INTRODUCCIÓN
En este artículo se describe un caso aplicativo de la metodología Lean Six Sigma, basado en el principio DMAIC para mejorar los procesos de reparación en una empresa metalmecánica. El objetivo del estudio es contribuir a la mejora de los servicios de los procesos de reparación de componentes de maquinaria pesada para la minería.
El uso de esta metodología en las empresas metalmecánicas es novedoso. La correcta aplicación de Lean Six Sigma puede ayudar a las empresas a mejorar su productividad, lo que redundará en la satisfacción de los clientes, ya que se reducirán los tiempos de parada de sus maquinarias y la producción podrá desarrollarse de manera fluida sin problemas.
En el estudio se tomó como referencia a una empresa metalmecánica que repara componentes de maquinara pesada utilizados en la actividad minera. Por políticas de la empresa, no se revelará el nombre de la misma.
La empresa metalmecánica está experimentando una baja productividad en los procesos de reparación de los componentes de maquinaria pesada, concretamente en las áreas de Planeamiento, Soldadura, Maquinado, Montaje y Control de Calidad. Para solucionar este problema, se propone implementar una metodología que mejorare los procesos y, por consiguiente, incremente la productividad y minimice los defectos en los componentes reparados.
Tras realizar el análisis de datos correspondientes al periodo 2021, se constató que el nivel de defectos se situaba en torno al 50% con un nivel sigma que oscilaba entre 2.19 a 2.57. Asimismo, la eficacia se situó entre el 70% y el 87%, lo que se tradujo en un índice de productividad de entre 0.77 y 0.85.
En este estudio se proporciona una descripción detallada de las etapas del sistema DMAIC, que implica el uso de varias herramientas como SIPOC, Pareto, gráficos de control, análisis de capacidad y T-pareada.
Al final se harán recomendaciones para la utilización de herramientas que servirán para mejorar la productividad y, por ende, satisfacer las necesidades de los clientes. También se demostrará que la implementación del Lean Six Sigma es factible.
Objetivo
Mejorar la productividad de una empresa metalmecánica reduciendo los defectos de reparación de los componentes de maquinaria pesada para la actividad minera.
Objetivos específicos
Mejorar el cumplimiento en el tiempo acordado con el cliente en la reparación de los componentes de maquinaria pesada para la minería, con una meta de al menos 90% de cumplimiento.
Disminuir el nivel de producto no conforme en un 25% como máximo.
Problemática
¿Cómo mejorar la productividad en la reparación de los componentes de maquinaria pesada con la aplicación de la metodología Lean Six Sigma?
Hipótesis
Ho: Aplicando la metodología Lean Six Sigma en la reparación de los componentes de maquinaria pesada, la productividad del 2022 es igual a la productividad del 2021.
Ha: Aplicando la metodología Lean Six Sigma en la reparación de los componentes de maquinaria pesada, la productividad del 2022 es mayor que la productividad del 2021.
MARCO TEÓRICO
El tiempo de reparación de los componentes de maquinaria pesada es crucial para la producción minera. La empresa en estudio realiza reparaciones de categoría V, que incluye las reparaciones de chasis, bastidores, front axle, cucharones, etc. El proceso de reparación implica que el componente pase por la sección de soldadura, donde se reparan fisuras, se rellenan alojamientos y asientos, se sueldan repuestos, entre otros. A continuación, el componente pasa por el área de maquinado para ejecutar el proceso de mecanizado de los alojamientos con la finalidad de recuperar las medidas estándar. Después, pasa por las respectivas inspecciones y, por último, se procede a la preparación para el montaje de dicho componente (si lo requiere). La empresa en estudio necesita mejorar la productividad, que se expresa como el producto fabricado por recurso utilizado para la producción, según Bernal (2019). También se le conoce como la razón del índice de eficacia sobre la eficiencia, es decir, los resultados obtenidos por unidad de recursos utilizados adecuadamente.
