Standards should not be promulgated by decree, imposed, thoughtless, speculative, or become a dead letter. As Liker and Meier (2006) state, standards should also not be used as a whip to flog employees for poor performance or as a bait to exceed that pattern.
According to the Lean Enterprise Institute (2014, p. 82), standards should be the result of standardized work, that is to say, of the establishment of precise procedures for each operator working in a production process. These procedures should be designed based on three elements: (1) the takt time, (2) the exact sequence of work performed by the operators within the takt time, and (3) the standard inventory including the items needed on the machines to keep the process running smoothly.
Standard operating procedures (also called job aids), as well as standard operating sheets, are often used to establish standardized work.
Job aids are conventional tools that set out sequentially and orderly the set of instructions on how each activity should be carried out at work. Meanwhile, standard operating sheets are tools that promote the design of processes so that employees know what they must do, what order or sequence they must follow, how they must proceed, and why the tasks must be performed the way they have been defined. Standard operating sheets are advantageous tools because they
[exploit visual management and highlight sui generis skills required to perform work safely, compliantly, and efficiently] (Lean Enterprise Institute, 2014, p. 86).explotan la gestión visual y destacan habilidades sui generis requeridas para realizar el trabajo de manera segura, conforme y eficiente
The Productivity Press Development Team (2002) states that
[problems frequently arise in companies because the information in standard operating procedures is obscure, incomplete, contains technical and complex terms that are not useful to the operator] (p.16).frecuentemente en las empresas surgen problemas porque la información en los procedimientos operativos estándar es oscura, incompleta, contiene términos técnicos y complejos que no resultan de utilidad para el operario
Likewise, Spear and Bowen (1999) warn that if activities are poorly specified and stated, that is, if the sequence, content, duration and outcome of operations are not well formulated, if supplier-customer processes are unclear and if product routings are inaccurate, then a series of problems will arise in the company as a result of a poorly projection and/or standardization.
Furthermore, when the communication of standards and procedures is not precise, work relationships based on trust are also affected as it would be difficult to empower employees with confidence as they may not perform equally and would be misaligned on the stated purpose, which would also undermine leadership management in a company.
But who should create or improve standardized work? Shimizu (2004) found that at Toyota, 10% of productivity improvements and process standardization falls on production operators through quality control circles. The remaining 90% comes from industrial engineers, production supervisors and improvement team leaders as part of their duties. However, at Toyota, these groups are not divorced. According to Rother (2010),
[the operator as well as the industrial engineers and team leaders have incentives to work together on process improvement] (p. 156). Therefore, it is healthy for industrial engineers to collect suggestions from operators when designing or improving standards.tanto el operario, cuanto los ingenieros industriales y líderes de equipos tienen incentivos para trabajar juntos en la mejora de los procesos
Fleury et al. (2008) state that industrial engineering dates back to more than a century ago and arose through the standardization or economic rationalization of production systems. However, from the first Taylorist systems to the present day, companies have faced dramatic changes. According to De Oliveira et al. (2013)
[knowing is not enough these days. Instead, expert professionals are required to possess skills, knowledge and attributes that make them capable of facing current demands and projecting solutions to multidisciplinary and complex problems] (p. 21).hoy no es suficiente saber; antes bien, se requieren profesionales expertos con competencias, saberes y atributos que los hagan capaces de enfrentar las exigencias actuales y proyectar soluciones de problemas multidisciplinarios y complejos
Isao Kato, a Toyota official, emphasizes that
[Developing something requires developing people. You cannot separate the development of the company system from the development of people] (2006, as cited in Liker and Meier, 2007, p. 121). Liker and Meier (2007) underline that the simple implementation of standards, without the appropriate development of the capabilities and skills of the people who develop those standards, generates limited benefits, specifically regarding standardized work.Desarrollar algo, exige desarrollar personas. Usted no consigue separar el desarrollo del sistema empresa, del desarrollo de las personas
Thus, there is consensus on the need for professionals highly capable of standardizing, maintaining and perfecting business processes. Therefore, professors should make every effort to ensure that future industrial engineers achieve high levels of competence in designing, developing, and maintaining standardized work.
The contribution of this article is to propose a ludic method that incorporates the use of the standard operating sheet tool to improve the teaching and learning of standardized work. The proposed game will help both undergraduate and graduate schools of Industrial Engineering and manufacturing organizations in the creation, maintenance and improvement of standards and their communication.
The contribution of this article is innovative because it enhances the capabilities and competencies of industrial engineering students and/or company employees by means of a game. This methodology provides students with the opportunity to learn and apply the concepts of standard and standardization in real time and in a fun, spontaneous, and motivational manner. As a result, the knowledge construction is more meaningful.
Problem, Objective and Hypothesis
Based on the above and according to The Productivity Press Development Team (2002), there is evidence of problems in the communication of standards and standardized work as the available tools for this task (such as job aids and standard operating sheets) do not provide the same level of added value in terms of information transmission. This motivated this investigation, which aims to propose a game to assemble a pegboard before and after teaching and learning the standard operating sheet, and to evaluate whether the teaching and learning of this tool reduces the pegboard assembly cycle time.
The research hypothesis is that the average of the differences in the cycle time of the assembly of the pegboard (before and after the teaching and learning of the standard operating sheet) is greater than zero.
Background
The background of this study are distributed into two categories. On the one hand, there is a great diversity of research that has promoted the application of standardized work and has shown positive results in manufacturing companies. On the other hand, there are studies that use games as didactic strategies to enhance the learning experience of industrial engineering in class.
Bragança and Costa (2015) stand out within the first group and point out in their study that they managed to do more with less in the company where they implemented work standardization, as they obtained an increase in flexibility and productivity on the plant floor without the need for high investments.
Through the standardization of work, Fazinga and Saffaro (2012) managed to disseminate a common goal for all those involved in the operating processes. There were no autonomous actions by the operators because all replicated the sequence of operations stated in the standard operating sheet, which reduced variability in the civil construction processes.
Pereira et al. (2016) stated that standard operating sheets are essential but can pose problems if not effectively managed and controlled within organizations. The authors conducted a study where they developed and reconfigured the standardization of work in a company, which had positive impacts on product quality and productivity.
Through the standardization of work, De Freitas and Da Silva (2017) managed to reduce variability and improve the process quality of a manufacturing cell. They highlight the importance of integrating people for a successful consolidation of the standard, as well as the impact on the satisfaction of the operators resulting from their participation in the design of the standards and the simplification in their training.
In a more recent study, Dos Santos et al. (2021) reported that the activities within a company used to be disorganized, resulting in frequent bottlenecks in the receiving and supply area. However, after the implementation of the standard operating sheet, there was improved harmony in operations, increased stability in the assembly line, enhanced throughput, reduced accumulated lead times, and higher process quality.
Regarding the second group of information consulted, Possebon et al. (2012) should be referenced. They successfully developed a teaching and learning process for the standard operating sheet using a group dynamic based on a game developed in class. This approach enabled production engineers to better assimilate the theoretical concepts presented during class.
Có et al. (2008) also proposed a teaching and learning strategy based on a ludic experience with cards and on constructivist epistemology with the purpose of improving the competences of production engineers regarding planning tools based on the lean manufacturing model. Students were able to formulate more efficient plans that improved the fulfillment order significantly.
The studies on improving the teaching and learning of industrial engineers is not limited to the tools of the lean model. Tapia (2014) develops a company game to improve the teaching and learning of operations planning under the theory of constraints model. In his conclusions he states that games are tools that facilitate the learning process, which contributes to improved understanding of abstract issues.
Justification
Proposing a game to improve the teaching and learning of standardized work is justified due to the general use of this tool in education. Games allow people to exercise in various hard and soft skills required for their integral development. Games are simulators that replicate real scenarios with the purpose of practicing, strengthening, maturing, learning, or acquiring new knowledge.