La eficiencia, como lo afirma Bernal (2019), tiene muchas definiciones dependiendo de diferentes aspectos. Así, por ejemplo, en el caso de las unidades de tiempo, es la razón de tiempo de proceso real sobre el tiempo del proceso estándar. Mientras que, en el caso de los recursos, la eficiencia se entiende como la utilización adecuada de los mismos. Otra definición es la ratio de trabajos despachados sobre los trabajos proyectados.
Por otro lado, la eficacia es la razón de abordar tanto los riesgos como las oportunidades que se presentan en el mercado (clientes). También se define como los resultados alcanzados que cumplen con los objetivos establecidos por las organizaciones (ver Tabla 1).
Tabla 1 Diferencia entre eficiencia y eficacia.
Eficiencia | Eficacia |
---|---|
Énfasis en los medios | Énfasis en los resultados |
Hacer las cosas de manera correcta | Hacer las cosas correctas |
Resolver problemas | Alcanzar objetivos |
Salvaguardar los recursos | Optimizar la utilización de los recursos |
Cumplir tareas y obligaciones | Obtener resultados |
Entrenar a los subordinados | Proporcionar eficacia a los subordinados |
Fuente: Elaboración propia con base en Bernal (2019).
El yield es importante para este estudio. De acuerdo con Álvarez (2019), el yield mide la calidad la calidad de los procesos de la producción; se calcula como la relación entre la producción de unidades sin fallas sobre la producción de unidades con fallas. En el contexto de Lean Six Sigma, el yield es un indicador clave de rendimiento (KPI) en los proyectos de mejora de los procesos. También se utiliza para controlar la eficacia de las actividades de los proyectos o procesos de mejora.
De acuerdo con lo expresado por Olabarrera (2021), el Lean Six Sigma es una estrategia de negocios que resulta de la fusión de las metodologías Lean manufacturing y Six Sigma, cuyo objetivo es optimizar el desempeño de los procesos e incrementar la satisfacción de los clientes. Dicha metodología se centra en el volumen de producción y en la mejora continua en las organizaciones. La base de Lean Six Sigma es la disciplina DMAIC (definir, medir, analizar, mejorar y controlar), que pretende reducir la variabilidad de los procesos de producción.
Definir consiste en identificar los aspectos clave internos y externos que afectan a la empresa.
Medir consiste en utilizar herramientas estadísticas para la recolección de datos de los procesos productivos.
Analizar consiste en evaluar las posibles causas del inadecuado funcionamiento del sistema.
Mejorar consiste en proponer las posibles soluciones para minimizar o erradicar de raíz las causas que afectan al sistema de proceso en estudio.
Controlar consiste en establecer un plan de control para evitar que vuelvan a producirse estos problemas.
Los objetivos del Lean Six Sigma son eliminar desperdicios, eliminar actividades que no agregan valor al producto o servicio, reducir el tiempo o ciclo y reducir la variabilidad del proceso. Por otro lado, los objetivos de la empresa de referencia son obtener una eficiencia superior al 90%, alcanzar a una eficacia superior al 90% y reducir el número de defectos a 3.4 partes por millón.
En la Figura 1, se observa una representación visual de estos objetivos.
Para la implementación de la metodología Lean Six Sigma, se requiere la utilización de herramientas estadísticas como el diagrama de Pareto, que consiste en clasificar las incidencias de mayor a menor para luego tratar de minimizarlas o erradicarlas. Otra herramienta es el Kanban, que permite clasificar los trabajos en función de sus etapas y prioridades con la finalidad de realizar una adecuada programación de las actividades de producción. La herramienta Heinjunka consiste en establecer objetivos para nivelar la producción y conseguir mejoras en los resultados.
METODOLOGÍA
En esta investigación, se adoptó un enfoque cuantitativo porque se recogieron datos (eficiencia, eficacia y el desempeño de la calidad) en un taller de una empresa metalmecánica (estos datos entrarán a la simulación). Es no experimental y transversal porque los datos se recogieron en un único momento. Es descriptiva porque explica la comparación de los resultados actuales con los resultados obtenidos después de la simulación, lo que nos dará a conocer la viabilidad de la metodología Lean Six Sigma.