Aguilar et al. (2018) argue that the purpose of games is to achieve academic quality and generate clear standards that allow establishing indicators to evaluate the desired competence profile of a professional.
The justification for focusing on enhancing the technical competencies of industrial engineers in relation to standardized work is based on Masaaki (1986), who states that without standards and standardization, it is impossible to initiate continuous improvement processes within a company.
That is, an anomalous situation cannot be detected without prior standardization. Therefore, standards and standardization are essential to make non-standard conditions visible, so that preventive and/or corrective actions can be quickly triggered in order to standardize them and reduce waste.
METHODOLOGY
Type, Method and Design of the Research
This work is of an applied type, since, as pointed out by Hernández et al. (2014), the emphasis of the study is to propose a practical solution to the problem posed. The level of the research is relational, that is, it seeks to show probabilistic dependence between events, since the statistical objective is to compare two measures, one before and the other after the teaching of the standard operating sheet. The design is pre-experimental because it works with a single group, where the intervention is applied (pre and posttest). According to Arnau and Bono (2008), the study also qualifies as longitudinal, of repeated measures on the same group, since its main characteristic is the sequential observation of the same dependent variable according to different treatments.
Inventory items required for implementing the pegboard assembly game
To run the game proposed, the items listed and shown in Figure 1 are required.
1 asymmetrical 20 × 23 cm wooden board with 42 holes.
50 wooden sticks 7 cm high and 0.5 cm in diameter. It should be noted that only 42 wooden sticks are required to assemble the pegboard. However, there is a restriction in the game: if a stick falls out during the assembly, it cannot be reused because it is assumed to be contaminated. Thus, industrial engineers will have to consider these wastes to determine the stock of sticks that will be needed at the workstation.
Trays of various types to organize the sticks prior to the assembly operation. The purpose of providing different containers is for industrial engineers to evaluate which is the most appropriate type and the number of containers to run the assembly operation easily and safely.
Game configuration
The game consists of assembling the pegboard in a 50 second standard cycle time as shown in Figure 2. The game starts with the organization of the worktable with the items to be used and ends with the total assembly of the pegboard. The only restriction is that if a stick falls out of the board during the assembly operation, it cannot be reused (it is assumed to be contaminated).
Population and Sample
The study population consisted of students enrolled in the Quality and Productivity Management course at the Graduate School of Industrial Engineering of a university of Lima, Peru.
The game dynamics involved dividing the students into two distinct groups, each with well-defined roles, and whose responses were based on non-probabilistic directed samples. The group of industrial engineers consisted of 5 volunteer students, while the group of operators comprised the remaining 25 students.
The group of industrial engineers was responsible for designing the standard procedure for the pegboard assembly to be performed in a standardized cycle time of 50 seconds. This group was also in charge of timing the actual assembly cycle times and documenting the gap between the standard procedure designed and the actual one executed.
On the other hand, the group of operators was responsible for executing the pegboard assembly operations according to the standard procedure designed by the industrial engineers.
Pegboard Assembly Rounds
Two assembly rounds were designed for the unassembled pegboards as follows:
The first round was executed by the group of operators based on the job aid designed by the group of industrial engineers. The industrial engineers were asked to develop a procedure to assemble the pegboard in a cycle time that lasted 50 seconds. The procedure had to contemplate the items to be used, their organization on the worktable and the filling of the pegboard. The group of industrial engineers was told that they could take into account the ideas provided by the group of operators to create the job aid.
The teacher then gave a 50-minute class on the standard operating sheet, in which it was explained what a standard operating sheet is, what it is used for, its format, how to create one, and the sections that conform it.
Then the second assembly round was carried out by the group of operators following the standard operating sheet designed by the group of industrial engineers. This time, the members of the group of industrial engineers were no longer told that they could take into consideration the ideas provided by the group of operators to make the standard operating sheet. They were told in class that one of the strengths of the standard operating sheet design is that it incorporates the participation of the operators in its outline.
RESULTS
Evaluation of the Job Aid and the Standard Operating Sheet Prepared by the Industrial Engineers for the First and Second Pegboard Assembly Rounds
Table 1 shows a checklist evaluation of the instruments designed by the industrial engineers to standardize the pegboard assembly process. This checklist was completed at the end of both rounds by the students and the teacher in order to make the students aware of what they were able to achieve and what they still need to consolidate.
Table 1 shows several weaknesses observed in the procedure developed with the job aid during the first round. Although the industrial engineers outlined the logical sequence of operations, the operators faced challenges regarding the arrangement of items on their worktable (including the position of the pegboard and trays) and the organization of sticks in the trays. The industrial engineers did not incorporate visual training or symbology to emphasize crucial points for task execution. Furthermore, they did not provide justifications for why tasks should be performed as described, nor did they determine whether operators should work while standing or sitting. Limited integration with the group of operators was observed during the creation of the job aid. As a result, there was an increased degree of freedom and variability during the execution of the first round, as shown in Figure 3. These factors also influenced the achieved assembly cycle times, as shown in Table 2.
In contrast, Table 1 shows the results with the standard operating sheet designed by the industrial engineers for round 2. There was more precision in describing what tasks should be performed, how to do them and why they should be done that way. In addition, they exploited visual management, which made it easier for the group of operators to perform the tasks. There was also greater standardization both in the arrangement of the items on the worktable and in the assembly operation itself, but, above all, there was full integration between industrial engineers and operators to prepare the standard operating sheet, which can be seen in Table 3.
Table 1 Qualitative Assessment by Means of a Checklist of the Job Aid and Standard Operating Sheet Elaborated at the End of the Two Experimental Rounds.
Item | Procedure with job aid | Procedure with Standard Operating Sheet | ||
---|---|---|---|---|
YES | NO | YES | NO | |
Describes the operations necessary to do the job. | √ | √ | ||
Indicates the filling sequence of each hole in a clear, complete and simple manner. | √ | √ | ||
Explains why the operations must be done according to the standard. | X | √ | ||
Uses visual training (graphs, drawings) to explain how to perform operations. | X | √ | ||
Uses symbology to highlight key or critical points when performing certain operations. | X | √ | ||
Lists inventories and types of inventories that will be required to execute operations. | √ | √ | ||
Lists the resources required to execute operations. | √ | √ | ||
Specifies position and orientation of trays in the work center. | X | √ | ||
Specifies the number of sticks to be contained in each tray. | √ | √ | ||
Specifies how to arrange the sticks in each tray. | X | √ | ||
Specifies how to position the pegboard on the worktable. | X | √ | ||
Specifies the inclination that the peg board should have. | X | X | ||
Specifies whether the operator must execute the operation standing or sitting. | X | X | ||
Specifies how the operator has to use each hand to execute the operation. | X | √ | ||
Specifies what to do if a stick is dropped. | √ | √ | ||
Specifies the standard cycle time for the assembly operation. | √ | √ | ||
There is integration between the industrial engineers and operators in making the standard. | X | √ |
Source: Prepared by students and teacher at the end of both assembly rounds.
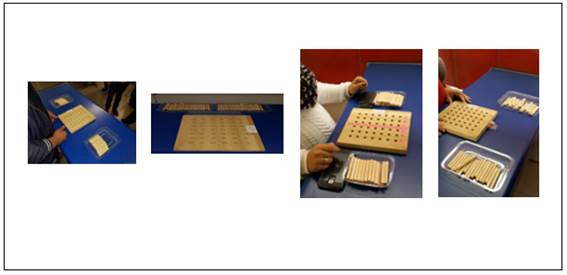
Note: All operators used the trays and number of sticks specified in the job aid, however the arrangement of the sticks on the work table was very different because it was not specified in the procedure. The photo on the left also shows an operator working standing up, while in the last two photos the operators performed the assembly operation sitting down. All of this had an impact on the amount of waste and the assembly cycle time.