RESULTADOS
Fase 1: Definir
Los resultados del estudio revelaron que la empresa tiene un nivel bajo en el indicador de productividad, lo que podría dificultar el cumplimiento de los requerimientos de los clientes. Los procesos de reparación de los componentes pertenecientes a la categoría V son los que tienen un nivel bajo de productividad y esta representa el 45% de sus ventas. Además, los costos de dichas reparaciones están valorizados en más de $50,000 (ver Tabla 2).
Tabla 2 Costos de reparaciones de algunos componentes pertenecientes a la categoría V.
CHASIS | BASTIDOR | CUCHARÓN | LAMPONES | FRONT AXLE | ||
---|---|---|---|---|---|---|
Material directo | Plancha 2500 x 2500 x 12.5 mm | $ 500.00 | $ 800.00 | $ 950.00 | $ 500.00 | $ 400.00 |
Alambre tubular E71 | $ 64.30 | $ 130.00 | $ 150.00 | $ 200.00 | $ 100.00 | |
Soldadura SUPERCITO E80 1/4" | $ 3,520.00 | $ 210.84 | $ 110.00 | $ 100.00 | $ 90.00 | |
Soldadura Tenacito E80 1/4" | $ 0.00 | $ 0.00 | $ 0.00 | $ 70.28 | $ 100.00 | |
Repuestos por importación | $ 50,000.00 | $ 76,000.00 | $ 50,000.00 | $ 60,000.00 | $ 65,000.00 | |
Total material directo | $ 54,084.30 | $ 77,140.84 | $ 51,210.00 | $ 60,870.28 | $ 65,690.00 | |
Mano de obra directa | Soldadores | $ 2,677.00 | $ 3,355.00 | $ 7,500.00 | $ 2,600.00 | $ 3,900.00 |
Maquinistas | $ 1,500.00 | $ 1,650.00 | $ 1,754.00 | $ 2,112.00 | $ 1,771.00 | |
Inspecciones | $ 576.00 | $ 300.00 | $ 400.00 | $ 492.00 | $ 480.00 | |
Mecánicos | $ 1,150.00 | $ 1,020.00 | $ 1,110.00 | $ 1,200.00 | $ 1,080.00 | |
Total de mano de obra | $ 5,903.00 | $ 6,325.00 | $ 10,764.00 | $ 6,404.00 | $ 7,231.00 | |
Costo de reparación | $ 59,987.30 | $ 83,465.84 | $ 61,974.00 | $ 67,274.28 | $ 72,921.00 |
Fuente: Elaboración propia.
De acuerdo con Arcos y Cerda (2019), el bajo nivel del indicador productividad es ocasionado por el incumplimiento de los tiempos y el alto índice de defectos de los componentes reparados. El proceso de reparación se puede apreciar en la Figura 2.
Se utilizó la herramienta SIPOC para describir cómo realizar la reparación de los componentes pertenecientes a la categoría V donde los proveedores y los clientes ingresan materiales, insumos y componentes a reparar, tal como se observa en la Figura 3 (Canahua, 2020; Castillo, 2021; Corzo y Teccsi, 2019).
Fase 2: Medir
Una vez definido el problema, se procedió a medir el nivel sigma de los componentes correspondientes a la categoría V, tal como se observa en la Tabla 3 (Alvarez, 2019; Castillo, 2019; Carrillo et al., 2021; Valverde y Reyes, 2021).
Tabla 3 Nivel sigma del año 2021 en la reparación de los componentes de la categoría V.