Source: Prepared by the author.
Figure 3 Variability in the organization of the Required Items on the Worktable and in the Assembly Operation Based on the Job Aid Prepared by the Industrial Engineers.
Table 2 Assembly Cycle Times of the Pegboard Achieved in the First and Second Rounds.
Operator | Assembly cycle time with job aid (first round) | Assembly cycle time with standard operating sheet (second round) | Pegboard assembly cycle time difference (before − after) |
---|---|---|---|
1 | 48.83 | 44.36 | 4.47 |
2 | 47.09 | 50.36 | −3.27 |
3 | 47.96 | 39.57 | 8.39 |
4 | 48.07 | 45.56 | 2.51 |
5 | 56.68 | 50.14 | 6.54 |
6 | 46.22 | 50.36 | −4.14 |
7 | 51.23 | 49.05 | 2.18 |
8 | 50.36 | 40.77 | 9.59 |
9 | 49.16 | 37.17 | 11.99 |
10 | 47.96 | 43.16 | 4.8 |
11 | 54.06 | 49.16 | 4.9 |
12 | 50.58 | 47.96 | 2.62 |
13 | 51.45 | 43.16 | 8.29 |
14 | 48.83 | 41.97 | 6.86 |
15 | 50.36 | 49.16 | 1.2 |
16 | 48.07 | 46.76 | 1.31 |
17 | 46.22 | 46.76 | −0.54 |
18 | 51.45 | 47.96 | 3.49 |
19 | 50.58 | 50.36 | 0.22 |
20 | 54.06 | 47.96 | 6.1 |
21 | 47.96 | 46.87 | 1.09 |
22 | 48.83 | 50.36 | −1.53 |
23 | 49.16 | 46.76 | 2.4 |
24 | 50.36 | 47.96 | 2.4 |
25 | 47.96 | 46.76 | 1.2 |
Source: The times were measured by the group of industrial engineers supervised by a professor.
Table 3 Standard Operating Sheet Elaborated by the Group of Industrial Engineers in Coordination with the Group of Operators for the Second Pegboard Assembly Round.
Source: The preparation of the original document was done freehand by the students.
Statistical Results
Normality Test
First of all, the statistical analysis was carried out in SPSS Statistics version 22 to assess whether the random variable difference in assembly cycle time of the pegboard (before − after) responds to a normal distribution. These data (before − after) are shown in Table 2. The significance level chosen was 5%, and the test statistic used was Shapiro Wilk, since there was a total of 25 data. A p-value of 0.9396 was obtained, as shown in Table 4, so it can be affirmed with a probability of 93.96% that the distribution of the random variable does respond to a normal distribution. Next, the parametric test was carried out to compare averages in repeated measures.
Table 4 Normality Test.
Normality Tests | ||||||
---|---|---|---|---|---|---|
Kolmogorov-Smirnova | Shapiro-Wilk | |||||
Statistic | df | Sig. | Statistic | df | Sig. | |
Before | 0.152 | 25 | 0.14 | 0.913 | 25 | 0.035 |
After | 0.218 | 25 | 0.004 | 0.892 | 25 | 0.012 |
Difference = before − after | 0.131 | 25 | .200* | 0.983 | 25 | 0.9396 |
* This is a lower limit of true significance.
a. Lilliefors correction
Source: Results obtained in SPSS statistics version 22.
Student’s t-statistic Procedure for Repeated Measures
Approach: The pegboard assembly cycle time was measured in a group of students before and after the teaching and learning of the standard operating sheet through a game. Did the teaching and learning of the standard operating sheet decrease the pegboard assembly cycle time?
The first statistical-descriptive results obtained by running the normality test through SPSS are shown in Table 5, in which the confidence intervals for the mean at 95% have been consolidated. Table 6 shows the details of the statistical-ritual hypothesis.
Table 5 Confidence Intervals for the Mean (95%).