Meses | Componentes categoría V | No. PNC | % defectos 21 | Oportunidad | DPMO | DPO | Yield (PNC) | Nivel sigma 21 |
---|---|---|---|---|---|---|---|---|
Ene-21 | 15 | 10 | 66.67% | 3 | 222222.222 | 0.22222222 | 77.78% | 2.37 |
Feb-21 | 20 | 12 | 60.00% | 3 | 200000 | 0.2 | 80.00% | 2.46 |
Mar-21 | 20 | 14 | 70.00% | 3 | 233333.333 | 0.23333333 | 76.67% | 2.32 |
May-21 | 10 | 8 | 80.00% | 3 | 266666.667 | 0.26666667 | 73.33% | 2.19 |
Jun-21 | 25 | 15 | 60.00% | 3 | 200000 | 0.2 | 80.00% | 2.46 |
Jul-21 | 15 | 9 | 60.00% | 3 | 200000 | 0.2 | 80.00% | 2.46 |
Set-21 | 20 | 15 | 75.00% | 3 | 250000 | 0.25 | 75.00% | 2.25 |
Oct-21 | 25 | 15 | 60.00% | 3 | 200000 | 0.2 | 80.00% | 2.46 |
Nov-21 | 25 | 13 | 52.00% | 3 | 173333.333 | 0.17333333 | 82.67% | 2.57 |
Dic-21 | 15 | 9 | 60.00% | 3 | 200000 | 0.2 | 80.00% | 2.46 |
Total | 190 | 98 | 51.58% | 78.46% |
Fuente: Elaboración propia.
Como se puede apreciar en el Tabla 3, el nivel sigma está alejado de la meta (3.4), ya que oscila entre 2.19 a 2.57. Además, la cantidad del producto no conforme oscila entre 8 y 15 unidades, por lo que el porcentaje de defectos oscila entre 52% y 80% en el año 2021.
Luego, se procedió a realizar la medición de la productividad en las reparaciones de los componentes pertenecientes a la categoría V a partir de los indicadores que maneja la empresa, que son la eficacia y la eficiencia (ver Tabla 4).
Tabla 4 Productividad total de los componentes de la categoría V reparados.
Meses | Tiempo acordado (Días) | Tiempo real (Días) | Eficacia 21 | Horas-Hombre asignadas | Horas-hombre reales | Eficiencia del tiempo | Productividad 21 |
---|---|---|---|---|---|---|---|
Ene-21 | 55 | 70 | 78.57% | 571.45 | 601.45 | 95.01% | 0.82696 |
Feb-21 | 45 | 60 | 75.00% | 321.00 | 345.00 | 93.04% | 0.80607 |
Mar-21 | 65 | 75 | 86.67% | 730.56 | 754.56 | 96.82% | 0.89514 |
May-21 | 35 | 44 | 79.55% | 530.46 | 545.46 | 97.25% | 0.81795 |
Jun-21 | 35 | 42 | 83.33% | 530.46 | 546.46 | 97.07% | 0.85847 |
Jul-21 | 25 | 32 | 78.13% | 435.89 | 453.89 | 96.03% | 0.81351 |
Set-21 | 35 | 50 | 70.00% | 645.35 | 763.35 | 84.54% | 0.82799 |
Oct-21 | 45 | 55 | 81.82% | 321.00 | 331.00 | 96.98% | 0.84367 |
Nov-21 | 65 | 80 | 81.25% | 730.56 | 750.56 | 97.34% | 0.83474 |
Dic-21 | 25 | 35 | 71.43% | 435.90 | 471.90 | 92.37% | 0.77328 |
78.57% | 0.82978 |
Fuente: Elaboración propia.
Los datos de productividad total para el año 2021 se muestran en la Tabla 4. Los resultados muestran que la productividad oscila entre 0.77 y 0.85, lo que indica que la eficacia oscila entre 70% y 86.67%, porcentaje inferior a la meta establecida por la empresa del 90%. En cuanto a la eficiencia de las horas-hombre oscilan entre 84.54% y 97.34%. El informe concluye que la empresa no cumple con las metas establecidas para la productividad a pesar de utilizar adecuadamente las horas-hombre.
Los resultados de la productividad fueron sometidos a diferentes pruebas, en la Figura 4 se muestra el informe de las mismas.