Measures | Pegboard assembly cycle time before (seconds) | Pegboard assembly cycle time after (seconds) | Time difference in pegboard assembly cycle time (before − after) (seconds) |
---|---|---|---|
Mean | 49.74 | 46.42 | 3.32 |
Standard error | 0.50 | 0.73 | 0.79 |
CI 95% lower limit | 48.71 | 44.91 | 1.70 |
IC 95% upper limit | 50.77 | 47.92 | 4.95 |
Source: Results obtained in SPSS statistics version 22.
Table 6 Statistical-Ritual Hypothesis.
Hypotheses H0: The average difference of the pegboard assembly cycle time is less than or equal to zero. ( 𝜇 𝑑 (𝑐𝑦𝑐𝑙𝑒 𝑡𝑖𝑚𝑒 𝑏𝑒𝑓𝑜𝑟𝑒−𝑐𝑦𝑐𝑙𝑒 𝑡𝑖𝑚𝑒 𝑎𝑓𝑡𝑒𝑟) ≤0) H1: The average difference of the pegboard assembly cycle time is less than or greater than zero. ( 𝜇 𝑑 (𝑐𝑦𝑐𝑙𝑒 𝑡𝑖𝑚𝑒 𝑏𝑒𝑓𝑜𝑟𝑒−𝑐𝑦𝑐𝑙𝑒 𝑡𝑖𝑚𝑒 𝑎𝑓𝑡𝑒𝑟) >0) |
Significance level (alpha) α = 5% |
Test statistic → Student’s t-test for repeated measures |
p-value = 0.000149 |
Decision: With a probability of error of 0.0149%, the average difference of the pegboard assembly cycle time is greater than zero. |
Source: Prepared by the author.
To validate research hypothesis H1, the Student’s t-test for related samples or repeated measures was run in SPSS. The results obtained are shown in Table 7. The p-value obtained by SPSS is 0.000298 and corresponds to a two-tailed test. However, since the test performed is a one-tailed test, we proceed to divide the p-value by two, from which we obtain a p-value = 0.000298 / 2 = 0.000149. Since the p-value obtained is less than the significance level of 5%, then the research hypothesis is accepted, as shown in Table 6.
Table 7 Student’s T-Test for Related Samples or Repeated Measures.
Paired Samples Test | ||||||||
---|---|---|---|---|---|---|---|---|
Paired Differences | t | df | Sig. (2-tailed) | |||||
Mean | Std. Deviation | Std. Error Mean | 95% Confidence Interval of the Difference | |||||
Lower | Upper | |||||||
Pair 1 before − after | 3.322 | 3.931 | 0.786 | 1.699 | 4.945 | 4.225 | 24 | 0.000298 |
Source: Results obtained in SPSS statistics version 22.
DISCUSSION
Based on the results obtained through inferential statistics, it can be affirmed that there is a decrease in the pegboard assembly cycle time after the teaching and learning of the standard operating sheet, since the confidence interval for the difference of the assembly cycle time does not contain zero.
This is supported by the p-value obtained since it is less than the 5% significance level, which confirms that there is a significant difference in the pegboard assembly cycle time before and after the teaching and learning of the standard operating sheet.
The results of the qualitative assessment of both tools (Table 1) also show that the standard operating sheet is a tool that allowed a more complete, detailed, and clear structuring of the information, since the design of the tool itself requires stating the tasks to be performed, identifying key points and justifying why the activities should be performed in a certain way. The tool also incorporates a visual training section that facilitates the understanding of how the activities should be executed. The tool and its processes helped reduce the variability of the pegboard assembly process.
The Productivity Press Development Team (2002) argues that knowing what to do and how to do it is not enough. It is important to understand why tasks should be performed the way they must, otherwise the established procedure could be weakened over time through the informal incorporation or suppression of operations, which would reduce the quality of a product or process or even impact on other processes of the company without being aware of the impact of these actions. With the standard operating sheet this risk is minimized or totally eliminated, since this tool requires explaining why the work must be performed as it has been standardized.