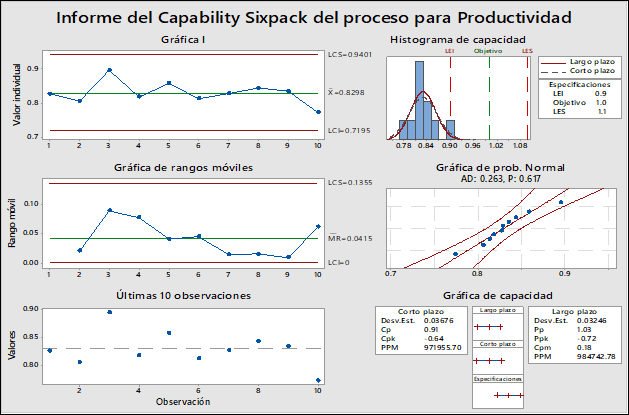
Fuente: Elaboración propia, basada en Cruz (2019).
Figura 4 Informe de la productividad de los componentes reparados de la categoría V.
Como se puede apreciar en la Figura 4, los datos de productividad se sometieron a una prueba de normalidad, que arrojó un valor p de 0.617, superior a 0.05. A continuación, se realizó un gráfico de control I que indica que la productividad de los componentes de la categoría V está bajo control estadístico, pero la variabilidad debe reducirse. También se realizó la medición de la capacidad de la productividad, que se interpretó según los límites 0.9 y 1.1 y un objetivo de 1, y se comprobó que es inherentemente incapaz, ya que se obtuvo un Cp 0.91 y un Cpk −0.64 y la productividad está desplazada hacia la izquierda. Por lo tanto, se recomienda que la empresa estabilice y centre los resultados de la productividad para alcanzar sus objetivos.
Fase 3: Analizar
Durante la fase 3, el equipo realizó el análisis de las causas de los retrasos con la finalidad de erradicarlas o minimizarlas.
Para detectar las causas, se utilizaron diagramas de Pareto con la finalidad de detectar, minimizar o erradicar la(s) causa(s) raíz de la baja productividad en la reparación de los componentes pertenecientes a la categoría V. La Figura 5, ilustra el informe de la productividad de los componentes reparados (Guerra, 2019; Pastor, 2018; Chamorro, 2017).
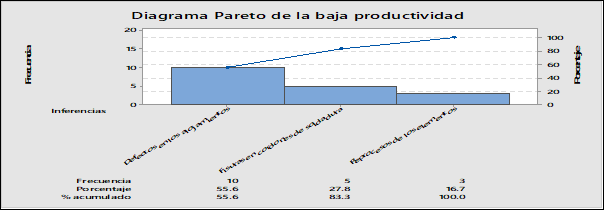
Fuente: Elaboración propia.
Figura 5 Informe de la productividad de los componentes reparados de la categoría V.
Como se puede observar en la Figura 6, se aplicó el principio 80/20 para determinar las incidencias más frecuentes: defectos en los alojamientos y fisuras en cordones de soldadura.
Se dio prioridad a la incidencia más alta, que era la de los «defectos en los alojamientos». A continuación, se realizó otro diagrama de Pareto con la finalidad de determinar la causa de estos defectos. En la Figura 6, se muestra la aplicación del mismo principio.
En la Figura 6, el diagrama de Pareto reveló las incidencias más frecuentes: corrección en los procesos de soldadura y poros en las zonas rellenadas.
A continuación, el equipo seleccionó como prioritaria la «corrección en los procesos de soldadura», al tener la mayor incidencia.
Por último, se realizó otro diagrama de Pareto para llegar a la causa diagnóstico, que se muestra en la Figura 7.
Tras realizar un análisis, se determinó que la baja productividad se debía a los defectos en los alojamientos. Estos defectos eran causados por las correcciones de los errores en los procesos de soldadura, cuya causa principal es el procedimiento inadecuado de soldadura.
Fase 4: Implementar (Mejorar)
Una vez detectadas las causas, el equipo propuso dos métodos para minimizar las causas de la baja productividad.
Implementación del Kanban. Este sistema se utiliza con la finalidad de planificar y programar las actividades de reparación de los componentes en función del nivel de prioridad (rojo para alta, amarillo para media y verde para baja). El tablero Kanban se presenta en la Figura 8.
Implementación Heinjunka. Esta herramienta se utiliza con la finalidad de nivelar las reparaciones de los componentes en función del nivel de prioridad. Además, como valor agregado, se implementó un cuadro de metas, submetas y límites (lo que estamos dispuestos a cumplir con los recursos con los que cuenta la empresa) para cumplir con las expectativas de los clientes. El objetivo de utilizar el tablero Heinjunka es minimizar el tiempo de entrega a los clientes y mejorar la comunicación con ellos (ver Figuras 9 y 10).
La tabla presentada anteriormente se ha generado con la herramienta Heinjunka y se basa en los siguientes indicadores: eficiencia, eficacia, producto no conforme, yield, tiempo de entrega al cliente y productividad.
Para minimizar los defectos y con ello reducir los retrasos e incrementar la productividad se recomienda implementar un nuevo procedimiento de soldadura. El proceso de soldadura que se utiliza actualmente en la empresa en estudio es el SMAW (Shielded Metal Arc Welding), que consiste en utilizar un electrodo para unir dos metales. También se le conoce como proceso de soldadura de arco con electrodo revestido. Sin embargo, este proceso tiene desventajas como dejar chisporroteos y porosidades que requieren rectificado adicional con esmeril. En cambio, el procedimiento FCAW (Flux Cored Arc Welding) consiste en el soldeo con alambre tubular con gas revestido. Este proceso es ventajoso porque tolera fuertes corrientes de aire y es de bajo costo.
Fase 5: Controlar la mejora
En esta etapa, se realizó la asignación de responsabilidades del personal del área de producción. Las responsabilidades se dividieron del siguiente modo:
Al equipo de planeamiento se le asignó el control del programa de producción mediante la herramienta Kanban. Otro equipo estuvo a cargo de la implementación del Heinjunka, el mantenimiento de los componentes y la coordinación con los líderes de las áreas involucradas (Maquinado, Soldadura, Planeamiento y Producción). Mientras que la implementación del procedimiento FCAW se les asignó a los soldadores homologados con amplia experiencia.
Tras aplicar las mejoras en los procesos de reparación de los componentes que pertenecen a la categoría V, se obtuvieron los resultados presentados en la Tabla 5.
Tabla 5 Posibles resultados del nivel sigma en el periodo 2022.
Meses | Componentes categoría V | N.° PNC 22 | % defectos 22 | Oportunidad | DPMO | DPO | Yield (PNC) | Nivel sigma 22 |
---|---|---|---|---|---|---|---|---|
Ene-22 | 15 | 3 | 20.00% | 3 | 66666.6667 | 0.06666667 | 93.33% | 3.02 |
Feb-22 | 20 | 5 | 25.00% | 3 | 83333.3333 | 0.08333333 | 91.67% | 2.95 |
Mar-22 | 20 | 6 | 30.00% | 3 | 100000 | 0.1 | 90.00% | 2.88 |
May-22 | 10 | 2 | 20.00% | 3 | 66666.6667 | 0.06666667 | 93.33% | 3.02 |
Jun-22 | 25 | 4 | 16.00% | 3 | 53333.3333 | 0.05333333 | 94.67% | 3.07 |
Jul-22 | 15 | 3 | 20.00% | 3 | 66666.6667 | 0.06666667 | 93.33% | 3.02 |
Set-22 | 20 | 5 | 25.00% | 3 | 83333.3333 | 0.08333333 | 91.67% | 2.95 |
Oct-22 | 25 | 6 | 24.00% | 3 | 80000 | 0.08 | 92.00% | 2.96 |
Nov-22 | 25 | 6 | 24.00% | 3 | 80000 | 0.08 | 92.00% | 2.96 |
Dic-22 | 15 | 5 | 33.33% | 3 | 111111.111 | 0.11111111 | 88.89% | 2.83 |
Total | 190 | 37 | 19.47% | 91.99% |
Fuente: Elaboración propia.