An important aspect to highlight, as shown in Table 1, is that the suggestions of the group of operators were considered in the preparation of the standard operating sheet, which made teamwork more effective and more productive. This was possible because the tool recommends the active participation of the operating team in the formulation of the standardized work.
Similar to the findings of Có et al. (2008), it was observed that the industrial engineers who participated in this game were able to question their prior knowledge and enhance their understanding of lean manufacturing. The students improved their perception and training in using tools for process standardization, and they analyzed the advantages of working with the standard operating sheet from a statistical perspective.
It was also observed that, as Possebon et al. (2012) stated, the game dynamics in class favored the consolidation of theoretical content, stimulated group work, and fostered discussion of the results obtained.
Finally, as highlighted by De Figueiredo (2010), games are instruments that not only motivate students in their learning process but also serve as valuable tools for tackling the complexities encountered when studying various theories. They are valuable strategies for educators to effectively transmit knowledge.
CONCLUSIONS
The standard operating procedures or job aids are tools that enable work standardization. However, with the dynamics applied in this research, it has been possible to appreciate that the standard operating sheet is an instrument that, due the nature of its structure, symbology and visual elements, helps to communicate more clearly a standard and this is reflected in the operation cycle time, as it has been verified.
The results obtained in this article can be replicated in other academic environments, for which other academic settings and teaching colleagues are encouraged to replicate methodology and experimental rounds described in this article in classroom settings, since this provides a simple and very economical way to reinforce knowledge in an experiential, practical and fun way.
The proposed results can also be validated in manufacturing companies by using the proposed game to train employees in the creation and dissemination of standardized work, so that the company personnel can be made aware of the advantages of the standard operating sheet with respect to conventional procedures.
It is expected that this work will encourage manufacturing and service companies to adopt the standard operating sheet not only for clearer transmission of standards but also for promoting integration between the front and back offices within the company.
RECOMMENDATIONS
Future research is encouraged to improve and enrich this game by reapplying it to work standardization, but with other tools, such as the standard operating combination; standard work sheet for work center; standard work sheet for each workstation, etc., as well as other lean principles.
REFERENCIAS BIBLIOGRÁFICAS
Aguilar Ortega, C. O., Tovar Luna, B., y Hernández Cruz, B. A. (2018). Escenarios de aprendizaje basados en simulación: experiencia multidisciplinaria de la Universidad del Valle de México. FEM: Revista de La Fundación Educación Médica, 21(4), 195-200. https://doi.org/10.33588/FEM.214.956 [ Links ]
Có, F. A., Có, M. A., y Merigueti, B. A. (13-16 de octubre de 2008). O “heyjunka didático”: um jogo interdisciplinar que auxilia na elevação da aprendizagem sobre a produção enxuta. XXVIII Encontro Nacional de Engenharia de Produção - ENEGEP, Rio de Janeiro, RJ, Brasil. https://abepro.org.br/biblioteca/enegep2008_TN_STO_078_544_10935.pdf [ Links ]
Arnau, J., y Bono, R. (2008). Estudios longitudinales de medidas repetidas: Modelos de diseño y análisis. Escritos de Psicología - Psychological Writings, 2(1), 32-41. https://www.redalyc.org/articulo.oa?id=271020194005 [ Links ]