Como se puede apreciar en la tabla anterior, se produjo una mejora del nivel sigma que oscila entre 2.83 y 3.07, es decir, que está cerca de la meta de 3.4. Los resultados de la simulación sugieren que para obtener un nivel sigma adecuado, el producto no conforme debe reducirse en un intervalo de 2 a 6 defectos por mes.
Los posibles resultados del nivel sigma se presentan en la Tabla 6.
Tabla 6 Posibles resultados del nivel sigma en el periodo 2022.
Meses | Tiempo acordado | Tiempo real | Eficacia 22 | Horas-hombre asignadas | Horas-hombre reales | Eficiencia del tiempo | Productividad 22 |
---|---|---|---|---|---|---|---|
Ene-22 | 55 | 59 | 93.22% | 571.45 | 601.41 | 95.02% | 0.98108 |
Feb-22 | 45 | 48 | 93.75% | 321.00 | 345.00 | 93.04% | 1.00759 |
Mar-22 | 65 | 66 | 98.48% | 730.56 | 736.77 | 99.16% | 0.99322 |
May-22 | 35 | 35 | 100.00% | 530.46 | 544.30 | 97.46% | 1.02609 |
Jun-22 | 35 | 38 | 92.11% | 530.46 | 545.00 | 97.33% | 0.94630 |
Jul-22 | 25 | 27 | 92.59% | 435.89 | 456.80 | 95.42% | 0.97034 |
Set-22 | 35 | 36 | 97.22% | 645.35 | 655.90 | 98.39% | 0.98812 |
Oct-22 | 45 | 45 | 100.00% | 321.00 | 330.00 | 97.27% | 1.02804 |
Nov-22 | 65 | 68 | 95.59% | 730.56 | 735.78 | 99.29% | 0.96271 |
Dic-22 | 25 | 26 | 96.15% | 435.90 | 440.89 | 98.87% | 0.97255 |
95.91% | 97.13% | 0.98760 |
Fuente: Elaboración propia.
Con base en lo mostrado en la Tabla 5, mantener un nivel adecuado de productividad que oscile entre 0.94630 y 1.02804 requiere un cumplimiento promedio del 95% y una eficiencia mensual del 97% mediante una utilización adecuada de los recursos.
El reporte que se muestra en la Figura 11 se generó a partir de los posibles resultados productividad obtenidos.
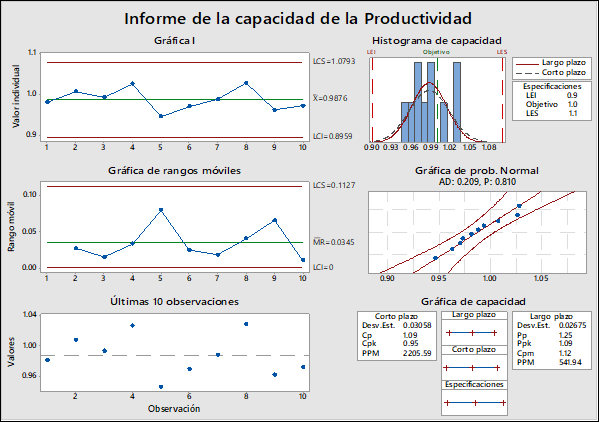
Fuente: Elaboración propia con los datos mejorados.
Figura 11 Reporte de los resultados de la posible capacidad de la productividad.
Como se observa en la Figura 11, los datos mejorados de la productividad siguen una distribución normal, ya que se obtuvo un valor p de 0.81. Es decir, este valor es superior a 0.05 en la gráfica I, lo que indica que los indicadores de la productividad mensual están bajo control estadístico. Sin embargo, se recomienda disminuir la variabilidad. En cuanto a los indicadores de capacidad Cp y Cpk arrojaron posibles resultados de 1.09 y 0.95 respectivamente, lo que indica que el nivel de productividad es inherentemente capaz. No obstante, se recomienda centrar los niveles.
Tras realizar la investigación y aplicar la metodología Lean Six Sigma en una simulación, se obtuvieron mejoras en la productividad.
A continuación, se realizó la contrastación de hipótesis.
Ho: Aplicando la metodología Lean Six Sigma en la reparación de los componentes de maquinaria pesada, la productividad del 2022 es igual a la productividad del 2021.
Ha: Aplicando la metodología Lean Six Sigma en la reparación de los componentes de maquinaria pesada, la productividad del 2022 es mayor que la productividad del 2021.
En la Figura 12, se utilizó la prueba t pareada para comprobar si la aplicación de Lean Six Sigma mejoró la productividad en la reparación de los componentes de maquinaria pesada.
Según el informe mostrado, el valor de p es 0.000, es decir, es inferior a 0.05. Por lo tanto, se rechaza la hipótesis nula y se concluye que la aplicación de la metodología LSS es viable y conduce a un incremento de la productividad, lo que supone una mejora de la productividad.
DISCUSIÓN
En la Tabla 7, se muestran las mejoras que se obtendría al aplicar la metodología Lean Six Sigma considerando los parámetros más importantes para el negocio.
Tabla 7 Cuadro de mejoras de los indicadores de los años 2021 y 2022.
Parámetro | Año 2021 | Año 2022 | Observaciones |
---|---|---|---|
Eficacia | 78.57% | 95.91% | Mejora en el tiempo de entrega |
Índice de producto no conforme | 51.68% | 19.47% | Mejora los procesos de reparación |
Eficiencia de horas-hombre | 84.54% - 97.34% | 93.04% - 99.29% | Rango de eficiencia |
Productividad | 0.82978 | 0.98760 | Reparación de componentes de maquinaria minera |
Proceso de soldadura | SMAW | FCAW | Mejora en el proceso de soldadura |
Fuente: Elaboración propia.
Se observa mejoras significativas tras la aplicación de la metodología LSS, sobre todo en los parámetros que generan más ingresos y reducen costos a la empresa.
Los mejores resultaron se obtuvieron en los parámetros eficacia, que pasó del 79% al 96%, la eficiencia de 97.34% a 99.29%, e índice de producto no conforme, que disminuyó de 51.68% a 19.47% con respecto al año anterior. Esto se traduce en una mejora de la productividad, que pasó de 0.82978 a 0.98760, lo que a su vez mejora la percepción del cliente y la rentabilidad de la empresa. Además, la empresa mejoró los procesos de rellenado cambiando el procedimiento de soldadura SMAW por FCAW, lo que supondrá una mejora general en la producción total de la empresa.
CONCLUSIONES
La simulación del presente estudio demuestra las bondades de aplicar Lean Six Sigma en los procesos de reparación. Esta metodología, en conjunto con las otras herramientas descritas, mejoran notablemente la productividad, por lo que se infiere que su aplicación es válida para cualquier otra empresa de servicios de reparación industrial.
Mediante la correcta implementación de la metodología Lean Six Sigma, las empresas metalmecánicas pueden ser más competitivas.
La aplicación de la metodología Lean Six Sigma conduce a la mejora de la productividad en los procesos de reparación de los componentes e maquinaria pesada, pues mejora la eficacia y reduce el índice de producto no conforme.
La metodología Lean Six Sigma se combina con herramientas como el Kanban para mejorar la programación y la clasificación de los trabajos, y como el Heinjunka para nivelar la producción o reparación de los componentes de maquinaria pesada pertenecientes a la categoría V.
La ejecución de la metodología Lean Six Sigma reduce el índice de producto no conforme y evita demoras en la reparación.
La metodología LSS mejora el índice de cumplimiento o la eficacia en las áreas de la planta.
La mejora de los indicadores de productividad conduce a una mayor satisfacción de los clientes.
Por último, las experiencias exitosas con la metodología LSS pueden compartirse a través de publicaciones de tal modo que tengan un efecto multiplicador.