De Figueiredo, J. C. B. (2010). Modelo computacional para simulação de aplicação da teoría das restriçoes. Revista Alcance, 17(2), 19-31. http://www.redalyc.org/articulo.oa?id=477748590003 [ Links ]
Bragança, S., y Costa, E. (2015). An Application of the Lean Production Tool Standard Work. Jurnal Teknologi, 76(1), 47-53. https://doi.org/10.11113/JT.V76.3659 [ Links ]
Possebon, F. R., Fontana, J., y Hoss, M. (15-18 de octubre de 2012). Dinâmica de Grupo sobre Folha de Operações Padrão. XXXII Encontro Nacional de Engenharia de Produção, Bento Gonçalves, RS, Brasil. https://abepro.org.br/biblioteca/enegep2012_tn_wic_166_963_20652.pdf [ Links ]
De Freitas, E. S., y Da Silva, M. G. (2017). Pesquisa-ação sobre a implementação do trabalho padronizado em uma célula de manufatura de uma fábrica de tratores. Espacios, 38(46), 21-38. https://www.revistaespacios.com/a17v38n46/17384621.html [ Links ]
De Oliveira, V. F., De Almeida, N. N., Carvalho, D. M., y Pereira, F. A. A. (2013). Um Estudo sobre a Expansão da Formação em Engenharia no Brasil. Revista de Ensino de Engenharia, 32(3), 37-56. http://revista.educacao.ws/revista/index.php/abenge/article/view/235 [ Links ]
Dos Santos, D. M. C., Dos Santos, B. K., y Dos Santos, C. G. (2021). Implementation of a standard work routine using Lean Manufacturing tools: A case Study. Gestão & Produção, 28(1), 23-32. https://doi.org/10.1590/0104-530X4823-20 [ Links ]
Fazinga, W. R., y Saffaro, F. A. (2012). Identificação dos elementos do trabalho padronizado na construção civil. Ambiente Construído, 12(3), 27-44. https://doi.org/10.1590/S1678-86212012000300003 [ Links ]
Fleury, A., Almada, F. y Monteiro, M. (2008). Introdução à Engenharia de Produção (1ª ed.). Rio de Janeiro, Brasil: Elsevier Campus. [ Links ]
Hernández Sampieri, R., Fernández Collado, C., y Baptista Lucio, P. (2014). Metodología de la Investigación. México D. F., México: McGraw Hill. [ Links ]
Lean Enterprise Institute. (2014). Lean Lexicon. A Graphical Glossary for Lean Thinkers (5a ed.). New York, NY, EE. UU.: Lean Enterprise Institute, Inc. [ Links ]
Liker, J. K., y Meier, D. (2007). Toyota Talent : Developing your People the Toyota Way (1a ed.). New York, NY, EE. UU.: McGraw Hill. [ Links ]
Liker, J. K., y Meier, D. (2006). The Toyota Way Fieldbook. New York, EE. UU.: McGraw Hill. [ Links ]
Masaaki, I. (1986). Kaizen: The Key to Japan’s Competitive Success (1a ed.). New York, NY, EE. UU.: McGraw Hill. [ Links ]
Pereira, A., Abreu, M. F., Silva, D., Alves, A. C., Oliveira, J. A., Lopes, I., y Figueiredo, M. C. (2016). Reconfigurable Standardized Work in a Lean Company - A Case Study. Procedia CIRP, 52, 239-244. https://doi.org/10.1016/J.PROCIR.2016.07.019 [ Links ]
Rother, M. (2010). Toyota Kata: Managing People for Improvement, Adaptiveness, and Superior Results (2a ed.). New York, NY, EE. UU.: McGraw Hill . [ Links ]
Shimizu, K. (2004). Reorienting Kaizen Activities at Toyota : Kaizen, Production Efficiency, and Humanization of Work. Okayama Economic Review, 36(3), 1-25. https://doi.org/10.18926/OER/40530 [ Links ]
Spear, S., y Bowen, H. K. (1999). Decoding the DNA of the Toyota Production System. Harvard Business Review, 77(5), 96-106. [ Links ]
Tapia, F. (2014). Aplicación de un juego de empresa como recurso didáctico para mejorar la enseñanza-aprendizaje del planeamiento y control de la producción según el modelo de teoría de restricciones. (Tesis doctoral). Universidad San Martin de Porres, Lima. https://hdl.handle.net/20.500.12727/681 [ Links ]
The Productivity Press Development Team. (2002). Standard Work for the Shopfloor. New York, NY, EE. UU.: CRC Press Taylor & Francis Group. [ Links ]
Received: October 26, 2022; Accepted: November 16, 2022